Tools of the Trade
Navigating a ship is tricky business.
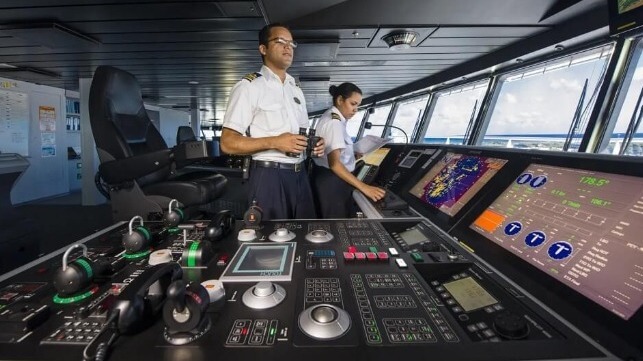
(Article originally published in Jan/Feb 2023 edition.)
There are more ships sailing than ever before with the global commercial fleet growing by 63 million dwt in 2021 alone, leading to congested waters and tighter quarters.
At the same time, the average age of the global fleet is steadily growing, reaching 21.9 years in 2021 according to UNCTAD. A key driver, reportedly, is uncertainty in the bulk sector over future technological developments, future fuels and changes to regulations surrounding emissions. This means a “sit-back-and-wait” approach to upgrades and innovation – especially in the area of bridge equipment.
However, the news isn’t all so grim. According to the Allianz 2022 Safety Shipping Review, which looks at trends and developments in shipping and safety, there were 54 total losses (vessels over 100 gross tons) in 2021 – a significant reduction in the 10-year loss average of 89 per year. It’s all the more impressive as the number of ships worldwide has nearly doubled to 130,000 from 80,000 some 30 years ago.
So the industry is obviously doing something right.
Advanced tracking and collision-avoidance aids are becoming de rigueur, and a digitally connected fleet allows for better communication, tracking and decision support. These tools enable the front-line personnel – the ship’s navigators – to sail the seas safely and efficiently.
And the tools keep getting better.
The Integrated Bridge
The most significant technological advancement of the last 30 years is the Integrated Bridge System (IBS).
IBS is defined as a combination of interconnected systems that allow centralized access to sensor information or command/control from workstations with the aim of increasing safe and efficient ship operation by suitably qualified personnel. Performance standards for its use were adopted by the IMO in 1996 with Resolution MSC.64(67) and the December 2000 revision to SOLAS updated Regulation 19 to include IBS requirements.
An IBS system can manage multiple operations including communications, passage planning, cargo operations, machinery control, and safety and security. In general, it includes functions such as autopilot, gyros, ECDIS, radar/ARPAs, conning display, position-fixing systems, PDS, GMDSS and steering or thruster controls. These are interconnected so that various functions are available seamlessly at workstations around the bridge.
More ships than ever are fitted with a full IBS package, and Kongsberg Maritime is the front-runner in the market. With more than 50 percent of the world’s navigators trained on a Kongsberg simulator, the system is familiar to most. And while it has all the standard features – ECDIS, radars, one-person control capability – the company has so much more available.
Advanced decision support and augmentation tools such as Intelligent Awareness are part of the company’s Ship Intelligence suite – remote and autonomous solutions for commercial applications. Combining multiple sensors with intelligent software, IA is designed to mitigate the risks navigators face, especially in poor weather conditions, congested waters or at night. Essentially, it gives the master and bridge personnel a heightened understanding of the ship’s surroundings.
Using light-detection and ranging (LIDAR) technology, the system pairs with GPS data to build a 3D environment. Additional spatial information is provided using HD cameras, and all of this is combined using data fusion to provide a complete overview of the surroundings.
The more information available to the navigator, the better the decisions they can make.
Staying the Course
Another innovative player in the bridge systems space is Sperry Marine.
The company’s approach is to make the bridge as compact and networked as possible with systems focused on a safe user experience. The VisionMaster Net bridge system features large flat-panel screens but fewer console cabinets than before, enabling the bridge to be designed and laid out for maximum ergonomic efficiency. Because the system uses a single Ethernet ring, the bridge can provide an optimized working environment in which navigators can move around as needed with equipment able to remotely provide views of critical screens such as radar and ECDIS.
Ever innovating, the company has a progressive outlook on the evolution of bridge technologies currently taking place. Managing Director James Collett says, “The bridge of the 2030s will be transformed compared to today. It will be simplified, location-independent and highly automated with better information flexibly available to the people who need it.”
