USCG Recommends Bollards Test After Failure Caused Drillship Allision
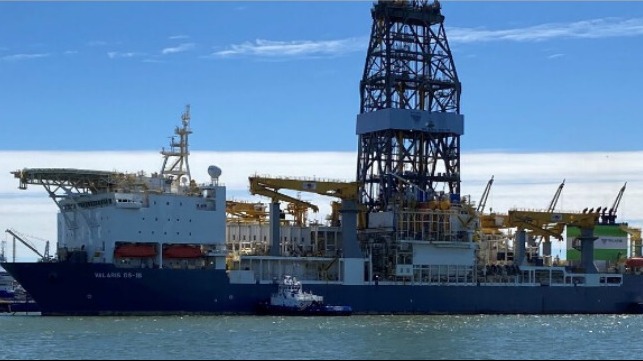
The snapping of a deteriorated bollard caused the collision of a drillship and a bulker in Pascagoula, Mississippi last year, leading to nearly $5 million in damages, the National Transport Safety Board (NTSB) has determined. They raise concerns about a lack of testing and inspections while also noting the increased size of ships and its impact on previously sufficient facilities.
In an investigation report on the collision of offshore drilling unit Valaris DS-16 and dry bulk carrier Akti in March last year, the NTSB found out that a deteriorated bollard that failed at the ST Engineering Halter Marine and Offshore (STEHMO) shipyard dock had also been modified to increase its height. The area was experiencing strong winds higher than normal during the passage of a cold front which created the added forces that caused the failure, and the vessel laid up undergoing repairs did not have power, despite using its anchors, to stop its uncontrol drifting across the channel.
The 752-foot drill ship was built in 2014 and is 52,242 gross tons. The vessel had been taken out of service and laid up in Las Palmas, Spain in August 2020. The vessel arrived at the shipyard in Mississippi on January 6, 2022, to undergo work for reactivation. According to the NTSB, it has a draft of 49 feet with its propulsion provided by six thrusters. Due to limited clearance at the dock, the thrusters were reacted above the keel before mooring rendering propulsion unavailable although the diesel generators were continuing to provide power while the vessel was docked.
A detailed ‘Quayside Mooring Analysis’ was carried out before the arrival of the drillship that identified some concerns including the spacing of the bollards. Although the analysis considered the loss of a single mooring line and calculated critical components, it did not consider the unlikely event of losing a bollard. Shipyard engineers did not have any records for pull test ratings specifically conducted on the bollards but they did have a pull certificate for 1534 metric tons from a tugboat’s bollard pull test at the pier. Before the vessel arrived in Mississippi, the captain working with the engineers modified the plan which was approved by the operating company engineers and sent to the shipyard.
The vessel was undergoing repairs with welders, operators, contractors, and others living aboard. At the time of the incident, there were 164 people aboard. In early March, the captain of the Valaris DS-16 became aware of a weather forecast for a strong cold front. Around the same time, a semisubmersible rig arrived in the yard docking to the north of the drillship and requiring a slight rearranging of some of the lines. Weather forecasts for March 12 predicted winds at 25 knots with gusts to 30 knots and gusts as high as 44 knots by morning.
Shortly after midnight, the captain woke believing he had heard the sound of a mooring line snap. Crewmembers confirmed that bollard 6, which secured four bowlines for the DS-16 and two stern lines for the nearby rig had broken free from the dock at its base. The bow of the DS-16 began to peel away from the pier and the remaining mooring lines parted. The general alarm was sounded while they also used the radio to alert nearby vessels and summon tugboats. Everyone aboard was mustered as they prepared for possible contact with another vessel.
Both anchors were deployed and several tugs arrived to assist. The anchors stopped the drift, but the tugs were unable to hold the stern and at 0041 DS-16 struck the Akti moored across the channel.
In the analysis, bollard 6 was specifically identified as a critical component in the mooring plan. In its report, the NTSB said that it performed ultrasonic thickness tests on the 13 bollards at the shipyard with results showing there was deteriorated steel at the lower portion for most of them besides signs of external corrosion and wastage. Further, all the bollards used to secure the DS-16 were modified from the original 1997 design, with vertical components added to each of them to accommodate more lines.
The collision caused sustained damages to the drillship in its riser handling system, deck fittings, transfer hose-reel system, walkways and platforms, and other equipment on board. A bulwark panel was also deformed on the starboard side with insets on the side shell plating and port stern also noted. Although there were no damages to the underwater portion of the hull, the drillship damages were estimated at $4.2 million. The Akti sustained damage to the starboard-side bridge wing, handrails, deck coaming, side shell plating, and lighting fixtures estimated at $778,000 while STEHMO estimated the cost to replace bollard 6 at their facility at $20,000. There were no reported damages to Chevron dock no. 6 where the Akti was moored.
The investigation concluded that under the pressure of strong winds, coupled with the fact that the drillship was an extremely large vessel, bollard 6 snapped and caused Valaris DS-16 to drift and collide with the bulk carrier.
The broken top of bollard 6 was not recovered from the channel and was not analyzed although a post-casualty measurement of the remaining 18-inch-diameter base of the bollard showed that the steel wall thickness was less than 0.25 inches on the side farthest from the edge of the pier—an apparent reduction in thickness of about 0.5 inches from the original bollard design of a wall thickness of 0.75 inches.
Additionally, several bollards showed signs of external corrosion and wastage while steel wires and chains were looped around the bases of bollards from which pier fenders hung, causing chafing and wear.
The NTSB concludes by highlighting that neither the U.S Coast Guard nor Occupational Safety and Health Administration (OSHA) has regulatory requirements for facilities to inspect and verify loading capacities of bollards at shoreside facilities. They also recognize the normal issues of exposure to seawater created a high risk for corrosion, as well as issues of wear. Further, “As a result of continuing increases in vessel size and sail area, bollards that were previously sufficient may not have adequate capacity to moor larger vessels,” writes the NTSB.
The Coast Guard has recommended that facility owners and operators develop routine inspection programs for bollards and other mooring equipment.