Circulatory Systems
Like the human body, a ship needs good circulation to run right.
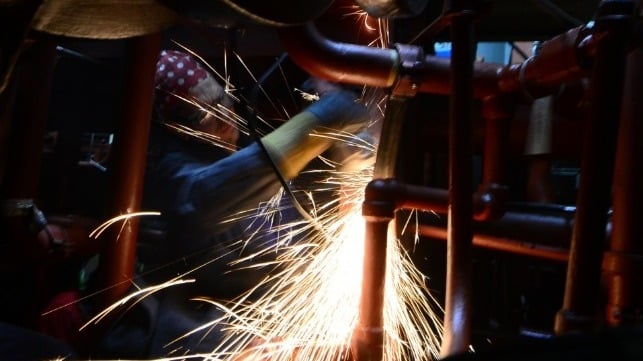
Despite all the technological advancements in today’s maritime sector, the same conventional methods continue to deliver the fluids that fuel, lubricate and cool the mechanisms of ships.
From alternative fuels to digitalization, as so many aspects of the industry seem to be evolving faster than companies can keep pace, it may seem that the piping systems that spider through the spaces and voids of every ship and maritime asset remain as rigid in their evolution as they are in their construction.
This is simply not true, of course, and briefly researching their history reminds us of the importance of these often-overlooked substructures. More importantly, speaking with leading-edge equipment manufacturers and vendors brings the truly dynamic nature of these industrial circulatory systems into vivid perspective.
Buckets, Bailing and Industrial Evolution
Piping systems and components have served as catalysts and facilitators for some of the greatest technological advances in history. Suction pumps designed to remove water from mineshafts helped the development of the steam engine as a reliable power source. Pressure pumps forced the evolution of stronger piping materials.
This relationship between necessity and invention likewise motivated many pivotal advancements in the maritime industry. No matter how well a wooden vessel was constructed and sealed, water found its way inside the hull. Sailors had to bail the water out bucket by bucket. As vessels grew with evolving shipbuilding techniques, more efficient dewatering methods were required.
Indeed, the evolution of shipbuilding created the need for better piping, pumps, and valves. In turn, the advancement of these components facilitated further improvements in ship design, building processes and materials.
That evolution continues today. Developments in materials and components spur advances in vessel design while digitalization allows users a greater degree of control and monitoring. These advances, in turn, reduce maintenance costs and support the industry in its current push to improve efficiency and reduce emissions.
Circulatory Anatomy
Similar to a living body with its complex circulatory infrastructures, a ship is comprised of many systems moving fluids to, from and through different equipment and systems. The same physical rules, requirements and components that regulate flow through the human cardiovascular system govern the circulation of fuel, cooling water and other media through a ship’s systems.
Likewise, the fluid networks supporting ships at sea sometimes experience comparable functional issues. Restrictions, wear and tear can negatively affect operational efficiency.
Unlike the human body, however, shipboard systems require far more external maintenance than their human counterparts, which have at least a limited ability to heal themselves. Any marine engineer will tell you in unvarnished vernacular the frustration involved in dealing with leaking pipes, corroded valves and worn, inefficient pumps.
Like unsanitary surgeons armed with hammers and acetylene torches, a quiet day in the ER (engine room) can easily become an emergency piping-related trauma response.
Components
Serving as the beating hearts of a ship, pumps ensure that her vital organs receive the essential fluids required to survive. The most dynamic elements of piping systems, pumps are subject to some of the most severe effects of corrosive fluids, cavitation and mechanical wear.
With the resultant high need for maintenance and upkeep, progressive manufacturers like Sims Pump Valve Company are employing composite materials in their construction, which offer tremendous advantages over traditional metals and alloys. Sims’ patented SIMSITE material demonstrates significant advantages in extending the service life of components.
Additionally, such composite materials used in shaft-stabilizing bushings, for example, can reduce operational wear on shafts, seals and bearings. Importantly, new equipment is not the only beneficiary. Replacement components are available for existing, even obsolete, installations via bespoke machining of parts from blocks of composite material like SIMSITE.
Connecting critical equipment to the pumps that service them are pipes, the veins and arteries of industrial vascular systems. Due to their traditional construction from ferrous materials, corrosion, wear and blockages often victimize piping networks. Even more insidious is the fact that, as the largest component of a distribution system – snaking quite literally everywhere personnel do not normally tread – pipes are the most difficult pieces to work with when in need of inevitable repair. Consequently, the best time to replace any pipe is often only when it fails (just ask any marine engineer).
