Back to Life
Repair yards rebound in the wake of COVID
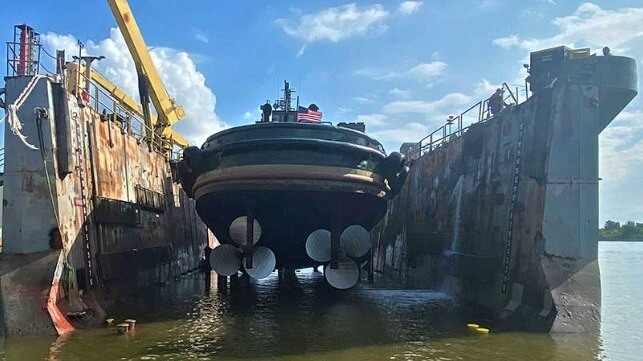
(Article originally published in May/June 2022 edition.)
Running a ship repair yard requires ingenuity, adaptability and a knack for bringing wornout equipment back to life. These talents work just as well on infrastructure as they do on ships, and many of the best yards expand by acquiring and fixing up underused assets.
With technical capabilities available in-house, a shipbuilder can repair a used drydock, gantry crane or workshop complex at a favorable price. Many of the fastest-growing yards on the market expand their footprint using the same creative skillset they use in repairing their clients’ ships.
At the Gulf Copper facility at the Port of Galveston, Texas, a novel ship repair project is expanding the capabilities of the shipyard itself. Gulf Copper holds the contract to drydock the venerable WWI-era battleship USS Texas, which needs significant hull repairs. The yearlong job will require a big floating drydock, and Gulf Copper and its partners have found a rare opportunity. Instead of buying or building new, the shipyard is purchasing and refurbishing a used drydock from a friendly competitor in the Bahamas.
In 2019, the No. 2 floating drydock at Grand Bahama Shipyard (GBS) suffered a casualty during a refit of a cruise ship, and the dock went out of commission. Thanks to a $350 million investment from its owners, GBS – the premier cruise ship repair yard for the Caribbean market – is set to get two brand new drydocks from China, each capable of handling the largest cruise ships in the world. The upgrade project may be the largest single investment in the history of Grand Bahama.
The landmark investment also means that GBS' damaged No. 2 dock will no longer be needed. It was the perfect opportunity for Gulf Copper, which purchased a segment of the dock for use in the USS Texas project. When repaired, the 35,000-ton dock will have plenty of capacity to accommodate the battleship's 570-foot-long bulk. Gulf Copper Vice President Jonathan Hale is leading the effort to ensure that the drydock is ready for delivery by the first week in June.
This isn't just any repair job. The battleship saw action in some of the most critical operations of WWII including the Normandy landings, the battle of Iwo Jima and the assault on Okinawa. She is receiving a degree of care commensurate with her service. The Battleship Texas Foundation is not just restoring the hull and superstructure – its conservators are stripping down and restoring the ship's equipment in minute detail. This is as labor-intensive as it sounds.
Taking apart, repairing and reassembling a single 20mm gun mount takes the conservators about 250 man-hours of labor, according to the foundation’s Vice President Travis Davis. The same painstaking level of care is being given to many of the battleship's fixtures, bringing new life to a 108-year-old ship.
Dockyard Upgrade
Detyens Shipyard in Charleston, South Carolina has grown its business significantly over its 60 years of history. Its home at the former Charleston Naval Shipyard site has three graving docks and one floating drydock, and Detyens keeps the giant complex busy with a mixture of government contracts and commercial work.
The acquisition of the former Charleston Naval Shipyard site in the mid-1990s provided the fuel for Detyens' growth. When the lease deal went through, the yard upgraded from wooden piers to government-grade concrete graving docks almost overnight. It also secured abundant workshop and warehouse space with enough room to house the yard and about 20 independent vendors and suppliers.
These include two coating companies, a sheet metal fabricator, three marine chemists, an electric motor repair shop and a 180,000-square-foot machine shop. On-site contractors speed up the work flow since there's no need to ship parts back and forth to a specialist shop. "The shipowner's port engineer can walk right over anytime to check on a motor rewind at Integrated Power Services, or head over to Collins Machine Works and take a look at the runouts on a propulsion shaft job," says Bradley Kerr, Director of Sales at Detyens.
The yard's success also springs from long-term employee relationships. Many have been at Detyens for decades, and Kerr says that the general pattern is that "If you stay for a year, you'll stay for ten." The high retention rate is helpful for repeat business because when a vessel comes through the yard for the second or third time, the team has seen it before and knows its layout.
Building on the skills of its experienced staff, Detyens is working hard to recruit the next generation of shipbuilders. Like most American employers, it’s finding that to be a lot more challenging in the pandemic era. "Everybody in Charleston's transportation industry – shipyards, tugboat operators, hauliers, freight forwarders, warehousing companies – everybody's looking for people now," says Kerr.
