U.S. Navy Accelerates Uptake of 3-D Printing for Spare Parts
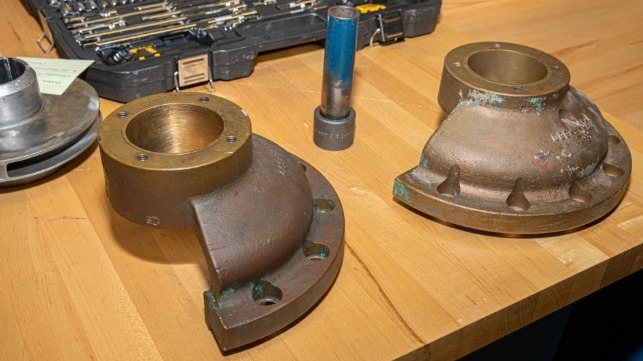
The U.S. Navy and Naval Sea Systems Command (NAVSEA) are exploring additive manufacturing (AM) technologies to design, print, approve, and install critical or obsolete parts – establishing a process and exercising component development on vessels even after undocking.
To jumpstart this effort, a NAVSEA team led by Engineering Duty Officers Lieutenant Commander David P. Johnsen and Lieutenant Commander Jake Lunday reached out to workers and Sailors across the globe and developed the Navy Additive Manufacturing Part Identification Exercise (NAMPIE) to identify what parts could be printed and installed shipboard or for use by waterfront workers. Efforts reached San Diego Naval Base in Ca.; Mid-Atlantic Regional Maintenance Center Norfolk, VA; Naval Station Rota in Spain; and Naval Station Mayport in Jacksonville, FL. Now, it has made it to the four public shipyards – with Norfolk Naval Shipyard (NNSY) leading the charge.
“This whole initiative started with a group of people who wanted to find ways to 3-D print parts onboard a ship – greatly reducing the amount of time it takes to make repairs while underway,” said NAVSEA's program lead for the project, Dalia McGlone. “While touring these other locations, the NAMPIE team started with identifying and producing smaller parts such as hooks and plugs with lower entry requirements, such as form and fit. And they had a lot of success with what they were doing, so we saw the value of the exercise for the shipyards.”
Together, McGlone and NNSY Innovation Program additive manufacturing lead Jessica Roberts went to Mid-Atlantic Regional Maintenance Center to see the initiative in action firsthand. It was clear to them this was something that could see a lot of success at the public shipyards.
“We’re looking to identify parts that support our capabilities of the Center of Excellence and identify future capability requirements - anything to benefit the Navy and the workforce of America’s Shipyard that work hard to maintain the fleet,” said Roberts. “We’re able to develop the technical data packages (TDP) for the parts to be routed, reviewed, and tested to establish it as a lasting component for the system.”
As of October, NAVSEA has a total of 182 approved 3-D printable parts in its database and more than 600 parts undergoing engineering review. With the exercise, they hope to expand these numbers significantly, continuing to build the database of parts accessible to anyone across the enterprise.
NNSY held its part identification exercise in late Oct., providing shops and code representatives an opportunity to share their ideas with the NAMPIE team. McGlone and Roberts were the leads running the event alongside Lieutenant Commander Lunday, who participated virtually due to the safety procedures in place with the ongoing pandemic.
One individual who met with the team was Non-Nuclear Surface Ships Propulsion Piping Division Mechanical Engineer Michael Nourse.
“During the NAMPIE, I was able to provide recent scenarios where we had to manufacture or procure a part in a short amount of time,” said Nourse. “I sent the team the part descriptions and drawings that we discussed so that they could have examples of what we worked on. I explained that for one part we had to machine bar stock in order to make a fitting to be installed on the ship. For another fitting, we had to order a new flange that came in after we needed it . . . This program could allow rapid development of ready-to-use parts. One of my main questions I asked the team was what materials could be used with these printers – depending on what’s available could greatly expand the capabilities of the shipyard and what could be developed.”
At this time, there are polymer printers throughout NNSY available for use. In addition, there are four metal printers en route to the shipyard that could be used to develop parts in stainless steel, tool steel, Inconel, aluminum and more.
With the exercise completed, Roberts and McGlone are already looking towards the future for not only NNSY but the enterprise as a whole.
“This is a shared initiative and we want to expand our reach as far as we can and get as many involved as possible,” said McGlone. “The goal is we can take parts from concept to creation, those that are obsolete, those with complex geometries and 3-D print them to speed up the process for getting parts installed or replaced. What’s more, we can even reverse engineer existing parts or develop parts that don’t exist yet but could help the mission.”
The desire is to have similar part identification exercise events at Puget Sound Naval Shipyard, Pearl Harbor Naval Shipyard, Portsmouth Naval Shipyard and the U.S. Naval Ship Repair Facility in Yokosuka.). NNSY and NAVSEA will continue to work with others to develop those ideas brought to the table.
“We want to encourage folks to come to us and share their ideas at any time; even if we don’t currently have the technology in place to make it happen right away, we want to know what the need is and look for ways on how we can help,” said Roberts. “Without the input from the workforce, we won’t truly know what the needs are. We want to build that connection and make innovation happen.”
The opinions expressed herein are the author's and not necessarily those of The Maritime Executive.