Predictive Maintenance
Early detection of potential problems is the key to smooth sailing, especially in these COVID-constrained times.
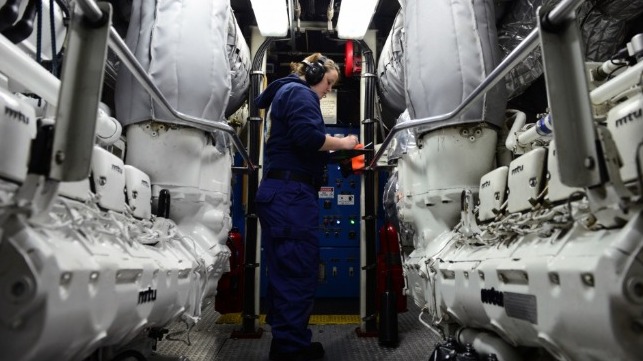
(Article originally published in Sept/Oct 2020 edition.)
In the midst of a global pandemic, face-to-face meetings have shifted significantly toward virtual delivery, such as telemedicine, which allows patients to connect virtually with their doctors, mitigating the need for in-person appointments.
The same can be said about condition monitoring (CM) and machinery, where rotating machinery is the patient and the analyst is the doctor. CM is the process of monitoring the health and functionality of critical assets, allowing ship operators to make efficient and effective maintenance decisions.
Informed decisions lead to increased equipment reliability as possible failures are detected in their infancy and can be tracked during their progression. This approach increases safety and decreases the risk of critical equipment failure while out at sea, thereby drastically lowering maintenance costs associated with the monitored machinery.
The Two-Percent Solution
According to Lloyd's Register’s Technical Investigation Department, only two percent of classed vessels have a condition-monitoring program. Vessel operators have been hesitant to adopt a CM program due mainly to preconceived notions of cost and complexity.
Although this technology has been available for decades, its slow adoption results in a lack of available information. As a result, many ship operators turn to the more familiar, time-based approach known as preventive maintenance. However, even if the most dedicated of engineers kept up with the recommended preventive maintenance tasks and routine inspections, only 23 percent of failures would be prevented. According to the U.S. Navy 1982 MSP study, 77 percent of failures occur randomly.
Contrary to popular belief, machines do not just fail. Typically, there is a failure mode present that amplifies over time. These machinery failure modes can be detected with condition-monitoring technology and, similar to human health, the key to preventing machinery failures is early detection.
Commercial vessels that adopt a CM program will increase their productivity, operational reliability and safety, while saving time and money.
How It Works
Under perfect conditions, rotating machines are designed for infinite life. Unfortunately, there is no such thing as perfect conditions in practical application, thus we strive to produce the most optimized operational conditions possible.
Condition monitoring does not enhance a machine's capabilities, nor does it prolong failure. It does, however, provide crucial information about the component being monitored such as overall condition, symptoms of failure and their severity.
If a condition-monitoring program has been established, it may be using either a stationary online system that collects data continuously or a portable hand-held monitoring device to take periodic measurements.
A stationary online condition-monitoring system utilizes permanently mounted accelerometers affixed to the desired machinery (usually located at each bearing within the propulsion system). Cables connect the accelerometers to the online system. Upon installation, the online condition-monitoring system is configured with a database containing the machinery to be measured, tasks and alarm levels. These tasks are specifically chosen to show machinery status, identify failure modes and automate diagnostics.
Temperature, pressure, and vibration data are collected across all channels simultaneously (good for picking up any transient events and diagnostic comparisons) and transferred to the integrated ship management system via ethernet or to onshore servers via mobile cellular router. These systems detect machine failures such as misalignment, excessive gear mesh, unbalance, groundings, bent shafts, propeller issues and bearing failures. The online condition-monitoring system can also be configured to send email notifications of machinery status updates to phones or computers.
With a portable offline device, ship operators can monitor the machinery's condition whenever desired by collecting the data themselves. Advances in handheld data collectors have made them very cost-effective and user-friendly, enabling crew of any technical ability to collect informative machinery data themselves.
The data can be analyzed two ways: It can be studied on-site using automated email notifications and visualization software, or remotely by a qualified engineering firm. The objective behind sending real-time data to shore installations is to allow advanced computational models to process the data and provide a baseline, trending analysis and timely diagnosis to the ship regarding operational measures and corrective actions required to avoid failures.
Benefits
Often practiced, the "run to fail" method is always more costly. Failure of one piece of equipment will affect the surrounding equipment, which will contribute to failures of nearby equipment.
A main benefit of using the proactive maintenance approach is that it allows machinery operators to predict future failures and address the root causes of a breakdown. With frequent and reliable machinery updates, ship operators have a real-time list and a clear picture of maintenance tasks to help shift from reactive to proactive maintenance.
Condition monitoring not only eliminates hidden costs, it can also boost overall machinery availability. With CM, ship operators can increase machinery uptime leading to lower operating and maintenance costs while reducing unplanned breakdowns, increasing fuel efficiency and maximizing productivity.
And as previously noted, condition monitoring can help ship operators transport data back to shore, eliminating the need for an analyst to travel to and attend the vessel, thereby saving time and travel costs. During the pandemic, the industry has seen stricter guidelines for onboard contractors, meaning remote condition monitoring is the safest way to keep track of maintenance needs.
According to Lloyd's Register’s Technical Investigation Department, only 17 percent of classed ships operate with an approved preventive maintenance system. Only 12 percent of the vessels enrolled in the preventive maintenance program use condition monitoring. Often, to stay enrolled in the class-approved program, surveyors may request vessel operators to disassemble a machine or locate archived maintenance records.
The required time to look for maintenance files not digitally archived can be significant. Additionally, disassembling a machine could compromise its internal components and overall functionality. Condition monitoring provides surveyors the same information as an “Open and Inspect” non-destructively. Digital data files can be pulled from data collections with the push of a button.
Classed vessels enrolled in a predictive maintenance program that did not have a condition-monitoring program during the pandemic lost crucial data needed to remain enrolled. Several ships will be forced to reapply the following year.
Nascent Stage
Predictive maintenance within the shipping industry is still in its nascent stage. With only two percent of all registered vessels implementing a condition-monitoring program, introducing a predictive maintenance approach is largely unexplored and therefore holds the highest potential financial impact on the bottom line.
Rich Merhige is Founder & President of Fort Lauderdale-based Advanced Mechanical Enterprises (AME). He was the subject of an “Executive Achievement” feature in the May/June 2014 edition of the magazine.
The opinions expressed herein are the author's and not necessarily those of The Maritime Executive.