Lifting Smarter
Innovation thrives in the crane and heavy lift markets despite COVID-related constraints.
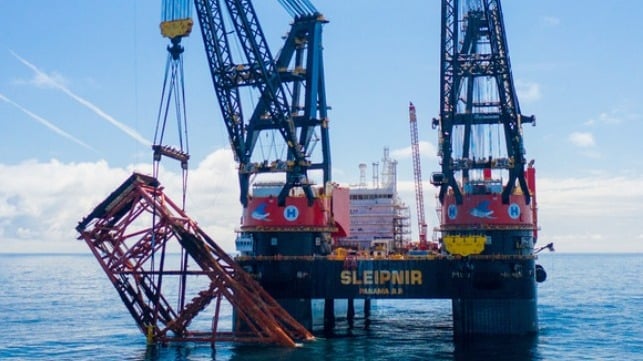
(Article originally published in Sept/Oct 2020 edition.)
Recent years have seen new and exciting lifting technology come to the forefront with the completion of record-breaking and increasingly impressive heavy lift operations, both shoreside and at sea, expanding operator capabilities and improving efficiency.
It’s a market driven by innovation. The nature and scope of operations are changing globally and often require a custom solution to meet new requirements. This results in higher-capacity equipment that is both lighter and more versatile. With VR technology, integrative software applications and readily available bandwidth, support can be offered remotely on a level not seen before.
Nonetheless, the market continues to reel from the effects of COVID-related constraints. According to IHS Markit’s “ContructionVesselBase,” heavy lift vessel utilization currently stands at just 33 percent due to the slowdown in offshore field development work and resultant drop in fixed platform installations. This has forced these assets to expand into more promising and growing markets like decommissioning and offshore wind.
Record Lifts
Despite the downturn, there have been a number of high-profile and noteworthy projects delivered already this year with more on the horizon.
Heerema Marine’s semi-submersible crane vessel Sleipnir, for example, has had a massively successful and busy year so far. Less than a year after setting the world record for lifting a 15,300-ton module offshore for the Noble Energy Leviathan project, the vessel – named for the eight-legged horse ridden by Odin in Norse mythology – set another record for the largest single jacket decommissioning lift for Vår Energi in the Norwegian North Sea at 8,100 tons. Within a month she broke that record with another North Sea lift, this one the Brent Alpha jacket weighing in at 10,100 tons.
Each of these lifts was completed using twin 10,000-ton Huisman tub cranes, the largest in the world. Based on a slew bearing principle, these next-generation cranes provide a lower center of gravity and offer lower weight in a smaller footprint than existing tub crane designs. Uplift forces are absorbed by the slew bearing, and the unit’s maintenance requirements are low as all rotating parts are enclosed.
Importantly, the drive system is electric, which eliminates the risk of hydraulic oil spill. This further reinforces Sleipnir’s claim as being the world’s most sustainable crane vessel with dual-fuel engines running on either MGO or LNG to reduce emissions during operation.
Offshore Wind Equipment
While offshore oil and gas exploration and production may be in decline, the offshore wind industry continues on a roll – providing the heavy lift market with ample opportunities as the demand for renewable energy grows.
Netherlands-based Jumbo Maritime, for example, recently completed a loadout in Vlissingen onboard the vessel HLV Fairpartner bound for the Yunlin wind farm, a 640-megawatt project offshore Taiwan. The Fairpartner is one of Jumbo’s J1800 class vessels with twin 900-ton cranes capable of working in tandem up to 1,800 tons.
Jumbo is no stranger to transporting unique cargoes, and the loadout consisted of ten transition pieces, each of which sits between the monopile and the turbine section of an offshore windmill and provides the main access point for maintenance personnel. This particular loadout was unique due to the number of pieces loaded.
Aside from sufficient cargo capacity, a heavy lift vessel also requires the ability to complete a long sea transport. The Netherlands to Taiwan is over 11,000 nautical miles! There aren’t many vessels in the world that have the combination of cargo capacity and range to complete such a project, and Jumbo operates six of them.
