Cashew Nut Shell Liquid – Biofuel Savior or Concerning Contaminant?
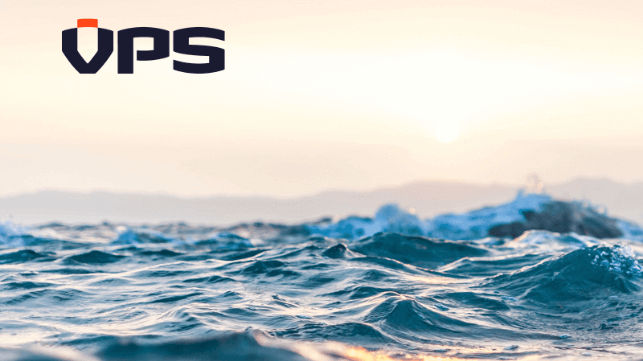
[By: VPS]
Cashew Nut Shell Liquid - Background
As demand grows from all modes of transportation for low-to-zero carbon fuels, to support efforts in complying and achieving numerous environmental legislation leading to global decarbonisation, many alternative fuel sources are being considered. One of the most common and in demand sources of such fuels, is Fatty Acid Methyl Esters (FAME), as either a 100% fuel-source, or as part of a bio-fossil blend. But with road transportation, aviation and shipping, all seeking to use FAME in their respective biofuels, demand is outweighing supply. Therefore, other bio-materials are being considered as alternatives to FAME.
One such material is Cashew Nut Shell Liquid (CNSL), which is the oil extracted from the shells of the cashew nut. This by-product of the cashew industry is a naturally occurring substituted phenol, which is abundantly available and a waste product, with a lower demand than FAME. The composition, properties and quality of CNSL depend upon the specific manufacturing production process used to extract the oil from the shell. These vary from, mechanical pressing to solvent extraction, vacuum pyrolysis, vacuum distillation or solvent extraction.
The industrial applications where CNSL is a key component are wide ranging and include, the production of polymers, plastics, resins, adhesives, surface coatings, insecticides, fungicides, anti-termite products and even pharmaceutical products.
There are three main components of CNSL, these are Cardanol, (also known as Ginkgol), Cardol and Anacardic Acid:
These substituted phenols tend to exhibit high acid number values (>3mgKOH/g). They also show high iodine values (>300gI2/100g), indicating an elevated level of unsaturation and hence increased degrees of reactivity and instability. Then also, high potassium levels leading to potential post-combustion deposits and corrosion of turbocharger nozzle rings.
As monomers, these chemicals are also prone to polymerisation at temperatures, >200ºC. As a consequence CNSL is potentially a highly reactive, very corrosive material.
However, the levels of acidity and reactivity can be reduced during the production and refining process by converting Cardol and Anacardic Acid to Cardanol. If the CNSL is >98% Cardanol, then the reactivity is significantly reduced.
VPS Testing of CNSL as a Biofuel
Over the past 3 years VPS have tested various CNSL compounds and fuel-blends to assess the potential of CNSL to be a viable biofuel.
Firstly, the use of CNSL blends can significantly reduce HC, CO/CO2 and smoke emissions, although they can raise NOx emissions slightly. However, VPS would advise never to use 100% CNSL as a fuel, as its far too reactive and corrosive. Further advice is to always check with the OEM regarding the compatibility of CNSL-based biodiesel blended products, with their machinery. Traditional marine fuels when blended with CNSL, may reduce the high acid number, reactivity and potassium levels of 100% CNSL, but also increase the energy content, sulphur content, cold-flow and sediment potential issues.
Fuel Combustion Analysis (FCA) of CNSL/Fossil Fuel Blends
In the recent past, VPS have tested CNSL products, blended with marine gas oil (MGO), very low sulphur fuel oils (VLSFO) and high sulphur fuel oils (HSFO). When undertaking fuel combustion analysis (FCA) of CNSL blended at varying percentages with MGO, VLSFO and HSFO, a wide range of results were produced in relation to, estimated cetane number, ignition delay and rate of heat release (ROHR), examples are given in the table below:
The CNSL blends with HSFO which undertook FCA, were particularly poor, with low Estimated Cetane Number (ECN), long Ignition Delay and low ROHR. CNSL blended with VLSFO gave better results, with acceptable ECN, shorter ignition delay and improved ROHR. Blending CNSL with MGO, gave better results than those obtained by HSFO/CNSL and VLSFO/CNSL blends.
Whether the blends were 80/20, 70/30 or 50/50 Fossil/CNSL, the blends using HSFO consistently gave the poorest FCA results. This may be due to a negative interaction between the asphaltenic content of the HSFO and the acidic nature of the CNSL.
