Rising Tide
AI can help solve most of our problems.
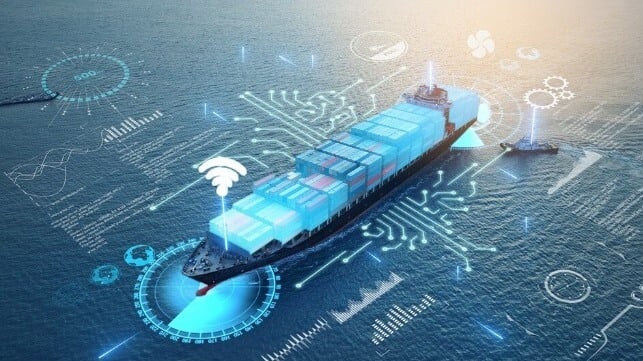
(Article originally published in July/Aug 2024 edition.)
[By Sean Hogue]
For all its innovation, there is still one area where the shipping industry clings to the past.
Paper.
Paper logs. Paper incident reports. Paper receipts.
This adds up to an estimated four billion pieces of paper in circulation onboard ships around the globe at this very moment.
Digital solutions rush to fill the gap, creating paperless platforms to better manage the maelstrom. Yet this does little to ease the ever-increasing reporting burden on the overworked officers of the watch, who more frequently find themselves driving a desk instead of a ship. And less than two percent of global trade is conducted digitally.
It’s a system largely unchanged since the 19th century.
Paper, Paper Everywhere and Not a Moment to Think
Part of the issue is that in global trade everyone does things, well, differently.
Depending on the charterer, contract, cargo, port or terminal, there are different requirements for timeliness and for the specific information requested. Some agents or port authorities respond quickly. Some do not. There are local forms, regional forms and flag state forms.
Charter parties. Bills of Lading. Statements of Fact. All unique as snowflakes.
When it comes to paper documentation, there’s a total lack of standardization.
Many Hands, Many Errors
Then there is the processing time.
A McKinsey study found that a standard Bill of Lading – a paper-based document required for the transport of goods – takes 16.4 hours of processing for every single shipment. Most of this is performed manually: by Masters at their desks, agents running between ships, banks, buyers, and insurers. And most of the documents have a total lack of standardization.
But if you can’t standardize the paperwork generated by the approximately 60,000 cargo ships sailing around the world, what if you used AI to standardize and digitize their output instead?
That’s the mission that Burmester & Vogel has been working on since new management took over the business in 2019.
Solving the Demurrage Problem
Founded in Hamburg in 1983, Boston-based BV is best known for laytime and demurrage management in the dry bulk and oil & gas industries. In 2022, the company began developing Artificial Intelligence and Machine Learning models to automate laytime and launched its AI-powered demurrage platform in 2024.
Demurrage is a penalty or freight cost charged to the charterer if their cargo operation exceeds the agreed amount of time to load or discharge cargo – also known as “lay time.” This compensates the ship owner for the delay and potential loss of earnings.
Evidence of delays, interruptions or exceptions to laytime is provided in a Statement of Facts (“SOF”), a notoriously non-standardized document often handwritten in chicken scratch. For tankers, there are often three for every operation: one from the ship, one from the shore and even one from the terminal or the surveyor. Comparing them is incredibly time-intensive. Differences often lead to lengthy disputes between the charterer and shipowner on the amount of demurrage owed.
So why not let AI do the work?
When you upload SOFs into B&V’s Demurrage AI Copilot platform, within seconds the system:
- Processes, digitizes and standardizes the documents,
- Compares each SOF against a demurrage claim or the charter party, and
- Delivers a side-by-side comparison, enabling fast analysis and accuracy in the settlement of disputes.
Thanks to the company’s long history in this space, B&V’s customers have shared thousands of documents to train its machine-learning algorithms, transforming non-standardized paperwork into automated laytime and freeing up human capital to spot-check the results.
Solving the demurrage problem not only impacts those involved in global trade but will lower time in port, reduce emissions and ultimately increase overall efficiency.
Simplifying RFPs
What did the last Request for Proposal (RFP) that came across your desk look like?
Likely the scope was unclear, the technical specifications immense, and the standards that the request needed to comply with (ABS, Lloyds, etc.) would take days to decipher.
This becomes an issue for both sides of the deal. The issuer doesn’t have time to write a clear RFP, and the vendors don’t have time to respond in full – or respond at all. This results in bids that cannot be easily compared, time delays, and just a boatload of extra paperwork in general.
Attender.ai, led by CEO Kevin Humphries, has developed a system to tackle this head-on and a marketplace that puts approved vendors and procurement teams next to each other to provide streamlined service acquisition.
The platform starts by using its AI engines to dig out the exact technical specifications, regulatory requirements and industry standards, then packages them up in an easily accessible scope of work. This gives vendors a clear understanding of the requirements and provides a firm baseline from which to begin the proposal process.
It then takes the next logical step and places prequalified vendors next to the issuer through its marketplace. Now they can easily bid on well-defined scopes through the platform, and the issuer can receive qualified bids that can easily be compared due to the standardization the platform provides. Plus, advanced analytics can advise on regional pricing trends, historical vendor performance and more.
Ultimately, this reduces overhead costs, is simple to use and provides a market for end-to-end service.
Everyone wins.
Managing Risk
It’s apparent that AI can reduce the paperwork burden at sea.
The next question then is: Can it help reduce high-impact shipping incidents?
That’s the question HiLo Maritime Risk Management has begun to answer. And the results are staggering.
Started as a project between a handful of shipping companies and a division of Lloyds Register, HiLo became an independent company in 2018 after the technology was proven. It now boasts more than 50 companies as customers.
The concept is simple: Take all of the incident reports, safety observations and related HSE data and plug it into the system. The core module, known as Pinpoint, maps the data, considers causal links, summarizes the data (kind of like what Amazon reviews is doing these days) and generates themes around leading indicators upon which the vessel operator can focus to improve safety.
In other words, it creates a network of cause-and-effect that is statistically significant and actionable. It draws a link between high-impact events and their drivers and has been demonstrated to be 98% accurate.
The catch is that the data provided by a single ship is not enough to draw these conclusions. It requires hundreds of thousands of data points from across thousands of vessels to pick out the weak signals. It only works if enough people share freely (and anonymously!), and the amazing thing is that HiLo has been able to create a culture that does just that – with over 50 companies freely sharing all of their incident data, totally unsanitized.
Again, using AI and statistical analysis to manage the mountains of paperwork previously processed by weary human hands and to summarize the resulting data into actionable insights is providing leverage on a scale we’re just beginning to grasp.
The Future Is Data
Your company already has the data.
Tucked away in logbooks. Filed in cabinets. Or hidden in folders inside dumb digital documents.
Processing that data into something manageable and summarizing it into something we can use is incredibly human capital-intensive. Which is why it doesn’t get done very well.
Who has the time?
And this is the advantage AI gives us. It isn’t going to “take our jobs.” It’s going to free up the massive resource that is our human capital for more important things than shuffling paper. Things like creative problem-solving, strategic planning, relationship-building, ethical and moral reasoning, and creative work.
The AI tide is rising, and it’s raising the performance of all companies, ships and maritime personnel that choose to embrace it.
Master mariner Sean Hogue is Senior Vice President of Operations at Baker Marine Solutions.
The opinions expressed herein are the author's and not necessarily those of The Maritime Executive.