DESMI Offers Simple Power Management for Energy Efficiency Compliance
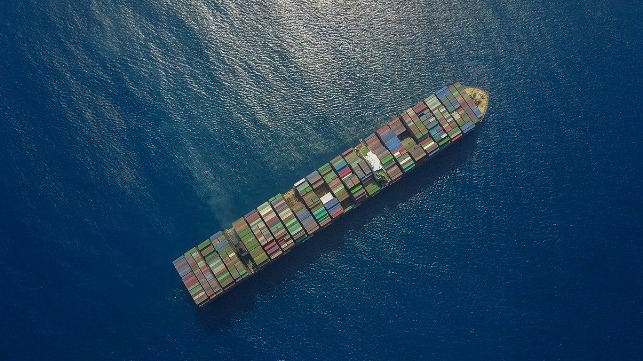
Shipowners and designers need to comply with the maritime industry’s ever-stricter regulations for reducing CO2 and greenhouse gas emissions. These new rules include the long-term Energy Efficiency Existing Ship Index (EEXI) and the Energy Efficiency Design Index (EEDI) included in the IMO’s strategy for reducing greenhouse gas emissions.
The new measures will require all ships to calculate their EEXI following technical means to improve their energy efficiency and to establish their annual operational carbon intensity indicator (CII) and CII rating. Carbon intensity links the greenhouse gas emissions to the amount of cargo carried over the distance traveled.
Shipowners can implement several technologies to meet the requirements. One of these includes Energy Efficient Technologies, which focus on the improvement of fuel consumption in auxiliary engines. The DESMI OptiSave™ Energy Saving System offers a cost-effective solution for compliance. It supports ship owners and designers to meet the requirement for the reduction of CO2 emissions. Such systems can be integrated at the new build stage or as retrofit applications, fully integrated within the overall control systems. The OptiSave™ system is also suitable for vessels that will continue to be in service beyond 2030.
“You should install it regardless of the rules and regulations,” says John Nielsen, DESMI’s Key Account Manager of Marine and Offshore. “At the end of the day, you want to save fuel. And in doing so you help save the planet.”
DESMI’s commitment
When developing solutions to help improve vessels’ operational performance and carbon footprint, DESMI’s design engineers realize there is not a “catch-all” solution for all ships.
“Fleet and operational patterns are so diverse nowadays. So, we tailor-make our OptiSave™ solution for every ship, so it achieves the highest possible performance,” says John Nielsen. “We are here to support our customers with the best possible solution.”
The OptiSave™ system was developed with the sole purpose to achieve the highest possible energy saving for centrifugal pumps and axial fans. The OptiSave™ system is modular, meaning that it is expandable, and several other applications can be included.
The DESMI OptiSave™ approach
The energy savings achieved using the DESMI OptiSave™ system often significantly exceed the pre-calculations made at the point of designing the system.
The background and optimization of speed of the centrifugal machinery is based on Affinity Law, which implies that as the shaft speed or impeller diameter changes, the horsepower changes in proportion to the cube of the change in shaft speed or impeller diameter. In other words, impeller diameter is constant, so by varying the speed, the power consumption will also vary by ~3 times.
“Basically there is a relationship among flow, pressure, and power. So, if you reduce the speed, then you reduce the power,” says John Nielsen.
How it works
Sea cooling water systems and pumps are designed for operation in 32°C seawater and 100 percent engine load. Normally, they run as if this condition is permanent, all over the world. But actually, there are only a few hot spots where these conditions are present. Otherwise, it is usually lower or much lower.
A standard vessel cooling system operating in these conditions around the world will be absorbing too much energy 95 percent of the time. The DESMI OptiSave™ system can regulate the energy consumption according to the actual cooling demand – thereby saving fuel as well.
The OptiSave™ system improves the ship’s efficiency of the sea cooling water pumps, depending on the sea water inlet temperature and the overboard sea water temperature. Using the OptiSave™ system allows for an increase in the overboard temperature, increasing the heat exchange capacity, and cooling capacity, making it possible to reduce the power consumption to a minimum.
A tale of two vessels
One can see the effectiveness of the DESMI OptiSave™ system by comparing the journey of two identical vessels traveling from Shanghai to Denmark. One vessel has no system, and the other one has a DESMI OptiSave™ system.
Already in Shanghai (water temperature 24°C), the OptiSave™ ship’s pump speed is at 56 percent. Where the no-system vessel is running at 100 percent pump speed and 90 kW usage. The OptiSave™ ship is only using 22 kW.
When reaching the Mediterranean (20°C), the pump is running at half the speed of the “normal” cooling pump system of the OptiSave™ ship.
By the time the ships reach Denmark, the accumulated savings achieved by the DESMI OptiSave™ system is 52,000 kWh, or 75 percent savings.
The DESMI OptiSave™ system for seawater
The OptiSave™ system controls the seawater cooling pumps by changing the pump speed according to the actual cooling capacity demand at any time, thereby achieving maximum power savings.
