Making the Case for Condition Monitoring
A well-planned condition-monitoring program can save both money and lives.
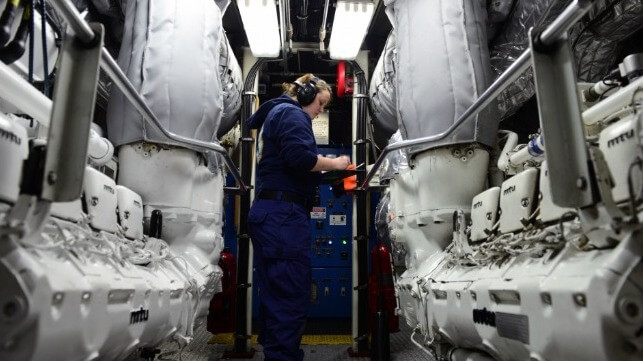
(Article originally published in Sept/Oct 2021 edition.)
It’s well-known that reliable condition monitoring had a difficult childhood. In many respects, the practice developed on its own over the years, much like a child who matures without parents or without a specific set of tried and tested guidelines for what to do and how to do it. But those of us in the field know better, and difficult childhoods often make the most interesting adults.
When equipment breaks down, it’s costly to get it running again. For that reason alone, maintenance should never be thought of as merely a drain on resources. Maintenance costs can be offset and, given accounting changes and a different management approach, even show a profit. Senior company executives and their accountants have too little appreciation for the opportunities to make maintenance a profitable operation rather than a loss leader.
Managing Costs
Analysis of maintenance costs clearly shows that a repair after a failure will be three to four times more expensive than the same maintenance activity when it is well planned. But maintenance is not usually considered a top priority with most shipping companies, who don’t fully appreciate the cost of downtime or the financial impact of unusable machinery on their vessels.
Unfortunately (and incorrectly), maintenance has too often been viewed simply as a direct cost burden of labor, material and overhead — fixing machines when they break down instead of carrying out “expensive” routine preventive maintenance. However, the real expense is in fact incurred when equipment does break down because more modest scheduled maintenance expenses were spurned as a matter of company practice.
I was assigned to a vessel a number of years ago that changed operating companies. The previous company had a firm policy that, every four years, each pump and motor on the ship would be removed, taken to the workshop and overhauled. The result was zero breakdowns. With the new operating company, this policy was seen as an unnecessary expense and abandoned. It worked for a while, but soon the breakdowns started happening and repair costs skyrocketed.
Of course, senior management tried to blame the chief engineers for the increase in breakdowns, but to quote John Adams, “Facts are stubborn things; whatever may be our wishes, or the dictates of our passion, they cannot alter the state of facts and evidence.”
Managing shipboard preventive maintenance systems in the 21st century is a daunting task, but one that really deserves much more attention. Increasing global competition, rapid advances in technology, safety and environmental considerations, and changes in management structure not only offer considerable opportunities to improve performance but also a much-needed competitive edge Condition monitoring for fault predictability, identification, isolation and repair is the heart and soul of every reliable preventive maintenance system, or at least it should be.
Multidisciplinary Approach
Effective maintenance management requires a holistic, multidisciplinary approach to systems thinking encompassing economics, instrumentation engineering, scientific discipline and information technology to detect and predict failures. The potential benefits of such an integrated multidisciplinary approach are wide-ranging. It’s been clearly demonstrated that the use of effective conditioning monitoring and maintenance techniques can give companies significant improvements in efficiency and directly enhance profitability.
They also have a major impact on the operational efficiency of each and every vessel. That impact increases as the systems become more sophisticated and their elements more dependent upon one another. It requires an interdisciplinary approach, dependent upon condition monitoring of all relevant parameters – prediction, prevention and control.
It’s an unfortunate truism that we rarely change our ways or take action until disaster strikes and losses mount. This “sacrificial lamb” approach will be regretted both in the short- and long-term with respect to machinery failure and the costs associated with injuries to personnel and potential litigation.
The trend of higher rotating machinery speeds and more power has resulted in the design of machines that are increasingly susceptible to vibratory phenomena. High-speed machines impose a limit on the operator’s capabilities. Lack of appropriate education and training to deal with this unfamiliar environment may lead to unpredictable systems failure, expensive shutdowns and the numerous safety issues related to those failures.
The Role of Information Technology
Nothing is more important to the successful management of a business than information. Whether we are trying to improve performance, reliability, profitability or the time it takes to go from point A to point B, the results can only be as good as our information. Information is to business what air and water are to us.
That’s why information technology has taken such a central role in making businesses more competitive. But studies have shown that many businesses are not successful in taking full advantage of the latest, potentially beneficial technology.
The impact of information technology on condition monitoring and maintenance management is significant. Over the years condition monitoring changed from being an instrument-based technology focused on making measurements into a results-oriented strategy with the intelligent information that it gives to designers and operators becoming the dominant focus. This paradigm shift directed the emphasis away from the instruments and onto personal computers (PCs).
At the same time the PC underwent a radical change. At one end of the spectrum, large numbers of PCs were grouped together into networks to replace the mainframe computer. At the other end of the spectrum, the PC has shrunk in size, making it more portable. Also, the boundaries between the instrument and the PC have been eroded as the PC has been replaced by Data Collection Units (DCUs) in the field to collect real-time data that is then downloaded onto the network PCs for analysis ashore.
The impact of these changes has offered new possibilities for condition monitoring. Networks now can upload raw data to the cloud, and this latest iteration allows the data to be shared throughout the company, enabling condition monitoring to become part of a complete management strategy for the entire company, not just for a vessel's chief engineer.
The costly need for Subject Matter Experts (SMEs) to be available on the spot is also being eroded. In addition, many disciplines in the field of condition monitoring and diagnosis that existed independently of one another in the past have been integrated with all of the intelligence available for decision-makers when and where they need it and at an attractive price point.
All of this necessitates the need for an effective approach to condition monitoring and condition-based maintenance (CBM) to prevent the costly expense of machinery failure and injury to personnel.
Paying Dividends
CBM on its own or combined with scheduled maintenance has proven to minimize the cost of maintenance, improve operational safety and reduce the quantity and severity of in-service machinery failure. An additional benefit is that it provides historical data, including the reliability characteristics of a system based upon the hours between maintenance tasks.
Monitoring the condition predictor of maintenance-significant items has the advantage of extending the realizable operating life and therefore increasing the system’s availability by reducing or eliminating equipment failures.
Simply stated, condition-based monitoring of equipment pays dividends well beyond any reasonable factor in standard cost/benefit analyses.
Robert Rice is Secretary-Treasurer of the American Maritime Officers union and Chief Engineer, Unlimited-Motor, Steam, Gas Turbine. This is his first appearance in the magazine.
The opinions expressed herein are the author's and not necessarily those of The Maritime Executive.