The Pandemic's Effects on the Ship Repair Industry
The pandemic has brought not just economic, social and physical disruption but technological disruption as well. And that may be a good thing.
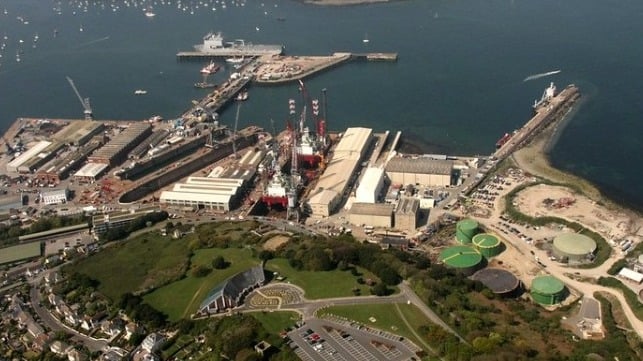
(Article originally published in May/June 2020 edition.)
The word “disruption” has been used and overused to the point of becoming a cliché, but there's one area of the maritime industry that it seems to have bypassed so far: ship repair. Not anymore. Along with the many disruptions that the COVID-19 pandemic has caused, you can now add new technologies to the list.
The virus has forced yards to rethink their operations and interactions. Detyens Shipyards in the U.S., for example, has been operational throughout the pandemic and credits preventive measures taken early for preventing an outbreak among its workforce. However, Brad Kerr, Director of Sales & Marketing, says some of the measures were met with initial resistance.
“We implemented a very strict entry policy to the shipyard for any outside contractors, tech reps and even customers, for that matter,” he explains. “We did that immediately and had a lot of pushback at first. But because we were so aggressive from the very beginning in controlling access to our shipyard, we've been able to stay ahead of any kind of outbreak curve. Other U.S. yards have had cases.”
Kerr believes that strengthening the yard's entry policy and focusing on health and cleanliness bring benefits that will endure. “We think there will be a smaller, more efficient, better workforce, so some good has come out of this tragedy.”
Essential Services
This year the repair and sustainment projects completed by Fincantieri in the U.S. were more important than ever as many of the vessels were needed to transport critical goods and materials to combat the virus. Fincantieri Marine Group’s three shipyards – Marinette Marine, Bay Shipbuilding and Ace Marine – were all designated critical workplaces with employees’ health safeguarded through multiple measures including frequent daily cleanings of high-traffic areas, social distancing and prohibiting nearly all travel.
The USCGC Mackinaw recently underwent drydocking at Fincantieri Bay Shipbuilding. It was the first time her azipods had been removed, and Julie Koch, Manager of Contract Services, says the yard had to build a higher block height to accommodate them. Working with ABB, the maintenance was completed within the first 30 days of the 84-day contract, which also included box cooler disassembly and cleaning, hull painting, bow thruster maintenance and other services.
Pacific Fishermen Shipyard in Seattle was also deemed an essential service, maintaining multiple high-speed ferries and emergency watercraft along with a large number of seafood harvesting vessels. The yard features experienced shipwrights, machinists, boilermakers and electricians at its Lake Washington Ship Canal facility, and the experienced caulkers on staff in their oakum loft are a diminishing resource in the wooden boat trades.
The yard was busy over the last year with everything from routine drydockings to main engine rebuilds and repowers. Notable activity included installing new twin Cummins QSK19 diesels on The Boat Company’s southeast Alaska eco-excursion vessel Liseron, replacing her WWII-era Minesweeper Cleveland 268A diesels, and the overhaul of the single Caterpillar 3512 main engine on the fishing vessel Northwestern of “Deadliest Catch” fame.
COTECMAR in Colombia has continued operations during the pandemic to maintain its role supporting defense and commercial shipping, adopting all the measures recommended by local health authorities to minimize the risk of contagion from COVID-19. The yard offers repair, maintenance, conversion and modernization services for a range of vessels at its Cartagena facility near the Panama Canal. It plans to expand drydock capacity to 18,000 tons with a new floating dock.
Works recently undertaken include tug conversions from conventional to azimuth propulsion and bow-design modification for commercial vessels. For the installation of ballast water treatment systems, COTECMAR offers a full scope of work including 3D scan, concept design, detailed engineering and installation.
Another active segment for COTECMAR is the modernization of tuna fishing vessels including upgrading bridge navigation and control systems and prefabricated accommodation modules for easy mounting and dismounting. This is in addition to electrical and hydraulic systems' analysis and enhancements to increase performance and minimize fuel consumption.
