Report Points to Rudder Failure in 2022 Grounding of Hagen Oldendorff
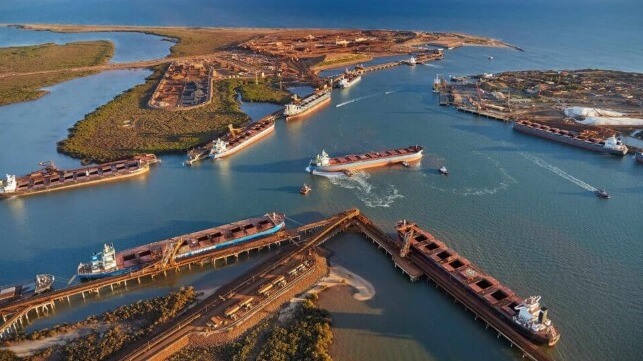
The Australian Transport Safety Bureau (ATSB) released a preliminary report on the grounding of bulk carrier Hagen Oldendorff in the port of Port Hedland in April 2022 saying that an initial review of the situation points towards “rudder failure” as the cause. The vessel grounded, suffering hull damage, with the pilot aboard at the time saying it appeared the vessel suffered a steering problem.
The interim report was issued after the fact finding and initially appears to confirm the pilot’s report. The ATSB expects to have its final conclusions and report by the first quarter of next year.
The report shows that on the morning of April 7, 2022, the 984-foot Liberian-registered bulk carrier arrived at Port Hedland, Western Australia from Tianjin, China, to load a cargo of iron ore. Loading was completed on April 8, with the 208,588 dwt bulker taking on 205,465 tonnes of iron ore. The vessel was registering a draft of approximately 60 feet fore and aft with its departure planned for the next tidal window on the following day.
The Hagen Oldendorff departed the dock shortly after midnight with the required four tugs available to guide the ship as it made its way from the port. About 50 minutes after departure, the ship was traveling through the harbor channel at 6.8 knots, with one tug connected to its stern and two others closely following. Underway in the channel, the pilot observed that the light on the rudder angle indicators had gone off.
As the ship was moving out the channel, it began to swing to starboard, and the pilot ordered port rudder, and the tug connected to the ship’s stern to pull the stern to starboard, to counteract the swing. Data from the ship’s voyage data recorder showed however that the ship developed a rate of turn of about 3.6 degrees per minute to starboard. The pilot ordered port 10 degrees, followed by port 20 degrees. The pilot also ordered one of the four tugs escorting it to pull the ship’s stern to starboard to counteract the ship’s starboard swing and steady it in the channel.
After issuing the instructions, the pilot queried if the rudder was responding and then ordered “hard to port.” The recorded data indicated that the rudder moved from its initial position of about port 27 degrees to port 35 degrees. At this time, tug RT Clerke was using full power to bring the stern to port while the ship’s rate of turn was 13 degrees per minute to port.
“The pilot reported to the vessel traffic service that the ship had experienced a ‘rudder failure’ and declared a ‘Port Emergency’,” notes the report.
While the ship’s rate of turn to port was reduced, it was not enough to prevent it from grounding on the edge of the dredged channel. Upon coming into contact with the channel’s edge, the ship’s bow swung away from the side of the channel, back to starboard. The tugs were able to gain control of the vessel after the grounding and move it to the anchorage for the investigation.
An underwater hull inspection later identified substantial damage, including holes in the ship’s port side and bottom shell plating. There also was a failure of the transverse bulkhead between the number 1 and 2 port double-bottom water ballast tanks, allowing flooding between them.
Angus Mitchell, ATSB Chief Commissioner, reports that the rudder angle indicator failure meant the pilot and ship’s crew were unable to ascertain the rudder’s position, or whether it was responding to commands. A post-incident inspection found the tracking motor of the bridge’s omnidirectional rudder angle indicator had burnt out, causing a short circuit that tripped the circuit breaker, causing a power outage in all the rudder angle indicators available on the bridge.
The ATSB continues to investigate for any safety issues. The final report will provide a detailed analysis along with the findings of the safety board.