Innovation at Work
Digitalization comes to the weather deck
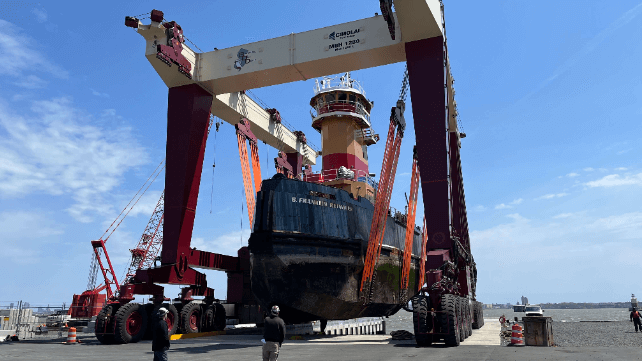
(Article originally published in Sept/Oct 2022 edition.)
Deck officers are intimately familiar with the gradual advance of digitalization on the bridge – with ECDIS replacing the paper chart and high-tech weather routing supplanting the trusty WeatherFax. That transition is also arriving on the weather deck where the machinery used for heavy lifting is now within reach for networking and electronic monitoring.
Classic freighters will carry on with basic hydraulic machinery for years to come, but newbuild and retrofit projects can now opt for "smart" deck systems that prevent misuse and monitor their own condition.
Digital Monitoring
Any modern main engine is fitted out with an extensive suite of sensors and digital controls that monitor and protect the multimillion-dollar investments in the engine room. The same can now be said for many cranes and expensive deck equipment. Digital systems provide protection, control and tracking, allowing owners to monitor their equipment's condition and plan for maintenance.
The engineers at Palfinger have applied digital monitoring systems to their well-known line of knuckle boom cranes, making them safer and easier to use. Palfinger is a leading name for cranes in the trucking and construction industries, and its land division has built digital control systems for operating and monitoring equipment in the field.
The company's marine division is taking a similar approach for its deck-mounted knuckle booms, which are common fixtures in the fishing, offshore and marine construction industries. By moving from hydraulic overload systems to digital, Palfinger aims to increase safety and reliability.
"Beginning with our newest knuckle boom,” says Gunther Fleck, Vice President of Sales & Service, “we have digital controls that work with sensors on the crane to better control its movements. The new controls also increase safety because they prevent the operator from making movements which could damage the crane. Crane operators are getting less and less skilled, and therefore you need additional safety features. These controls will be gradually introduced into all our marine cranes."
At the high end of high-tech lifting, Palfinger has taken digital control to its logical conclusion by designing an unmanned, remotely-operated deck crane for the offshore industry. This fully electric jib crane is designed for lifting cargo off the deck of an offshore supply vessel onto an unmanned oil and gas platform without any on-scene human intervention.
The special-purpose design is set to go to work on Aker BP's next developments on the Norwegian Continental Shelf, the NOA Fulla and King Lear fields. "We know that this is an entry point for us to develop this technology and roll it out to our other products," says Fleck.
Heavy-lift leader Liebherr also uses high-end digital technology on its cranes for unmanned offshore installations. Since crane inspections and maintenance on far-flung platforms are costly, offshore operators have an extra incentive to use digital condition monitoring and predictive maintenance systems to keep an eye on their lifting equipment.
Liebherr Intelligent Maintenance uses sensors on the crane to keep track of its condition and history, even logging the weather conditions to which the crane has been exposed. An optional automatic greasing feature keeps critical parts lubricated without requiring a technician to visit the platform. With these features in place, the crane can go 12 months or more without a maintenance call, saving labor and transport costs.
Deck equipment giant MacGregor has developed a similar digital condition-monitoring and predictive-maintenance system for its full crane portfolio, starting with high-end cranes for specialized offshore vessels.
Its newly-released OnWatch Scout monitoring system draws on multiple sensor points throughout the crane and relays the data back to shore where it is logged and processed by a predictive-analytics system. This "smart" system forecasts equipment degradation, giving operators advance warning so they can perform maintenance at the most convenient time. For the engineering crew on board, it provides alerts about the status of specific components along with recommended diagnostic steps and supporting technical documentation – on the same digital platform. The operator's shoreside staff can access the same information at the same time.
All next-generation MacGregor electric cranes are compatible with OnWatch Scout as well as most legacy cranes back to 2006. In the future, the system may even work with data from other OEMs' deck gear, says Bhavik Thakker, MacGregor’s Director of Digital Solutions.