Sefine Shipyard in Turkey says it’s functioning at full capacity as a result of taking early precautions and continued vigilance during the pandemic. The yard's electrical workshop, set up in late 2018, has performed repairs and overhauls on over 1,000 motors, and ballast water treatment system and scrubber projects are continuing.
In the U.K., A&P Group has deployed strict COVID-19 measures at all three of its facilities. During the pandemic, it’s continued to deliver complex, large-scale projects with minimal disruption to labor.
A&P Falmouth has continued to provide critical support to the Royal Navy and Royal Fleet Auxiliary with the workforce commencing a major refit to RFA Mounts Bay and delivering essential repairs to HMS Scott. At A&P Tyne, the team completed installation of cable repair equipment to Prysmian’s North Sea Giant, essential to the safe and continuous power of the National Grid. A&P Tees completed vital maintenance and repairs for suction dredger Arco Beck including urgently needed stern seal renewals.
Technological Disruption
In the technology space, subsea and offshore solutions provider Unique Group has partnered with Tugdock to bring a new, patented modular floating drydock concept to market. Tugdock’s system comes in sizes ranging from 12x12 meters to 100x100 meters with a total lift capacity up to 15,000 tons. The company says it can lift vessels and other floating structures out of the water at a fraction of the cost of standard drydocks.
The system is transportable in standard shipping containers with components assembled in customized dimensions to best suit the size and shape of the vessel to be docked. It’s designed for shipyards, ports and the assembly and loadout of structures associated with floating offshore wind farms.
The system can be designed to DNV GL rules for floating drydocks. The deck of the Tugdock is sealed with a small bund wall around the perimeter and also has large sump drains with particle filters. When a vessel docks, the valves on the drains will be open to the sea, but once the vessel is in position the drain valves will be switched to divert any deck run-off into a sump. The sump will automatically pump the run-off ashore or to an alongside floating tanker.
Any normal work that vessels undertake while occupying floating drydocks can be conducted. It can be moored to a quayside or secured by piles or spud jacking legs. Lifting time for a standard harbor tug is around 30 minutes.
Digital Disruption
In the digital disruption realm, Silicon Valley-based Stottler Henke Associates has been awarded a contract with the U.S. Navy to demonstrate a critical chain and critical path scheduling system for surface ship maintenance operations. Stottler Henke’s solution is based on its Aurora™ intelligent planning and scheduling system.
The project will entail a series of demonstrations and government tests to verify the system’s ability to solve large, resource-constrained scheduling problems, generate numerous reports and displays to provide an integrated picture of the Navy’s surface ship maintenance demands, support tens of thousands of users and provide system administration tools. If the evaluation is successful, the Navy is expected to contract Stottler Henke to develop and deploy a customized, operational version of the system at naval shipyards, regional maintenance centers and ship facilities.
Navy ship maintenance is extremely labor- and resource-intensive, says Stottler Henke’s Director of Strategy, Rob Richards, and ship maintenance schedules must satisfy complex constraints. For example, many maintenance operations require different combinations of limited resources such as shops, equipment and teams with specific skills and certifications. Large parts are removed from the ship and transported to specialized maintenance shops where they are reconditioned or repaired. Other work is performed on board in small spaces, so spatial reasoning is needed to schedule those tasks.
Aurora uses advanced artificial intelligence, a Stottler Henke area of expertise, to increase throughput and increase productivity. It was originally developed to help NASA tackle difficult, mission-critical scheduling problems with complex constraints. Most systems use simple rules to select and schedule activities and assign resources to carry them out. Often, these schedules are far from optimal, says Richards.
“Aurora solves complex problems more effectively by encoding and applying sophisticated scheduling knowledge and decision-making rules provided by expert human schedulers,” he explains. “Aurora’s built-in and user-supplied decision rules produce better schedules by considering these attributes at key decision points such as determining which task to schedule next, assigning the best time and resources to each task to optimize the overall schedule, and handling situations in which some resources are not available when the task is scheduled.”
He says the best solution cannot be calculated by using mathematics alone because the problem is so large it can’t be completely searched by even the fastest computers in less than geological time spans. The system is suitable for non-military applications and has been used in a wide range of industries including airplane construction and satellite downlink scheduling. The shipping industry could be next.
The opinions expressed herein are the author's and not necessarily those of The Maritime Executive.