Back Story
The cruise industry gets all the attention, but the pandemic has impacted ferries and tour boats too.
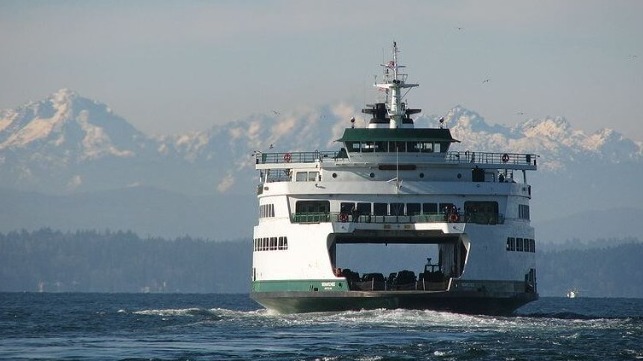
(Article originally published in Nov/Dec 2021 edition.)
For tour boats and harbor cruise operators, COVID-related health and safety concerns have led to a sharp drop in revenue from out-of-town visitors and corporate-event charterers. For ferry agencies, which don’t have the option of suspending operations to wait for lower case counts, COVID has been a genuine challenge for the safety and continuity of everyday operations.
At Washington State Ferries (WSF), the largest ferry system in the U.S., crew illness and post-exposure quarantines made it difficult to sustain minimum manning levels during the worst months of the pandemic. In January 2022, with the Omicron variant on the rise, the agency is seeing a resurgence.
"With Omicron, we've seen a big uptick in cases among crew and support staff,” says spokesman Ian Sterling. “It mirrors what is going on in the rest of the country. The good news is that even though there's a high case count, I'm not aware of any employees who are hospitalized or in serious trouble. That's good, because earlier in the pandemic we saw some people get really sick. We actually lost a couple of workers to COVID."
Control Measures
WSF has responded to the COVID threat with control measures including a federally-required mask mandate for indoor spaces. Like airlines and bus companies, ferry operators are covered by the U.S. Centers for Disease Control’s mask requirement for public transportation, which applies to all passengers in indoor settings. However, WSF has taken an “educate-and-encourage” approach to enforcement, and its staff provides free masks – not strict regulation.
"If you're getting on one of our boats, then yeah, you have to wear a mask," says Sterling. "But our employees aren't the mask police, and we've given them direction on how to approach people when needed."
Many passengers opt to drive aboard and stay in their cars, which lowers their risk of COVID transmission to near-zero with no masking conversations required. While walk-on ridership numbers have plummeted, driven down by work-from-home policies, WSF's car ridership has rebounded to near-normal levels.
Like many maritime operators, it’s taken a stricter line on crew vaccination. Last October, following a directive for all state agencies, WSF dismissed about 130 employees who opted out of vaccination – a seven percent reduction in its workforce, deepening an existing staffing shortage and prompting the agency to cut back on service.
Without enough mariners (especially in the engine department), WSF's ferries have been operating on a reduced schedule ever since. It will take at least until the summer to recruit enough people to fully man America's biggest ferry fleet, according to Sterling.
"Our vaccination requirement hasn't been a barrier for recruitment, since it's become the norm for a lot of maritime operators," he says. "There are many people who prefer working in an all-vaccinated workplace. It cuts both ways, just like it does in the rest of society."
Service Disruptions
To the north, just across the border, Canadian public ferry operator BC Ferries finds itself in much the same boat. Omicron is impacting staffing levels and, in conjunction with other factors, forcing schedule alterations.
"BC Ferries is anticipating that a combination of issues may result in unplanned service disruptions on all routes," the operator said in January, “among them the Omicron variant's potential to impact employee wellness, regular cold and flu season, severe winter storms, vaccination policies that have reduced crew availability and the global shortage of professional mariners."
The Staten Island Ferry system has also had a bumpy ride. In March 2020, as the outbreak began in New York City, the mayor's office announced that it would cut sailing frequency in half because of low ridership and staffing issues. Regular service levels resumed for daytime runs that summer, but full nighttime service was not restored until last August, 17 months later. The system has been gradually bringing operations back to normal ever since with some minor disruption due to staffing challenges in December.
