Future Development of Flettner Rotor Propulsion
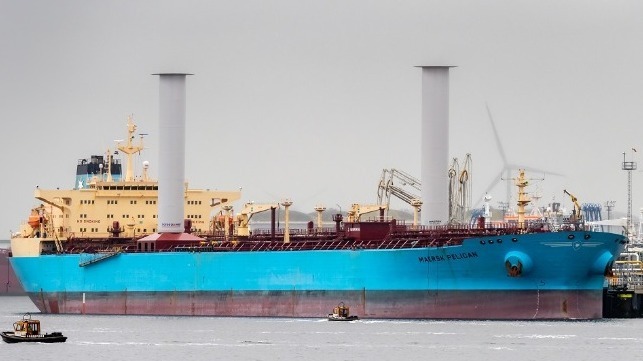
Wind energy historically provided the basis for vessel propulsion, using sails and sometimes kites. During the 1920s, engineer Anton Flettner developed large cylinders spinning on a vertical axis to redirect a wind stream to produce vessel propulsion. There is scope to combine recent developments in multiple technologies with Flettner cylinders to enhance the performance of wind-assisted and wind-propelled commercial vessels.
Introduction
Flettner rotors are large cylinders that spin on a vertical axis, redirecting the flow of wind energy to produce a reaction in the form of propulsion on large vessels sailing through windswept regions of ocean, reducing fuel consumption.
Flettner Rotor operation might be compared to that of an aerosol can where a small amount of pressure applied to the control button releases a large amount of pressure from storage. A small amount of energy from an electric motor is required to spin the Flettner cylinder, which redirects the flow of wind energy to produce a massive amount of propulsive thrust. There are alternate methods by which to sustain cylinder rotation.
Geographic locations
Several regions of the world experience reliable and steady winds. Coastal winds occur in many regions after sunrise, with wind blowing inland from sea to land and in the opposite direction after sunset. Both wind directions provide the basis for wind-based vessel propulsion, with predominant wind direction determining the choice of wind-driven propulsion technology. While some wind-powered vessels would need to sail directly into headwinds, other vessels would sail parallel to the wind, while even other vessels could redirect kinetic energy from side-winds to achieve propulsion. Already proven technology can convert energy from tail winds and side winds.
Some ship captains had recorded fuel consumption on their vessels on certain voyages, prior to and after installation of Flettner rotors. They reported up to 25% reduction in fuel consumption along sections of the voyage with rotors in operation. Whereas sails of clipper ships delivered up to 3,500-horsepower, groups of deck-mounted rotor sails are estimated to deliver up to and over 10,000-horsepower on voyages that pass through windswept regions of the ocean.
Related technologies
The concept of “convergence of technologies” combines features of existing and proven technologies with large cylinders that rotate on a vertical axis above the deck of a ship. Cylinder rotation requires a small input of power to redirect a large amount of wind energy that would result in propulsion. The cylinders need to rotate either clockwise or counter clockwise depending on wind direction. Bi-directional mechanical gearboxes are available in the railway industry, with bi-directional electric motors also being readily available. Flywheels along with variable ratio transmissions and multi-speed gearboxes are also readily available.
Maritime vessels can carry the weight and accommodate the volume of multiple container size grid-scale batteries that could sustain several days of cylinder rotation aboard commercial vessels. Certain configurations of deck-mounted wind turbines could through gear mechanisms, initiate and sustain cylinder rotation. Waterwheels could likely sustain deck-mounted cylinder rotation after a vessel has reached a suitable sailing speed. During daylight hours, electric energy from solar photo-voltaic panels could energize electric motors that sustain several hours of cylinder rotation.
Wind turbines driving cylinders
Tilting a self-starting, vertical-axis bladed wind turbine by 90-degrees lets it rotate on a transverse horizontal axis. Installed at low elevation above the deck, it would drive a vertical-axis Flettner rotor through a bi-directional gearbox. A deflector would guide wind energy only to the working section of transverse-axis bladed turbine. Above certain wind speed, bladed small wind turbines of sufficient size and spinning on a horizontal axis would be able to sustain rotation of large non-bladed deck-mounted cylinders, allowing them to redirect a massive amount of wind energy to produce vessel propulsion.
An alternative approach could involve low-cost, long-life grid-scale batteries housed inside shipping containers and carried far below deck. Battery-driven electric motors could sustain propeller driven propulsion for short distances, departing from port and sailing into a port. Batteries driving the cylinders via electric motors could sustain vessel propulsion between ports of origin and destination, both located in windswept regions. Future wind-powered vessels could combine batteries, flywheels, water wheels, Flettner rotors, suction sail propulsion along with kite technology on the same vessel, so as to use trade winds and side winds for propulsion.
Conclusions
Wind energy is presently assisting some piston engine vessels with propulsion. There is also growing interest in developing commercial vessels that sail almost exclusively on wind energy, potentially sailing the routes of clipper ships and schooners of an earlier era in both short-sea and trans-ocean shipping. While a small number of wind-powered passenger cruise ships use deck mounted aeronautical wing type sails and kite-sails for propulsion, future wind-powered cruise ships could feature the combination of Flettner rotors, suction sails, and stacked kite technology to provide propulsion.
The opinions expressed herein are the author's and not necessarily those of The Maritime Executive.