Carbon-Free Propulsion Using Articulated Tug and Barge Technology
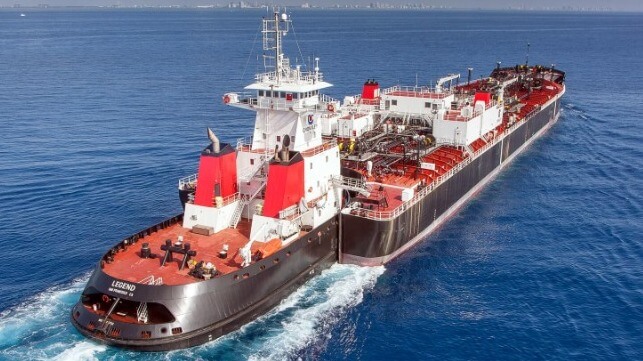
The maritime sector is introducing initiatives that reduce carbon exhaust emissions produced by vessel propulsion systems. Several carbon-free propulsion technologies involve the use of renewable energy and occupy considerable volumetric space inside a vessel, reducing payload capacity. Precedents in tug-barge operation suggests the possibility of combining a mega-size barge with a mega-size tug that provides propulsion and navigation.
Introduction
Tug-barge assemblies of vessels have successfully sailed in commercial freight service for many years along America’s inland waterways, the Upper Great Lakes and ocean coastal service. The size of each barge in a coupled tow on the Mississippi system suggests that a carbon-free tug could be built to 2-barge widths by 1.5-barge lengths. In service, it would sail within the hydraulic shadow of the coupled assembly ahead of it, thereby reducing its water drag. A tug of 3,500 to 4,000-horsepower is able to propel a barge tow of 4-barge widths by 10-barge lengths.
Railways moving the same tonnage and or volume as 40-barges would require groups of locomotives generating 30,000 to 40,000-horsepower to pull several trains. Converting main railway corridor operations to carbon-free propulsion requires the installation of electric power cables above the tracks at a cost of around $3-million per mile, along with purchase of all-electric locomotives. By comparison, there would be scope to develop an over-size tug that would carry competitively-priced, long-life grid-scale batteries at much lower initial and long-term cost. Unlike road or railway transportation, maritime transportation could actually use grid-scale batteries for propulsion.
Trailing Propulsion Unit (Tug)
Tug-barge propulsion has proven successful along inland waterways, across the Great Lakes and in ocean coastal service. Connecting the stern of an extended length of barge to the bow area of an extended length heavy tug requires a design of articulated coupling capable of sailing through severe ocean wave conditions. The coupling between barge stern and tug bow may need to allow for relative vertical freedom of movement while transmitting propulsive force and directional control as the barge and tug pitch at different frequencies. However, future research would need to determine the actual need for such a coupling.
The interior volume and carrying capacity of an extended-length and widened tug would be essential for a vessel that carries carbon-free propulsion technology. It could carry large tanks of hydrogen to operate either fuel cells or a thermal engine. Recent advances in liquid air energy storage could form the basis of tug propulsion. The tug could operate on heat-of-fusion stored thermal energy and recharge at coastal nuclear power stations. Grid-scale batteries capable of providing vessel propulsion includes aluminum-air technology, the iron-air battery, the zinc-air flow battery and vanadium-based flow battery.
Storage Technologies
A wide range of technologies have future potential to provide carbon-free propulsion for maritime vessels and might include:
- Liquefied Air: Initiatives are underway in England to develop grid-scale energy storage using super-cooled liquefied atmospheric air that has a density of over 80% that of liquid water. It has been successfully tested as propulsion in a small car and has potential to being adapted for ship propulsion where a geared turbine or positive-displacement rotary engine would drive a propeller. The combination of liquefied air stored inside well insulated containers and a source of stored thermal energy aboard a mega-size tug could theoretically propel a barge for distances of 600 to 1,000 n. m.
- Iron-Air Battery: The iron air battery occupies the space of a standard size shipping container (40-feet length). Small-scale testing indicated negligible deterioration of battery chemistry after 20,000-full depth drain cycles and is able to deliver steady output for a duration of up to 100-hours. An array of 2-levels of 8-wide by 4-lengthwise of iron-air battery containers (64) carried aboard super tug of 300-ft length by 70-ft width would deliver over 4,000-horsepower for 100-hours, making the technology suitable for tug-barge operation along inland waterways. Coastal operation and Great Lakes service would require larger versions of the tug.