Each seawater pump has its own individually mounted, marine-approved variable frequency drive (VFD) for pump speed/flow regulation. A master control panel is in turn being fed with process information from the system’s temperature and pressure transmitters. Sensors on the seawater inlet pipe measure the temperature to be able to control and calculate the amount of seawater needed to maintain adequate cooling of the freshwater side.
The temperature transmitters on the seawater outlet pipe are used to monitor and maintain a maximum discharge temperature. This is done to be able to extract the most energy out of the seawater as possible.
DESMI can also mount additional pressure sensors on the seawater side to measure the differential pressure over the central seawater coolers. The differential pressure measurement has the benefit of giving the OptiSave™ system the ability to prompt the duty engineer when back flushing of the coolers is necessary.
The DESMI OptiSave™ system for Low Temperature Fresh Water Cooling
DESMI also offers an OptiSave™ system for Low Temperature Fresh Water (LT/FW) cooling where the control is formed by using pressure, temperature, and flow measurements to obtain the lowest possible energy consumption on the main LT/FW pumps.
On almost all commercial vessels, the LT/FW cooling system is designed for a cooling water temperature of 36°C at outlet (inlet to components). This temperature is traditionally controlled by using a PID controller linked to a 3-way valve with a valve actuator.
The 3-way valve will mix the hot LT/FW cooling water returning from components with the colder water coming from the main heat exchangers and keep a constant temperature of 36°C.
As opposed to the open seawater cooling system, the LT/FW cooling water system is closed and needs a certain amount of pressure to function.
When the OptiSave™ system is installed in an LT/FW application, the frequency converters will be programmed to a specific minimum RPM. This RPM corresponds to the minimum pressure setting where the cooling water system will perform as designed. The system maintains pressure using differential pressure measurements.
To monitor and control the performance of the system with lower pressure and hence reduced flow, a number of pressure transmitters and temperature transmitters are installed. Each of these sensors have the ability to control the frequency converters in the LT/FW system.
As an added function, the OptiSave™ system is designed to work with the temperature requirements set forward by MAN and by WinGD.
It is possible to increase the overall energy savings of the LT/FW cooling water pumps by adding shutoff valves for the individual components in the LT/FW system. The function of these valves is to close the waterflow through the components, when not in operation, and thereby reduce the flow further. As a result, the power consumption of the main LT/FW cooling water pumps is reduced.
Engine room ventilation system
The DESMI OptiSave™ system also works in a similar way for the ventilation system in the engine room. Each fan has its own individually mounted frequency converter and a common control PLC for fan speed/air-flow regulation.
Each fan’s VFD operates with information from the temperature sensor in the engine room, differential pressure measurements, and main engine fuel index measurements.
The system can also control the fire dampers according to the operational condition of each fan. Dampers can also be manipulated in manual mode. As an extra option, the system is also designed to control the opening and closing of the exhaust louvers in the funnel. This function ensures better control of differential pressure (overpressure) in the engine room.
The fans being operated by the OptiSave™ system will be operated at the same speed if running in AUTO mode.
Reliable operation – also remotely
The OptiSave™ master control panel includes a color touchscreen for easy monitoring and system condition. It also includes several fail-safe modes. For example, if a wire for a sensor breaks, or if the master control panel is powered off, the pump speed increases automatically to 100 percent to ensure sufficient cooling.
Furthermore, all alarms and events are logged and can be transferred to the alarm system on the vessel. Remote support is also available for data logging and monitoring performance data – from any remote location in the world, no matter where the ship is sailing. Remote surveillance allows not only fault-finding but also to monitor the performance of the system, says John Nielsen. “We do not need to go on board,” he says.
The DESMI OptiSave™ system can be installed and commissioned in just four to six days, depending on the size of the system. It does not need modification of the vessel’s safety functions but needs only minimal modification to the existing equipment.
“We can do turnkey solutions, we do the pre-calculations, we do the production and supply the equipment for the installation, and we do the commissioning,” says John Nielsen. “There is no need to dry dock, and the installation can be done when the vessel is in service.”
The installation and DESMI commitments
Currently, some 700 OptiSave™ systems are operating across different categories of vessels around the world.
One of these is Maersk Tianjin, an oil and chemical tanker, from 2016. In that case, it was reported by Maritime Hawai’i in 2017, that a DESMI OptiSave™ cooling water system saved the vessel an estimated 116 tons of fuel per year. This resulted in 359 tons of CO2 savings/year and considerable fuel cost savings.
For Maersk Tianjin’s cooling room fans, the OptiSave™ system saved an estimated 32.4 tons of fuel per year, with 175 tons of CO2 emissions saved.
As part of DESMI’s commitment to our clients, we provide calculations that enable our clients to make decisions.
“A shipowner should care about the total costs of operation, and he should look for opportunities for savings,” says John Nielsen. “This equipment is easy to install. It’s affordable. It’s one of the cheaper solutions compared to many of the other energy-saving solutions available in the market, today.”
For more information, please visit DESMI online.
The opinions expressed herein are the author's and not necessarily those of The Maritime Executive.