As part of this evolution, Sperry has recently launched the NaviPilot 4500N, designed to deliver improved course-keeping with reduced fuel consumption and a lower workload on the bridge. It builds on the highly successful 4000 platform and has the ability to adapt in real time to external factors such as trim changes due to fuel usage, different cargo-loading parameters and longer-term changes in behavior as the vessel ages. It can also optimize rudder lift and drag to smooth performance, particularly in rough weather.
The end result is an increase in fuel efficiency and a decrease in bridge officer workload – a winning combination.
Company management has also restructured, placing the Sperry defense programs with Northrop Grumman in the U.K. and leaving Sperry Marine to focus entirely on commercial shipping, which positions the company for the digital transition and tightens its focus on safe, efficient and low-carbon navigation.
(Re)Structuring for Success
A new name in the field, SEAM, has roots back to 1988 when it was developed as a continuation to ABB Marine. You probably know them by their most recent name, Westcon Power & Automation AS.
With a clear focus on zero-emission solutions for the maritime industry, SEAM specializes in hydrogen, full-electric and hybrid installations. Offering the complete package including switchboards, power management and drives, the company features its e-SEA® Bridge line to control it all.
Including a bridge remote system, control desks and navigation system, the e-SEA® is implemented as a workplace configurator with ergonomics designed to create a more user-friendly and safe working environment for the navigator. Remote control interfaces allow for greater integration between systems and provide opportunities for SMART and automated tasks, allowing the crew to focus completely on the task and situation at hand.
e-SEA® was based on the experiences and feedback of multiple navigators, who’ve been a vital part of the development – especially in terms of console-design and control placements. It improves efficiency by integrating navigation functions and equipment so that safe and efficient operation of all bridge procedures is performed with a minimum of steps and movements.
Pair this solution with the in-house automation system – the e-SEAMatic®. Installed in hundreds of vessels since 2008, it’s a platform used for many different systems and continuously updated. e-SEAMatic® also connects to the Energy Power Management System, of which SEAM is a world-leading supplier of fully electric and hybrid maritime systems.
The company is currently finishing system delivery and integration for the MF Hydra – the world’s first hydrogen-operated ferry, owned by Norled – an exciting leap forward in renewable transportation solutions.
Chief Operating Officer Otto Kock says, “Our ambitions are to tailor to customers’ growing demands and need for novel and disruptive technology. The pursuit of the ‘green shift’ is challenging but productive for technology developers.”
Systems designed to work together provide the greatest flexibility, and the e-Sea line offers an advanced approach to vessel operations.
Bolt-On Bridge Capability
Sometimes vessels need more capability than they currently have. A change of trading area or contract-specific requirements mean they need a little something extra. When it comes to adding advanced radar augmentation, the sigma S6 suite from Rutter is the best there is.
The Rutter system adds a single piece of hardware that interfaces with the ship’s radar. Depending on the requirement, it then adds advanced capabilities such as ice detection, oil-spill detection, wave analysis, current monitoring, small target detection and more. This provides enhanced situational awareness that promotes safety, security and efficiency in a variety of maritime situations.
The system leverages X-Band radar technology installed onboard and can provide a standalone antenna where needed as well as a standalone monitor that displays a base layer followed by any of the other layers the client requires. It also features a remote login for shoreside connectivity and decision-making.
This easy-to-upgrade capability has been added to such vessels as the Sir David Attenborough, one of the most advanced polar research vessels in the world, designed to support science in extreme environments. A range of scientific facilities, instruments and laboratories enables scientists to conduct multidisciplinary studies of the ocean, seafloor, ice and atmosphere. Marine robotics and remotely operated vehicles – including the now infamous Boaty McBoatface – capture data from the deep ocean and previously inaccessible locations under the ice.
Two of Rutter’s sigma S6 systems will be installed on the ship: sigma S6 Ice Navigator™ and integrated sigma S6 Oil Spill Detection and WaMoS® II Wave and Surface Current Monitoring. The ice system will provide imaging and detection for safe navigation in polar seas. The objective of the integrated oil and wave/surface current measurement system is to collect data for scientific research.
Bold New Horizons
Marine technology is advancing at a rapid pace. Digitization, automation and the Internet of Things gives the modern seafarer more information and decision-making support than ever before. This helps drive efficiency and safety and ultimately gets the industry closer to its ambitious “30 by30” goals.
These technologies must be built on a firm foundation, and the bridge systems described here make up that foundation. The changes taking place in shipping require navigation system and service providers to come up with new approaches to vessel operations including standardization and simplification of the modern bridge portfolio. Increased industry collaboration and higher levels of automation ultimately result in a better user experience and safer seas.
No more sitting back and waiting to see what happens.
Master mariner Sean Hogue is Senior Vice President of Baker Marine Solutions.
The opinions expressed herein are the author's and not necessarily those of The Maritime Executive.