Confronting the Container Imbalance
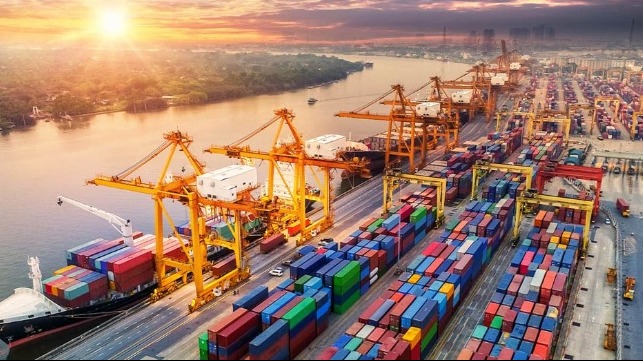
Procurement managers, technical directors, and purchasing agents are feeling it in high prices and long delays: As the global economy surges back to life, a massive imbalance in shipping container traffic is exacerbating bottlenecks in the supply chain.
Container bookings are hard to find. Delays are long, with many shippers waiting 6-8 weeks for a container. Prices are high: often 3-5 times normal rates, according to Alex Durante, global sales director at Horizon Air Freight. And air freight alternatives are even more expensive.
The container imbalance is impacting all sectors of the global economy. It contributes to inflation, which is on the rise, reducing consumer buying power in the midst of persistent shortages of key consumer goods. Small and medium enterprises are priced out of global trade by the high costs of shipping. Time-sensitive shipments of food are stuck in home ports. Even recovery from wildfires in the U.S. West is slower and more expensive because of the rising costs of building supplies.
What’s Causing the Container Imbalance?
In the early days of the COVID-19 pandemic, countries around the world went into lockdown. Many factories shut down, reducing supply. Simultaneously, demand for many consumer and business products plummeted.
With many ports closed and crewing complicated by public health restrictions, shipping companies took many container ships offline to wait out the crisis. This left empty back-haul containers stranded, with no ships available to collect and return them to net exporting countries such as China.
Over the past year, as the global economy has come back to life, recovery has been uneven. Many countries in Asia came out of lockdown first but found themselves with a shortage of head-haul containers for export, while continuing restrictions in Europe and the Americas stranded back-haul containers.
With restrictions now loosened, demand in the Americas has rebounded strongly in recent months, amplifying the historic trade imbalance between Asia and the Americas.
This has all prompted aggressive measures by Asian exporters to retrieve any available containers, placing other regions in competition for an insufficient supply.
Throughout the global shipping network, port congestion caused in part by staffing shortages and lockdown regulations continues to further delay any attempt to rebalance container supply.
How Are Container Imbalances Impacting Procurement Managers, Technical Directors, and Purchasing Agents?
“First and foremost, air freight rates right now are through the roof,” says Durante, “because there’s limited capacity. In some cases, air freight pricing is 2-4 times higher than what it was pre-COVID. That has led to a fundamental shift toward ocean freight, because ocean freight is much cheaper than air freight. So you have a huge shift of cargo that needs to be moved by sea now because it’s cost-prohibitive to move it by air.”
However, that cargo — including smaller ship spares — that might once have been moved quickly by air must now compete for an insufficient supply of shipping container space. Meanwhile, oversized equipment and bulk supplies that have always been too large or too costly to ship by air are taking longer to deliver by sea, at much higher prices.
Procurement managers, technical directors, and purchasing agents are having to make sometimes impossible choices. Wait 6-8 weeks to ship by container, at 3-5 times normal ocean rates or ship by air, at 10 times what the same shipment would cost by sea?
For critical equipment needed urgently to keep a ship in service, delays can be catastrophic, yet the solutions can quickly exceed a fleet’s budget.
What Is Horizon Doing to Help Customers Keep Their Fleets Running Smoothly Without Exceeding Their Budgets?
“We’re doing the same thing we always do,” says Durante, “but putting in a lot more overtime doing it. All of our attention is focused on finding solutions, because we know that every order is critical.”
Horizon has always managed emergency shipments for our clients, finding ways to move critical parts halfway around the world when every hour counts. We take pride in always finding a way, no matter how hard the ask. However, in the current crisis, even shipments that once would have been routine are requiring the full force of our agents’ experience, creativity, and persistence.
“Whereas in the past we might go to 2-3 steamship lines to find available capacity at a good price and schedule, now we’re going to 10 or more to find the best availability,” says Durante. “We have to move quickly, too, because pricing that was once stable is now changing every day.”
Throughout the crisis, our staff has often pulled rotating 12-hour shifts to find, confirm, and monitor appropriate bookings for every delivery, so that our customers get what they need, where they need it, to keep their fleets safe, able, and sailing.
What Can Procurement Managers and Purchasing Agents Do to Secure the Best Available Shipping Options for Their Fleet’s Equipment and Supplies?
In short, two things: plan ahead, and confirm quickly.
Planning ahead is good practice even in the best of times, but it’s really essential while the container imbalance persists. As much as you can, anticipate what your ships will need in two months, then go ahead and order it now rather than waiting until the last minute. The more lead team you give us, the better we’re able to find solutions that balance costs with your deadlines.
Whether you order with plenty of lead time or need a last-minute shipment because of an unexpected emergency, we’ll work hard to find available container capacity that meets your timeline and won’t bust your budget.
When we present you with a good option, please confirm it with us as quickly as you can. Because of the intense demand for container space right now, that available space may disappear hours later. If it’s still available the next day, the price may have gone up.
The sooner you confirm a price and schedule with us, the sooner we can go back to the steamship line and lock in that space for you.
When and How Will the Container Marketplace Rebalance?
The short answer: we don’t know. But, with current container shipping delays averaging between 45 and 60 days, we know this will continue for many months at the least.
“I think this is going to go on for at least another year,” says Durante. “The port congestion alone is not letting up anytime soon. That paired with the labor shortages that we’re experiencing, there’s not enough hands, there’s not enough equipment to conduct regular operations. Just think of a traffic jam where they’re not clearing the accident from the road.”
However long the crisis lasts, we’ll do whatever it takes to deliver to our customers, door to deck, on budget and on time. Despite all the challenges, ships will keep moving the world, and we’ll be by their side, ready and able to help.
The container imbalance is complicating shipping, but we love a challenge. Contact Horizon Air Freight and they will get you what you need, where you need it, on budget, with our industry leading 99% on-time delivery.
This message is sponsored by Horizon Air Freight.
The opinions expressed herein are the author's and not necessarily those of The Maritime Executive.