Compliance Assurance
Shipowners want reliability when it comes to ballast water treatment systems. Failures can be costly.
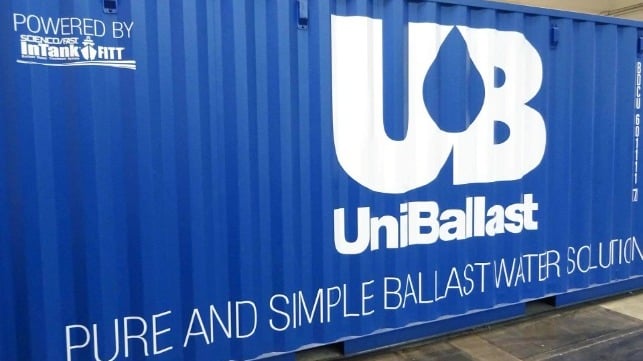
(Article originally published in Jan/Feb 2025 edition.)
Compliance is a top priority for shipowners, and that includes the handling of effluent and emissions.
Merchant ships have at least five major waste streams – exhaust, bilge water, solid waste, ballast water and sewage – each with stringent limits. Of these, ballast water requires treatment for almost every deepsea shipping application, and treatment failures mean costly delays in cargo operations.
Day-in, day-out reliability requires a working ballast water treatment system (BWTS) and long-term support from the OEM. For a busy merchant ship, that service relationship may make the difference between on-hire and off-hire.
LONG-TERM SUPPORT
Alfa Laval, the market leader in ballast water management, was among the first companies to begin developing a system for BWM Convention compliance. When the convention finally entered into force in 2017, it installed thousands of systems for shipping companies around the world.
Now that the big surge of retrofits is over, it's extended its lead as many other suppliers have pulled back or disappeared altogether. This long-expected market consolidation is making it harder for many owners to keep legacy systems in proper operation: Parts and knowledgeable service techs are tough to find at some of the OEMs that have disinvested from the sector.
At the same time as support is declining, port state-control inspectors are stepping up scrutiny of BWTS compliance. This is a challenging combination of trends as an unfixable BWTS is a costly liability if it halts a vessel's cargo operations.
Given the difficulty of maintaining unsupported equipment, some owners are deciding to replace their BWTS outright. Many are turning to Alfa Laval. The company has already replaced more than 250 systems from 30 different manufacturers with its PureBallast 3 system and expects that more owners will be coming.
"We see an increasing number of them making the tough decision to replace the system on board with a more reliable one," a company spokesperson said.
A big part of the reason, according to Alfa Laval, is stability and support. The company is the biggest BWTS supplier and one of the largest marine systems OEMs with service locations around the world and an ongoing compliance service package for peace of mind. "We believe it's key to have a close relationship with the BWMS supplier and go the recommended preventive maintenance way rather than the troubleshooting way, which has proven to be a lot more costly," the spokesperson said.
Alfa Laval continues to invest in R&D for ballast water treatment and has distilled customer feedback into a newly-revised model of its BWTS released in 2024. The system has proven itself effective in all water conditions, Alfa Laval says, even in challenging turbidity. It's also energy-efficient compared to other UV systems – a key factor for merchant ships as ballasting and deballasting occur during periods of peak power demand.
BALLAST WATER BACKUP
What happens if your ballast water treatment system does break down during in-port cargo operations? Do you have to stop loading in order to wait for spare parts and repairs?
Missouri-based SciencoFast has a solution that makes it easy for ships to carry on with their work even if the onboard BWTS can't keep up. This could save thousands of dollars a day in downtime costs for a busy merchant vessel.
SciencoFast has recently come up with a containerized version of its InTank ballast water treatment system, which chlorinates and treats water inside the ship's tanks. The original InTank is permanently mounted and treats ballast while under way, without any filtration. The containerized version keeps the same basic concept but is designed for temporary use while in port. Installation is as simple as hoisting the container on deck and running a circulation line into each tank, says Rudy Mes, SciencoFast's Senior Vice President of Operations.
The best news is that the containerized system is automated and self-monitoring. It takes care of everything – dosing, measuring and neutralization. After enough time has passed for treatment and discharge, it produces a certificate of technical compliance that the crew can show to the authorities to demonstrate proper operation. None of these steps requires any specialized knowledge or additional effort on the part of the crew.
"It shows which tanks are treated, what level of the chemical was injected, how long that was in that tank, when it was neutralized, and what the remaining total residual oxidant (TRO) was after neutralizing," says Mes. "So that's basically a guarantee for the vessel owner that the system has worked and that the water is fully treated and safe to pump overboard."