Each of the CNSL blends gave poorer FCA results, when compared with the 100% fossil fuels, HSFO, VLSFO, MGO and 100% FAME.
Please note, to VPS knowledge, the above highlighted CNSL blends were not burnt onboard a vessel.
Burning CNSL/Fossil Blends
CNSL-blended fuels with MGO, VLSFO, or HSFO, have shown mixed reactions to vessel operations, where some CNSL-blends have been stored and burnt without issue, whilst, other CNSL-blends have given rise to operational problems such as:
- Fuel sludging
- Fuel injector failure
- Corrosion of engine parts
- Filter clogging
- Fuel system deposits
- Corrosion of turbocharger nozzle rings
- Damage to Selective Catalytic Reactor (SCR) units.
The quality of the CNSL, through its production and refining processes, will of course be significantly influential in relation to the quality of the fuel, but also the quality of the fossil fuel with which it is blended, will also have an influence.
A B100 Case Study
In early 2024, two vessels bunkered a B100 fuel in Flushing. The B100, was assumed to be 100% FAME, however, the first vessel began burning the fuel and experienced significant difficulties with blocked filters, delayed ignition and abnormal exhaust temperatures. Prior to burning the fuel, the second vessel sent samples to VPS for testing and via proprietary GCMS methodology. The fuel was found to consist of 40% FAME, 10% FAME Bottoms and 50% CNSL. So theoretically the fuel was a B100, it just wasn’t the 100% FAME, which had been ordered. This case highlights the need to know your fuel, its components and for biofuels, the need to know if the bio-source is truly sustainable? Having the fuel certified by an independent body such as ISCC, accompanied by independent testing from VPS, will provide the necessary confidence regarding the biofuel.
Potential Contaminating Properties of CNSL
In the final quarter of 2024, a VPS customer experienced numerous operational issues with its vessels when burning VLSFO fuels. These issues included blocked filters, delayed ignition and abnormal exhaust temperatures. On testing the fuel, GCMS analysis detected and identified the presence of 10,000-15,000ppm of CNSL within these fuels.
Up to the end of 2024, CNSL, which is a non-volatile chemical species, could only be detected using high-end, GCMS methodology. As CNSL is now more common within the fuel supply chain, it brings an elevated risk of potential contamination to fossil fuel supplies.
Therefore, VPS has developed a pre-burn, rapid screening technique, which detects and identifies the presence CNSL and other non-volatile organic chemicals. Whereas previously, only volatile organic chemicals could be detected by GCMS-Headspace Screening, this new and unique development of a qualitative GCMS-Headspace chemical screening method makes it possible, within a single analysis, to detect volatile (VOC), semi-volatile (SVOC) and non-volatile (NVOC) components within HSFO and VLSFO fuels.
Over the upcoming weeks, VPS will be releasing a technical white paper covering the development of this new GCMS-HS Advanced Screening Method, which is now available from every VPS laboratory.
CNSL Summary – Friend or Foe?
CNSL has certainly divided opinion of its applicability to be considered as a bio-component within marine biofuels. Its natural high level of acidity and reactivity, along with its potential to polymerise, certainly raises negative questions. Data would indicate using 100% CNSL as a fuel should be avoided, along with blending CNSL with HSFO fuels. Vessel operational issues, due to the presence of high levels of CNSL have caused fuel system, engine and exhaust damages.
For the purposes of ISO 8217:2024 and all preceding versions, CNSL is not recognised as a standard fuel component. Accordingly, its presence in a marine fuel may be considered a contaminant and potentially classified as off-specification when assessed against the ISO 8217 standard.
However, in instances where CNSL is intentionally used as a blending component and does not fully conform to any of the defined categories within ISO 8217, the fuel may still be deemed acceptable—provided that its characteristics and specification limits are mutually agreed upon by the buyer and seller. In such cases, the fuel shall be classified under an appropriate category defined in ISO 8217, accompanied by any necessary deviations or additional parameters required to adequately characterise the fuel's properties.
It is also worth noting that CNSL production and refining techniques are improving in order to produce a higher quality product. As stated, when the CNSL has a Cardanol content of >98%, with a significant reduction in the presence of Cardol and Anacardic Acid, then the product is a far less reactive component. Therefore, from a fuel purchasers perspective, it will be the choice of the CNSL supplier and the production processes they employ, which will be a significant factor in what is received and the CNSL properties, behaviour and overall quality of the product.
CNSL does require a much higher level of fuel management than other fossil fuel, or biofuel blends. So, whether it is in the development of a fit-for-purpose marine fuel blend, or in damage prevention detection of CNSL as a contaminant within fuels, VPS can provide high level, in-depth, expertise and experience in relation to CNSL-based fuels.
The products and services herein described in this press release are not endorsed by The Maritime Executive.