If transporting large offshore wind structures to remote locations is one challenge, loading them onto ships is another. Not to be outdone in this department, Liebherr has taken its successful MTC 78000 offshore mast type crane and adapted it to create one of the most innovative rail-mounted gantry cranes in the world, the TCC 78000 traveling cargo crane. Located in the port of Rostock, Germany, the crane is strategically placed to take advantage of the deep-draft quay and provide access to land and sea connections.
The TCC 78000 has a unique combination of high capacity and hook height. It’s capable of lifting 1,600 tons at 36 meters and has a raised boom jib height of 164 meters. It runs on a double-trolley track 420 meters long and has an under-crane clearance of 17 meters. According to Winston Ziegler, Senior Sales Manager for Liebherr Maritime Cranes and Reachstacker for the U.S., it’s the largest structure in northeast Germany.
The TCC 78000 was recently used to load 72 monopiles bound for the Kriegers Flak wind farm off the coast of Denmark. The field will be the largest in the Baltic Sea and increase Denmark’s production of electricity from wind by 18 percent – enough to power about 600,000 homes and contributing significantly to the country’s goal of achieving fossil-free living within one generation.
From Sea to Space
On the U.S. side of the pond, Liebherr has installed the world’s largest mobile crane at Port Canaveral in Florida. The custom-designed LHM 600 crane is fitted with a special double-layer winch to help accommodate the maximum lifting height of 70 meters. Its 154-ton SWL (safe working load) makes it the largest capacity crane in the state.
While the crane will serve a variety of functions within the port, from containers to various heavy cargoes, its most impressive use is handling the Falcon 9 booster rockets for SpaceX, which are approximately 45 meters tall and weigh about 30 tons. The rockets are landed on the recovery ship OCISLY (“Of Course I Still Love You”) after a launch, then towed back to port. A new type of crane was needed, and the LHM 600 delivers.
A version of this same crane with a different configuration is installed in New York harbor and is the largest floating bulk-handling crane in the world and the first of its type on a floating barge. Operated by SIMS Metal Management, this LHM 600 has a maximum capacity of 75 tons and is used for scrap handling. The barge mounted configuration allows for quick setup while requiring no changes to the existing infrastructure
COVID-Inspired Innovations
In response to the COVID pandemic, Liebherr accelerated the delivery of its Remote Service App, developed to enable faster trouble shooting. It came in handy when Liebherr delivered a new LHM 420 mobile harbor crane in August to Euroamerica S.A in Argentina.
Normally the assembly process would be completed under the guidance of a delivery engineer, but COVID-related travel restrictions made direct onsite management unfeasible. So the company leveraged its new remote capabilities to assist, ensuring the crane was not just assembled according to its rigorous specifications but completed on time and on budget – setting a remarkable precedent for similar operations in the future.
Nonetheless, the pandemic is taking its toll, especially on the ship repair market. According to Clarksons Research, it will result in a decline of more than five percent in seaborne trade and 10 percent in ship repair activities. With fewer ships sailing and deferrals of special surveys, repair yards need to turn vessels around efficiently in order to make a profit.
Enter Syncrolift. Offering a truly innovative lifting solution, Syncrolift provides a system of ship lifting, transfer and fast-docking to help reduce vessel time out of the water and ensure greater space efficiency within the yard. This improves lead times and allows for tighter management of repairs.
Recently a Syncrolift shiplift system was delivered to Norwegian repair yard Skarvik. Requiring no wooden blocking, the system integrates support arms that increase versatility in a simpler solution, designed for vessel repair operations. Ship washdown can be performed on the steel decking of the platform without compromising stability. Water is quickly removed by tilting the platform using the Syncrolift control system, and special channels direct waste from the vessel into tanks on land.
While ownership has changed over the years, the company has a long history with over 240 shiplifts installed worldwide. Initially developed in 1953, the system has undergone constant improvement with the company continuing to offer support for all of its installed equipment. In keeping with the times, training and support is offered using cutting edge technology including virtual reality simulations.
Ongoing Innovation
While the global market for heavy lift vessel utilization may be down currently, it will be those companies that are lifting smarter and pushing the envelope of technology that will be well positioned to dominate the market in the future.
Sean Hogue is a Master Mariner and Vice President of Marine Assurance at Baker Marine Solutions. This is his first appearance in the magazine.
The opinions expressed herein are the author's and not necessarily those of The Maritime Executive.