The system is designed to be light, compact and usable anywhere, on any vessel up to 50,000 dwt (or larger, with multiple units). The treatment chemical is simply industrial bleach, a standard product available in any port. And its electrical load is exceptionally low, saving power during port calls when the vessel's generators are working hardest.
SciencoFast's ultimate hope is to mount the containerized treatment system on a tank barge and provide ballast water treatment as a service. The barge would pull alongside the ship; the ship would deballast into the barge's tanks, and the barge-mounted treatment system would sanitize the water. There would be no waiting at all. The ship would deballast into the barge at full speed, and the water would be treated later. For minimal fuel consumption and emissions, the treatment could even be done when the barge gets back to the pier and plugs into shore power.
French water system manufacturer BIO-UV has been making UV treatment systems for water disinfection for 25 years.
It started with shoreside treatment applications, then branched out into solutions for BWM Convention compliance, adapting proven technology to a marine operating environment. It's well known in the yacht, workboat and specialty-vessel markets for its compact UV-based treatment units (including the smallest BWTS commercially available).
BIO-UV is quite active in the American workboat and naval markets. Last year it delivered six of its BWTS units to a leading American offshore vessel company, and it has a new system for the U.S. Navy in the operational test phase.
Combining its experience in ballast water treatment and shoreside water systems, BIO-UV recently branched out with a purpose-built pool and spa water disinfecting system for cruise ships. For BIO-UV, it's also a return to familiar ground: The company's very first product was a UV disinfection system for swimming pools, and its systems equip more than 6,000 public pools around the world.
Based on the same technology as BIO-UV's BWTS, the new device uses UV to kill at least 99.99 percent of all microorganisms in the water from a cruise ship's pools, hot tubs and spas, a rate far higher than chlorination can achieve. It's certified to treat cryptosporidium, a microscopic parasite that can cause outbreaks of gastrointestinal illness on cruise ships.
With a UV system installed, the cruise ship's recreational water supplies can run with 75 percent less chlorine, reducing the unwanted byproducts of chlorination. When chlorine reacts with biological matter in the water, it forms chloroform and chloramines, common and irritating pool water contaminants that are known to have human health effects.
By maintaining high levels of disinfection while reducing the byproducts of treatment, the cruise operator can offer passengers a better experience, the company says.
PRACTICAL EXPERTISE
Fort Lauderdale-based Headhunter is a well-known name in marine sanitation with deep roots in the demanding luxury yacht segment. Its team builds and installs complete black- and graywater systems for vessels of all kinds for capacities up to 50,000 gallons per day.
Some of its biggest contracts are for the U.S. Navy's Military Sealift Command, which uses Headhunter's TidalWave HMX system aboard the Expeditionary Fast Transport (EPF) catamaran and the follow-on hospital ship version, the Expeditionary Medical Ship (EMS).
A big driver of Headhunter's success is the quality of its aftersales service, which is key for military customers. "We've received a lot of positive feedback from MSC regarding our technical support," says Headhunter President Mark Mellinger, "which takes place around the world. The Philippines is a popular destination, and we've provided service in Croatia, Singapore, Bahrain, Italy, France and the U.S. West Coast. We've never missed a service call for them."
Headhunter's expertise is so well known that Mellinger was selected to advise the U.S. delegation to the IMO. "I was invited to join a subcommittee called PPR – Pollution Prevention and Response – and we've worked on rewriting the annex on sewage (MARPOL Annex IV)," he says. "It's a privilege to be invited, and I'm the only U.S. manufacturer in our group."
His input has had a meaningful effect on the details of the regulation. Mellinger gave the subcommittee practical guidance on the order of operations for blackwater treatment, helping write rules that better fit the real-world design of sewage systems for use in international waters.
Mellinger has also encouraged the subcommittee to base its requirements on how many people are going to be aboard a vessel, not just on vessel size. Current regulations determine the required size of the treatment system by gross tonnage, which does not have a direct relationship with the crew and passenger count.
"People are what makes sewage," he says. "You could have a 400-gross-ton ship – the size where the rules take effect – but it might only have two or three people, especially now with more autonomy on board. If the new rules allow it, you could shrink the sewage system down to a size that's actually appropriate to the smaller crew. That would reduce displacement and power consumption, creating savings on fuel and emissions."
The opinions expressed herein are the author's and not necessarily those of The Maritime Executive.