Polar Tankers Trials 3D-Printed Parts on U.S.-Flagged Vessel
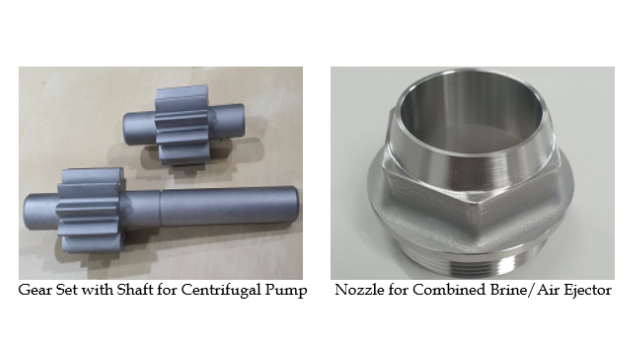
In partnership with ABS, Sembcorp and 3D Metalforge, shipowner ConocoPhillips Polar Tankers has installed working 3D-printed mechanical parts aboard the U.S.-flagged oil tanker Polar Endeavor.
Typically, the parts used in shipbuilding and repair are manufactured with casting or forging techniques. For this project, the consortium used additive manufacturing (AM, also known as 3D printing) to make three types of parts - a gear set with a shaft for a centrifugal pump; a nozzle for a brine/air ejector; and a full flexible coupling for an effluent pump. According to ABS, a rigorous testing process showed that the 3D-printed replacements are of higher quality than conventionally manufactured products.
AM techniques use a print head on a small robotic gantry to build up material layer by layer, following a digital CAD template to produce a part. With the a variety of sytems and technologies on the market, the range of available metal print materials is quite broad, including stainless steel, maraging steel, bronze, Inconel and (for aerospace users) titanium. The small footprint of a 3D printer means that products and components can be made locally (or even on board), cutting lead times. The additive method lends itself particularly well to short production runs and to the manufacturing of intricate parts.
“ABS is proud to be able to support this practical project . . . It’s a key development in a technology that certainly has a significant role to play in the future of the industry,” said Patrick Ryan, ABS SVP of global engineering and technology.
Other notable 3D printing ventures include a JV between Wilhelmsen’s Marine Products division and thyssenkrupp (formerly ThyssenKrupp) on serving commercial marine clients with AM-produced spare parts. Customers include Berge Bulk, Carnival Maritime, Thome Ship Management, OSM Maritime Group, Executive Ship Management and Wilhelmsen Ship Management.
“We are already seeing a very positive response from our maritime customers on the additive manufacturing adoption,” said Abhinav Singhal, Director of thyssenkrupp Innovations, in a statement last year. “They are realizing the benefits from faster lead times, reduced costs and having more resilience in their spare parts supply chain. This is going to be a true gamechanger for the maritime industry and we are proud to offer it alongside Wilhelmsen.”
The U.S. Navy's Naval Sea Systems Command (NAVSEA), Norfolk Naval Shipyard and Huntington Ingalls' Newport News Shipyard have also taken steps to roll out 3D-printed metal parts in the Navy supply chain, targeting critical or obsolete parts. As of October 2020, NAVSEA had approved a total of 182 3-D printable parts in its database and more than 600 more undergoing engineering review.