The shipyard's apprenticeship program and youth outreach efforts help spread the word. It also helps that Detyens' employees and their families have access to an onsite medical clinic staffed by two doctors and a nurse practitioner – a rare benefit usually found at much larger companies.
More Space, More Business
BLRT Repair Yards, a division of Baltic industrial conglomerate BLRT Grupp, has expanded its facilities in recent years to accommodate more and larger ships. The group operates Tallinn Shipyard in Estonia, Western Shiprepair in Lithuania and Turku Repair Yard in Finland, and its largest dock can handle vessels up to Post-Panamax size.
Recent capacity expansion and HSEQ investments are allowing the company to pursue new opportunities for bigger vessels. In addition, its parent company has acquired businesses that complement ship repair like the recent purchase of marine electrical systems company Bars Elekter.
These investments are paying off. In mid-March, Western Shiprepair in Klaipeda won a contract for repairs to a tanker owned by Bremen-based operator Sloman Neptun, the Sloman Herakles. It was a new customer for the group, and the docking was a pilot project. The customer was pleased with the results and has rewarded the yard with a contract for another vessel, the Sloman Dispatcher.
BLRT's core business rests on long-term relationships with companies like Wilson Ship Management, headquartered in Bergen, Norway. Gabriel Avanesov, Sales Director at Tallinn Shipyard, says the two companies’ partnership has been in place for 25 years. This long-term arrangement brings plenty of work to Tallinn, which has served more than 100 of Wilson’s ships over the years including three vessels since the start of 2022 alone. One of them, the general cargo ship Wilson Brake, has called at Tallinn Shipyard seven times since 2007 – a long run of repeat business.
Under New Management
On the other side of the Baltic, passenger-vessel specialist Fosen Yard has recently expanded with the addition of MV Werften's Volkswerft, a well-established shipyard in the city of Stralsund, Germany. Under previous ownership, the Volkswerft yard built the ultra-luxury expedition cruise ship Crystal Endeavor, and the facility configured for top-end finish work. It has an indoor production hall measuring 950 feet long - perfect for painting and fitting-out during Northern European winters - and a shiplift rated at 25,000 tons.
The city of Stralsund purchased the 85-acre Volkswerft property after cruise shipbuilder MV Werften entered insolvency proceedings earlier this year. The city council plans to attract a variety of users to revamp the site and create new employment, and Fosen Yard has negotiated a lease for the main hall and shiplift. The lift will be online for drydockings beginning in September.
“This will be an attractive alternative for luxury expedition cruise ships as these have extreme demands for a superb finish, which we can offer,” says Ole Morten Husøy, Business Development Director for Fosen Yard.
Fosen has a history of high-end refurbishments and passenger vessel conversions at its two existing yards. The new site in Stralsund gives it more flexibility, and the extra space is helpful as it negotiates for new projects – like two newbuild expedition cruise ships. “The Stralsund yard in many cases will be the yard of choice for larger conversions due to the shiplift, close proximity to many ro-pax ships operating in the Baltic Sea and the ability to roll vessels inside for high-quality groundwork and finish,” Husøy adds.
Regional Expansion
Fincantieri Marine Systems, the North American division of the well-known Italian naval and cruise shipbuilder, has opened a brand new repair yard in the North Florida market. The Fincantieri-built Freedom-Class Littoral Combat Ships are based out of Naval Station Mayport, and the company concluded there was a good business case for opening a local yard to meet the needs of the Navy, Coast Guard and commercial shipowners in the region.
Last year, Fincantieri Marine Systems agreed to lease the former North Florida Shipyards facility, a 30-acre site at Commodore Point in downtown Jacksonville. It’s investing millions in improvements including construction of a new 500-foot floating drydock certified to Navy standards. When the new dock is delivered next year, the yard will be ready to service Freedom-Class ships on Jacksonville's waterfront as well as other government and commercial vessels.
In the interim, the new Fincantieri Marine Repair yard is well-positioned to serve midsized commercial vessels up to 2,700 tons with its existing floating drydock and can accommodate larger ships at its pier for topside work as well. The yard's first project was to carry out testing and trials for another Fincantieri-built vessel, the LNG bunkering barge Clean Canaveral – the largest Jones Act barge of its kind.
The new shipyard brings employment opportunities for the Jacksonville region with 120 jobs already created and up to 300 more in the pipeline over the next three years. "We’re very excited to be a part of downtown Jacksonville and its economic growth,” says Megan Ehlers, the yard's Business Development Coordinator. “We have a strong commitment to excellence, and with our experienced team we’re ready to provide superior repair and maintenance services.” – MarEx
Paul Benecki is News Editor for The Maritime Executive.
The opinions expressed herein are the author's and not necessarily those of The Maritime Executive.