New Lubricants Will Be Key to the Renewable-Fuel Transition
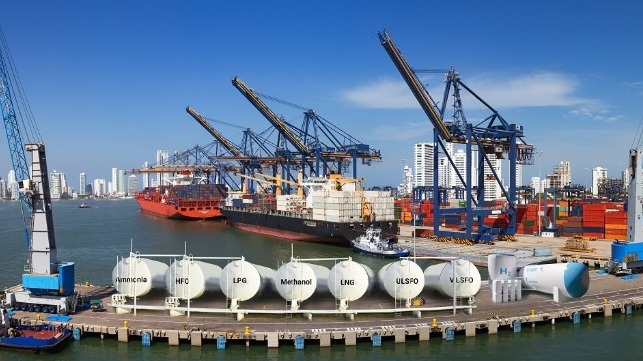
Ship operators must work alongside the companies they charge with maintaining engine condition in order to ensure a smooth transition to using alternative fuels. That is the challenge laid down by Lubrizol’s Technical Manager for Marine Engine Oils, Ian Bown, as the company explores how it must adapt lubricants to protect ship engines burning alternative fuels.
Shipping’s long-term environmental targets are propelling the industry’s quest for new, cleaner fuels. But while the big target – cutting greenhouse gas emissions by at least 50 percent compared with 2008 levels – is still 29 years away, time is short for the task at hand. Engine technologies for many of the candidate fuels have yet to reach even the pilot stage in commercial shipping, but the lifespan of vessels means that fuel choices will need to be made very soon for newbuilds that will likely still be trading by 2050. The long development cycle for cylinder oils is another challenge.
“It is well recognized within the industry that while changes come quite quickly in some areas, lubricant development is sometimes not as fast,” says Bown. “That's because we have to understand the impact of these fuels when they're in service.”
When it comes to preparing the lubricant additives that will help ensure cylinder condition on main engines, laboratory tests are simply not enough. Collecting experience from engines operating in the field is a crucial part of the lubricant and additive development process. The release earlier this year of CIMAC guidance on lubricating LNG-fueled engines – more than five years after the first such marine engines were put into use – shows the typical lag between market introduction and the settling of lubrication requirements.
A lack of willing test cases can exacerbate the delay. Many shipowners and operators are understandably reluctant to put forward vessels as guinea pigs for new lubricant technologies. But with the industry now under pressure to develop viable solutions for using alternative fuels, Bown hopes that this may change.
“I’d like to throw down a challenge to shipowners to engage with us on developing new oils,” he says. “There’s a lot of discussion about collaboration and I believe it will be essential for shipowners, engine designers, fuel suppliers and lubricant companies to work together to understand the engine performance, condition and the implications of new fuels.”
It is not just the service experience that takes time to gather. Lubrizol’s experience in the run-up to 2020 – and the global 0.5 percent cap on fuel sulfur, the biggest ever coordinated change in marine bunker quality – highlights some of the other challenges that await shipping as it prepares to operate with new fuel types.
The first issue is fuel availability. When Lubrizol started its research into very low sulphur fuel oil (VLSFO) in 2017, there was virtually no VLSFO available in the market. Even up until late 2019 it was unclear what the blends were going to look like.
“We started by blending our own 0.5 percent sulfur fuel to test in the lab, which is probably a lot easier than manufacturing ammonia or methanol,” says Bown. “And we continued down that path until we managed to obtain our first small quantities of commercially available fuels for bench testing and then sufficient quantities to run engine tests.”
At the engine test stage, a second challenge was observed. The field tests on VLSFO did not always match the findings of the smaller scale, laboratory-based bench testing conducted earlier in the development cycle.
“Those engine tests helped us to understand earlier results from the bench tests we use to determine deposit formation and antioxidant effect. This gave us direction for our formulating approach. Some of the bench tests were giving us results that did not correlate with what we saw in the test engine. We had to go back and take another look. In some cases, we modified the bench tests and in other cases we had to introduce new tests that would give us a better indication of performance,” he said.
The upshot is that developing products for new fuel types takes an enormous investment not just in time spent on in-service testing, but in ensuring that laboratory tests are measuring the right characteristics. Based on Lubrizol’s experience preparing for VLSFO, Bown believes that similar challenges will emerge as the company investigates alternative fuels.