The question of compensation for crewmembers – who’ve become front-line workers by necessity – has also played into the staffing challenge. A former union official told local media last year that New York City pays less than WSF for equivalent positions even though the cost of living in New York is considerably higher than it is in Washington.
“COVID has exacerbated the issue because people are now scared to come to work,” MEBA Secretary Treasurer Roland Rexha told the Staten Island Advance in September. “They’re dealing with the public on a daily basis. These people are coming in and keeping this operation going during the worst possible time,"
SOLAS Supply Chain Challenges
The pandemic has also added new challenges for the supply chain that keeps vessels moving safely. The recent surge in containerized cargo volume has affected every industry, and shipments of SOLAS equipment are just as vulnerable to rate hikes and disruption as everything else.
This inevitably raises cost, says safety flare manufacturer Wescom, and the challenge requires in-house expertise to keep supplies moving. For safety flares, which are pyrotechnic devices, there’s an additional wrinkle: A container full of IMDG Code Class 1 explosives can only be stowed safely in a few places aboard a boxship. Those approved slots are scarcer than ever in today's freight market.
"We're manufacturers and suppliers,” says Marketing Director Chris Feibusch, “but by necessity we're also excellent at Class 1 logistics. It's not a product that you can hold in a warehouse for any length of time since it has an expiration date, so the whole logistics chain has to be a very efficient and slick operation."
That logistics operation fulfills an essential need. When the worst happens, mariners need to get the message out and tell rescuers where they're located. Though it’s not complex or electronic, the simple red flare still saves lives every day, says Feibusch. This infallible signal requires no batteries, burns underwater and is universally understood.
"In a distress situation you need to be seen by rescuers,” he adds, “and there’s nothing that comes even close to a pyrotechnic flare for visibility. It’s more than 200 times brighter than the brightest 'electronic flare' strobe device on the market, and it’s instantly recognized by any member of the general public."
U.K.-based Wescom has been in the business since the days when sailors used cannon fire to call for help. Its PainsWessex brand was selling gunpowder as early as 1620 and filed the first patent for a distress flare in 1873. The latest version is familiar and reliable, but the manufacturing methods are up-to-the-minute: WesCom has fully automated its Bremerhaven production line for red flares, making it easy to increase or decrease production.
Feibusch says this flexibility was helpful in the first year of the pandemic when the cruise industry – a big customer – laid up ships and slowed its ordering.
Vertical Integration
As the maritime industry works through a period of unprecedented supply-chain disruption, Wescom has benefited from having an in-house manufacturing operation. Another SOLAS safety equipment manufacturer, Piraeus-based Lalizas, says its vertically-integrated operation has helped it ensure continuity of service for its customers during the pandemic.
"It’s a fact that the majority of our industry faced supply-chain disruptions during 2020-2021 when demand was unpredictable," says Chrysostomos Kavounis, Sales Supervisor for Lalizas. "Lalizas managed to overcome any obstacles thanks to the structure of the company – because we manufacture most of the components of our lifesaving equipment in house. We also took proactive action by having an adequate supply of raw materials."
Lalizas has also helped its shipping customers by taking on the logistics of refurbishing life rafts, which must be serviced regularly to meet SOLAS requirements (even during a global pandemic). "Our Fast & Independent Liferaft Exchange (F&I) is a radical game-changer, a simple and fast life raft exchange to keep the vessels compliant and in service," says Michalis Loupasakis, Maritime Companies Sales Manager. "F&I offers life raft compliance in the world’s key ports for a single fixed fee without need of a contract."
Unbranded Products
Much has changed in the safety business since Lalizas started up in 1982, and there have been many positive developments in technology.
But the company also sees a concerning trend in the passenger-vessel sector: A new crop of unbranded products is entering the market, targeted at budget-conscious operators. Additionally, name-brand lifesaving equipment is sometimes being overhauled by unauthorized shops, which may not have the skills to do the job correctly.
"Products such as inflatable lifejackets and life rafts are being serviced by inexperienced personnel, and in many cases they don’t use genuine spare parts," says Loupasakis. "We advise our customers to choose their partners wisely, based on the product and service quality and not just the price. When it comes to our field, the only focus should be on human lives." – MarEx
Paul Benecki is News Editor of The Maritime Executive.
Top image courtesy Tobias Eigen / CC BY 2.0
The opinions expressed herein are the author's and not necessarily those of The Maritime Executive.