“Walk-to-Work” Systems
Among the most sophisticated, highly-automated pieces of deck equipment on the water are “walk-to-work” systems, the stabilized gangways used to connect service operation vessels (SOVs) with offshore wind turbines and offshore oil and gas platforms.
These high-spec gangways are so large and mission-critical that the ship is designed around their structural requirements and their need for minimum vessel motion. The biggest walk-to-work units are so tall they come with their own elevator to carry technicians from the SOV's main deck up to the gangway level. In order to deliver technicians safely in a broad range of sea states, active heave compensation keeps the gangway steady while the vessel pitches and rolls in the swells.
Though it’s made offshore wind farm service possible in rougher conditions, walk-to-work is somewhat costly to scale. The wind market is expected to need dozens of SOVs to fill its needs over the coming decade, and at $50-60 million each, these special-purpose ships come at a price. The alternative is to retrofit a gangway onto an existing vessel, but this is not always practical because of the size and weight of a walk-to-work system.
Palfinger believes it’s found an affordable retrofit solution in the form of a specially-designed stabilized manlift, or "offshore passenger transfer system" (OPTS). The idea is to hoist technicians from the ship over to the platform using a stabilized boom and basket, eliminating the mass and complexity of a full gangway – along with 90 percent of the capex.
"Walk-to-work is quite difficult to retrofit on a vessel because of the design requirements for deck strength and stability,” says Fleck. “With the OPTS, it’s an easier calculation to install and you can put a working solution on many vessels. The operational speed is competitive, and it just takes about 60 seconds to transfer six people from the ship's main deck to the platform."
This could be particularly useful for the U.S. market where unused offshore supply vessels could be repurposed as Jones Act-compliant SOVs – if equipped with the right deck gear to transfer personnel. The lift also has dual-purpose applications for offshore oil and gas work: Fleck says the OPTS is an ideal way to access the underside of a platform for decommissioning or repair, which walk-to-work gangway systems cannot do.
Shipyard Lifts
Shipyards also have complex lifting needs, and Spanish crane builder Comansa has a solution from a related industry: heavy construction. Comansa makes and rents tower cranes for large construction projects, and Sales Manager Joseph Patton says these off-the-shelf lifting systems have great crossover applications along the waterfront.
U.S. shipyards typically invest in tracked, portable crawler cranes that can be driven around the yard, but these systems have a few drawbacks, he says. First, they’re relatively expensive with new models trading in the seven figures. Second, crawler cranes have a wide stance, and shipyards have to keep broad avenues clear to move them – taking up valuable space.
A tower crane is cheaper, has greater reach and only takes up a 25-by-25-foot pad on the ground. It’s also all-electric with no engine and no emissions.
Modern tower cranes can lift a lot more than their forebearers. Patton says a customized Comansa crane installed at the Aibel yard in Norway can handle up to 50 tons, and its 260-foot jib radius covers the entire work area. For portability, a tower crane can be installed on a portal base on quayside rails, but even one erected on terra firma can be disassembled and relocated in three to four days. "They're designed to be moved from one construction site to another," he adds.
Repair yards can also achieve higher productivity with a marine boatlift, which allows the shipyard to drydock as many small vessels as it has space to store. “Small” is relative because these wheeled hoists keep getting bigger year-on-year.
Italian engineering company Cimolai Technology holds the record for the world's largest boatlift, a 1,500-ton giant capable of lifting large yachts and working vessels. It sells versions in all sizes for marinas, boatyards and shipyards.
Bayonne Drydock & Repair, which fixes everything from workboats to sealift ships, commissioned a 1,280-ton Cimolai boatlift last year for use in docking tugs and other smaller vessels. It’s seen plenty of use in its first year in operation. "At the time of this writing,” says General Manager Bob Magas, “we’re proud to say we’ve completed 34 evolutions of hauling, completing repairs and undocking vessels using our mobile boat hoist. These projects range from a quick 'up and down' for propeller changeouts to full ABS/USCG five-year regulatory dockings."
Innovation at Work
Innovative lifting systems like these elevate the industry’s prospects, raising productivity and lowering costs. Enabled by digital technology, the biggest OEMs in the business are raising their sights, and the next generation of cranes may have even more capability – and less maintenance spend. – MarEx
Paul Benecki is the magazine’s News Editor.
The opinions expressed herein are the author's and not necessarily those of The Maritime Executive.