- Stored Thermal Energy: Modern solar-thermal power stations continue to generate electric power after sunset, generating steam from thermal energy stored in mixtures of molten salt such as 80% lithium hydroxide and 20% lithium fluoride. There may be scope to modify coastal nuclear power stations to include a dock, where a tug may be moored to replenish its thermal energy supply. The tug would use a geared steam turbine or suitable positive-displacement rotary engine to provide propulsion while pushing and navigating barge trains along inland waterways or single barges in short-haul coastal service.
Given that steam is a greenhouse gas, a thermal tug or ship that operates its engine on steam would require a condenser to re-use and recirculate the steam. Sailing distances of 500-n. m. should be possible with thermal storage compound offering millions of repeated deep-drain discharge cycles.
- Aluminum-Air Battery: The aluminum-air battery stores double the energy of lithium-ion competitors. Its operation requires continual steady discharge, making it suitable for up to 30-hours of sailing at steady speed. Spent batteries would go to a recycling installation where the electrical storage compound can repeatedly be recycled and returned to energy storage application. A life expectancy of over 100,000 full-depth draining cycles makes the technology cost-competitive against lithium-ion technology. Long-distance sailing would likely require an exchange of battery-containers at prearranged locations, possibly using roll-on roll-off technology involving tiny wheels and standard gauge railway lines.
There would be a need to combine aluminum-air battery technology with a companion battery technology when sailing over extreme distances. While aluminum-air batteries would sustain propulsion for up to 95% of the voyage before depletion, the companion battery technology would sail the vessel out of the port of origin and into the destination port, with both ports able to recycle exhausted aluminum-air batteries.
- Zinc Flow Battery: Flow batteries carry electrical energy in a tank of liquid electrolyte, allowing depleted liquid electrolyte to be pumped out and recharged liquid electrolyte pumped in during a stop-over. The chemistry of the zinc-air flow battery from Zinc-8 of Canada carries zinc particles in a potassium-hydroxide (KOH) liquid electrolytic solution. Zinc-8 plans to offer over 100-hours of storage that involves less cost per kilowatt-hour than vanadium flow battery technology or lithium-ion technology. While Zinc-8 aims their technology at grid-scale storage market, their technology has potential for mobile application in vessel propulsion.
- Hydrogen: Reciprocating and turbine engines operate well on hydrogen. The electrolysis to produce hydrogen operates at 70% to 80% efficiency while fuel cells convert hydrogen to electric power at up to 70% efficiency, for an overall 50% to 55% round trip efficiency. Chemical batteries offer a round-trip efficiency of 70% to 90%. Thermal power stations operating at 50% efficiency while producing hydrogen incurs an overall round-trip efficiency of around 30%. Hydrogen is the leading competitive future carbon-free for commercial aircraft propulsion. Rapid re-fuel capability and extended operating range makes hydrogen attractive for carbon-free maritime propulsion.
- Mini-scale Nuclear Power: The past 20-years have witnessed several innovative new developments in small-scale and micro-scale nuclear power conversion. There would be scope to install mobile nuclear power conversion technology into a floating trailing unit, to generate electric power to propel and navigate a large forward unit. Upon arrival at a destination port, the nuclear tug would be uncoupled from the barge and then be coupled to the stern of a barge vessel being prepared for departure, with a replacement crew onboard.
Conclusions
Rechargeable/renewable energy technologies used in maritime propulsive service would occupy considerable volumetric space along with a considerable amount of weight. Tug-barge technology can combine carbon-free propulsion with maximum payload capacity aboard the barge. While tug-barge operation is well-proven in the wave conditions of the Upper Great Lakes and in ocean coastal service, further research might be needed to develop tug-barge articulated coupling technology capable of sailing through severe, storm-driven, mid-ocean wave conditions. Future battery tugs could measure over 400-feet length by 105-feet width, carrying grid-scale battery containers on several levels.
Several grid-scale energy storage technologies that show potential for use in maritime propulsion, offer greatly extended usable service life in terms of repeated full-depth drain cycles, at comparative initial and long-term costs. Maritime transportation requires far less engine horsepower per ton of maximum laden vehicle weight than railway or road freight transportation, allowing for cost-competitive grid-scale batteries to be adapted to mobile application sustaining electrical propulsion. Provided the power grid can supply the needed electric power for recharging, the long-term cost of vessel operation using grid-scale batteries would be cost-competitive against battery-electric rail vehicles and also road vehicles.
The opinions expressed herein are the author's and not necessarily those of The Maritime Executive.