W&O Supply, with a long history of providing valves and pipes to the marine industry, is looking at this issue through the eyes of an organization that has seen it all before. Since bringing groundbreaking thermoplastic piping to market in 2015, the company has witnessed the application of more plastics as the technology progresses. According to Kevin Hein, W&O’s Director of Engineered Solutions, these non-metallic options offer long-term advantages to commercial and military stakeholders given their service life of 25 years and the wide variety of sizes, media and operating conditions available.
One of the most interesting developments in this area, however, has little to do with the actual material utilized. Laser scanning technology makes design and installation vastly more efficient even before construction begins. Daryl Johnson, Owner of Summit Engineering and Design, says laser scanning takes the “measure twice, cut once” philosophy to the next level, delivering half-inch accuracy by “working in the actual, real three-dimensional space instead of drawings that may or may not match reality.”
If pumps are the beating hearts of a vessel’s circulatory system and piping is its vascular component, valves are… well, valves. Used for isolation, backflow prevention and other applications, valves offer regulatory and protective functions as vital as any component.
Subject to the same corrosive fluids and damaging vibration as pipes and pumps, valve construction material is important. This is especially true in light of the industry’s growing use of ammonia, hydrogen and LNG. Alternative fuels have different corrosive effects, flow at different temperatures and pressures and demonstrate other unique characteristics compared to traditional fuel oils.
“As new marine fuel technologies evolve,” says W&O’s Hein, “they will require specialized valve products.”
“Smart” Installations
Advanced materials reduce maintenance requirements and extend the service life of piping systems and their components. However, physical enhancements mean little if they don’t collectively improve performance of the larger system and ultimately the whole vessel. The catalyst that combines these elements into better execution is control.
Even though pumps and valves have historically been some of the last devices to which improvements are applied, today’s system newbuilds and upgrades are likely to be digitally integrated, “smart” installations. Variable frequency drives (VFD), for example, provide precise speed control for pumps, offering better tuning for performance and efficiency. Combined with precision control of valves and other components, emissions and overall safety likewise improve.
As the maritime industry’s vendors and service providers take advantage of remote capabilities, predictive maintenance, scheduling and management of critical spares further improve performance and lower operational expenditures.
Digitalization and the industrial internet of things (IIoT) also allow users a greater degree of monitoring. Remote access modules provide means of checking performance, reducing the number of service calls and providing better information to technicians when they do have to be present.
For all the promised advantages of technology, there are challenges, making the wisdom of experience critical. Some vessel owners may only see advanced piping networks as simple systems with “bells and whistles” added, the cost of which makes the siren call of cheap alternatives all that more appealing. John Kozel, President of Sims Pump Valve Company, warns that while cheap, inferior products still dominate sales, “It actually costs a lot more in maintenance, replacement and operating expenses.”
A Fluid Relationship
While hidden from view under deck plates, between bulkheads and inside tanks, piping systems nevertheless continue to drive and foster growth in the maritime industry – not only in their obvious role as stalwart circulatory systems but by reminding us of the fluid relationship between necessity and invention.
With the growing pressure to improve efficiency and reduce emissions, smart versions of pumps, piping and valves offer a reliable means of achieving increasingly rigorous objectives. The world’s militaries, operating in even more demanding circumstances than the commercial sector, are taking notice of innovations both inside and outside the maritime sector that offer pioneering solutions.
Alternative fuels, demands for greater efficiency and tightening markets are blending commercial and military specifications, driving significant changes in the definition of “marine grade” for piping systems and components.
Early advances in technology enabled better vessel designs, but the dynamic nature of piping systems and components extends beyond a solely historic role. As these components further drive the evolution of ships and the industry, progressive manufacturers and engineering companies are looking toward a future of increased efficiency in every respect. According to W&O’s Hein, “We have more technical resources at our disposal than ever before.”
This, however, does not preclude the need for intelligent application of these advanced materials and techniques. “The best approach is for each part of this process to be performed as part of an overall team where issues and feedback are brought to the entire team, leading to an efficient resolution,” says Johnson of Summit Engineering and Design.
As the industry and equipment evolve, there’s still no substitute for intelligent operators, management and service.
Kings Pointer, marine engineer and maritime consultant Chad Fuhrmann is a regular contributor to the magazine.
The opinions expressed herein are the author's and not necessarily those of The Maritime Executive.