“In the early stages, the development processes are going to be more iterative. It will take us time to understand the interactions between the lubricant and the fuel and how existing bench tests correlate to real world conditions. We may need to adapt current bench tests or design new ones to strengthen this correlation.”
Over the past year or so, Lubrizol has been laying the groundwork for investigating the lubricant performance requirements of the main alternative fuel candidates. To guide its research, the company has developed a matrix for assessing the challenges associated with each fuel. This includes looking at the inherent fuel characteristics, the engine modifications the fuel will require, the operational impact on the engine and, based on all of those things, the performance required from the lubricant.
Taking methanol – one of the emerging favorites among clean fuels – shows how the matrix helps Lubrizol to study fuels systematically. Like many alternative fuels, methanol requires a small amount of pilot fuel for controlled combustion. This will have an impact both on emissions and on engine condition. Also, like other fuels, there is a chance of auto-ignition. Auto-ignition results in combustion that is not as efficient as well-timed combustion, leading to greater fuel consumption and higher emissions. It can also create hot spots within the cylinders and on pistons that can lead to damaging deposits.
These inherent characteristics mean that engine developers need to adjust their designs to use methanol as a fuel. To manage the different injection pressures of methanol and the pilot fuel, new injector concepts are needed. Also, to keep emissions of NOx below IMO’s Tier III limits, exhaust aftertreatments are required, such as selective catalytic reduction (SCR), exhaust gas recirculation (EGR) or water injection.
Based on those characteristics and engine design changes, there are operational impacts on the engine. It is this column of the matrix where the need for engine experience as well as lab testing becomes clear. One example of an impact when using methanol is the different flame propagation compared to conventional fuel. While the flame created in the cylinder by diesel combustion is quite consistent, the flame from methanol combustion is not. It can last longer and is not as even as the diesel reaction. This unpredictable flame can lead to parts of the cylinder piston being exposed to higher temperatures, again increasing the potential for deposits that can cause engine wear.
From looking at these three areas, it is clear that methanol has some specific requirements from a cylinder lubricant. The risk of auto-ignition and flame propagation will mean that a lubricant needs to be robust enough to withstand relatively high cylinder temperatures without diminishing its ability to provide effective lubrication. The risk of deposits being formed at hot spots will mean greater wear protection is needed to prevent premature cylinder damage. Further challenges are likely to emerge as engine experience grows.
“Across all the main alternative fuel candidates, the matrix gives a good initial idea of where Lubrizol’s development challenges lie. Based on this early investigation, an important fact is already becoming clear,” says Bown. “We will certainly need new additive chemistry to enable these fuels, and I think it is safe to say that there will be no one-size-fits-all solution. It will certainly be about choosing the right oil for the right application.”
Time is of the essence if the industry is to meet the challenge of using alternative fuels without dramatic changes to the way engine and cylinder condition is managed. While lubrication formulation throws up its own unique challenges – particularly the long lead time for product development based on service experience – there are other areas in which all industry stakeholders face the same concerns. Bown highlights risk assessments as one key area.
“Before you can bring in even the smallest amount of these fuels for laboratory testing you need to conduct a very rigorous assessment of potential risks. What do we need to do as we run this through our tests? What do we need to be aware of? What's different between a lubricant contaminated with ammonia, for example, compared to a lubricant contaminated with a residual fuel? These tests are onerous and every stakeholder in the industry is going to have to go through them.”
Once again, partnerships could accelerate the process. Just as shipowners play a vital role in providing the testing ground to bring new lubricants to the market more quickly, so too can industry stakeholders. If stakeholders work together to understand alternative fuels and the risks involved, this will enable shipping to get to the field testing of new lubricants sooner.
“Lubrizol is already sharing its early investigations and assessments with key partners,” says Bown. The firm is also contributing to discussions on engine designs and fuel and lubricant requirements through industry forums, including CIMAC and the Getting to Zero Coalition. These discussions – and the cylinder condition solutions that result - will be critical to enabling the use of alternative fuels in shipping.
Ian Bown is Technical Manager for Marine Engine Oils at Lubrizol.
The opinions expressed herein are the author's and not necessarily those of The Maritime Executive.