K Line Considers Using Old LNG Carriers to Build FLNG Vessels
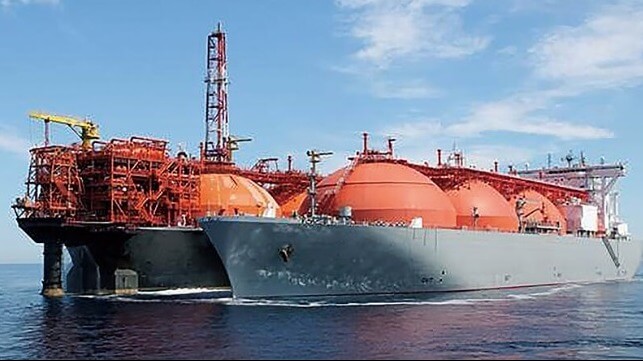
Japanese engineering company JGC Holdings and shipping company Kawasaki Kisen Kaisha (‘K’ Line) working together have developed a new approach to developing floating LNG plants (FLNG). Under their design, which receive approval from ABS, they propose utilizing older LNG carriers to create a cost-effective means of expanding LNG production especially from small to mid-sized fields that might otherwise not be economical to operate.
The companies highlight that since the first LNG carrier was built in the 1970s, LNG transport has increased to the point that there now exist 600 carriers globally. However, in recent years, some LNG carriers have been replaced by newer, more energy-efficient ships with larger carrying capacity, leaving older carriers to languish in ports.
“JGC Global and ‘K’ Line saw an opportunity in the older generation of LNG carriers and, with the backing of Japan's Ministry of Land, Infrastructure, Transport and Tourism, the conceptual design of new type of FLNG hull was established,” the companies said announcing their concept. The challenge they say is to overcome the issues to building FLNGs while capping construction costs.
Floating LNG production, storage and offloading facilities they noted have been adopted as a cost-saving approach to development of new LNG fields. They point out that the approach is appealing because it eliminates the costs involved in laying a pipeline for transporting gas from the field and development of the infrastructure used in production. Further, the companies developing FLNGs have the opportunity to redeploy the floating plants after a field is depleted.
Yet, while the floating approach is being pursued, they note that they vessels require specialized skills and are costly to develop. The design must consider factors such as counteracting wave motion while also creating a very compact structure and addressing safety issues.
“The key components of an FLNG facility are the hull, which contains the LNG storage tanks, as well as the production and liquefaction units on the topside. The LNG storage tanks in the hull require very costly cryogenic materials able to withstand temperatures as low as -162°C. Welding together these materials require special technology, which means that FLNG facilities can only be built by a small number of shipbuilders. This leads to high costs and long delivery times,” said the companies.
Due to the challenges and costs, there are only seven FLNG facilities exist globally, including those in transit and under construction. Yet they noted despite the strong, growing global demand for LNG, there are numerous stranded offshore gas fields all over the world where development would not be profitable using a land-based LNG complex.
Their design concept involves transferring and reusing the LNG storage tanks from existing spherical tank (Moss tank) carriers to the hulls of new FLNG facilities. Transferring and reusing the spherical Moss tanks from existing LNG carriers means there is no need to build new new storage tanks from expensive cryogenic materials, reducing the cost of hull construction. In addition, a wider choice of shipbuilding yards is able to construct the FLNG hulls. This is expected to reduce construction time and cost to expand the global fleet of FLNGs.
The American Bureau of Shipping reviewed the design and issued Approval in Principle (AIP), which the companies are calling as a significant step towards its realization. They plan to use JGC’s experience in FLNG design, procurement and construction along with ‘K’ Line’s experience in the construction of LNG carriers to further this approach. The companies are moving aggressively to build an orderbook for the design that they believe presents strong advantages for the emerging sector.