First 3D Printer Installed on U.S. Navy Ship for Evaluation Underway
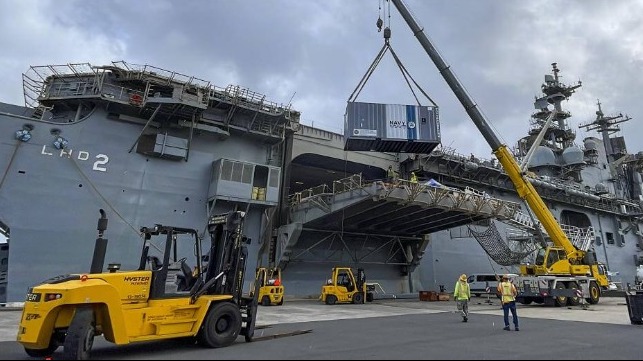
The U.S. Navy recently installed its first 3D printer aboard one of its vessels in a program designed to test the capabilities of the technology and its potential contribution to enhancing maintenance aboard active duty vessels. The Navy joins with the commercial shipping industry which has also been looking at the capabilities of 3D printing and tested the first parts for ships made with the technology.
The 3D printing system was recently placed aboard the USS Essex, a Wasp-class Landing Helicopter Dock currently based at Pearl Harbor, Hawaii. Commissioned in 1992, the amphibious assault ship is testing the technology while it is currently participating in the Rim of the Pacific (RIMPAC) 2022 training exercise.
“Having this printer aboard will essentially accelerate, enhance, and increase our warfighting readiness,” said Lt. Cmdr. Nicolas Batista, the Aircraft Intermediate Maintenance Department (AIMD) officer aboard the Essex. “The capabilities of the 3D printer will enable Essex to become more self-sufficient.”
According to Batista, the 3D printer installed aboard the Essex is one of the fastest printers on the market, capable of fabricating and printing aluminum up to 10 inches by 10 inches. He said that they believe many common components may be created on the ship including heat sinks, housings, fuel adapters, bleed air valves, valve covers, and more, using the technology
During testing and evaluation at sea, a team aboard the Essex will create various shipboard aluminum items with the 3D printer and provide feedback on the results. The Essex according to the Navy is the first ship to participate in the initial testing and evaluation of the 3D printer during underway conditions to determine the printer’s viability when out to sea.
Xerox technician assembling a 3D printer head on USS Essex (US Navy photo by Petty Officer 3rd Class Isaak Martinez)
A team of technicians joined the vessel before she departed Pearl Harbor and in addition to installing and testing the system, they are responsible for training sailors. Among the individuals being trained on the system is Aviation Structural Mechanic 3rd Class Roxanne Barrera who will also assist in training others on her team.
While the Essex has had the capability to manufacture small items needed on the ship, Aviation Electronics Technician 2nd Class Jonah Waage explained, “We have never been able to make something with the precision and intricacy that this new 3D printer will provide, which is important because it will contribute to saving time and money for our Navy in the long run.”
The evaluation of the 3D printer is part of a broader program the Navy is undertaking exploring additive manufacturing which is also exploring the capability of fabricating needed aircraft parts with a 3D printer.
The U.S. Navy has been testing 3D printing for the last few years in a variety of different applications. In 2018, they installed the first prototype 3D-printed metal part aboard the USS Harry S Truman for a one-year test and evaluation trial. By October 2020, U.S. Navy and Naval Sea Systems Command (NAVSEA) reported it had approved a total of 182 3D printable parts in its database and had more than 600 additional parts undergoing engineering review. Those tests were being conducted onshore at fabrication plants with the Navy now looking at the capabilities of extending small part manufacturing to the ships.
The commercial industry has also been exploring the use of 3D printing. Early in 2021, for example, 3D-printed mechanical parts were installed aboard the U.S.-flagged oil tanker Polar Endeavor in a test. After six months in operation, the parts were retrieved and inspected by the vessel’s crew, followed by a remote survey by ABS that confirmed their good condition. ABS approved the spare parts after successful onboard testing on the tanker creating the opportunity for wider applications of the technology.