Side Benefits
Durable, lightweight pumps and piping systems last longer and perform better. They also lower fuel consumption and reduce harmful emissions.
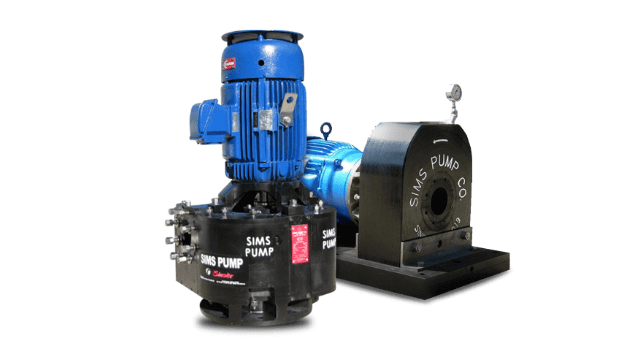
(Article originally published in Mar/Apr 2022 edition.)
Who knew? Product improvements in one area can actually have benefits well beyond their original purpose, proving once again that technological advances – particularly in arcane areas like pumps and piping systems – can lead to wonderful and unexpected results, improving efficiency and decreasing emissions as well.
Computer modeling and other tools are part of the solution – helping maritime sector vendors improve ships’ fuel efficiency and other aspects of operations. Those improvements are available due to changes in both shipboard hardware and land-based software.
Plastics are a good example. They make modern life possible and often make our lives better due to their strength, resilience, and light weight. In the maritime sector, GF Piping Systems is using the versatile material in its products to enhance operations on ships across the globe.
The company, based in Switzerland, has been improving maritime operations since its founding as Georg Fischer AG, in 1802. Today, GF Piping Systems provides plastic piping systems for shipboard HVAC systems and other applications including offshore wind installations. Its products are grounded in the latest technology with the company using computer modeling – among other techniques – to evaluate the effectiveness of its designs, which are constantly evolving and improving.
With such tools, GF Piping Systems has studied how well its piping works including evaluating ways to slow increases in temperature in its systems. Keeping system temperatures lower during their operation is just one way the firm is improving its products’ efficiency. That factor alone, if controlled, can add greater fuel efficiency to such systems, but it’s just one of numerous factors being improved upon by the company.
“The most important savings are in decreasing pressure loss,” says Roberto Chiesa, Head of Marine Business Development.
Significant Fuel Savings
Taken together, controlling temperature and controlling pressure loss in its piping solutions result in significant fuel savings for ships – with up to 30 percent less fuel being used in such systems. That lowered fuel use also decreases carbon gas emissions – a secondary eco-friendly benefit of the company’s piping.
Precisely how much cash will this fuel savings amount to over the years in a large passenger ship that runs on oil? Anywhere from $2 million to $2.6 million over 25 years, the company claims.
The ability to control pressure and temperature in its piping is partly due to how the company designs the piping. The pipe’s insulation is more durable than others’ and less apt to corrode.
“We target this product to have a 75-year life,” Chiesa explains. “We aim to keep the piping insulation effective and intact for the life of the pipe.”
The resulting decrease in carbon gas emissions is a big selling point for many. “Customers ask us every day, ‘What are the greenhouse gas emissions?’” Chiesa says. The light weight of the company’s piping is also partly responsible. Its piping products are about 40 percent lighter than metal piping systems.
To further benefit customers, the company recently implemented a new Department of Specialized Solutions, which provides offsite prefabrication for clients and shipboard training for clients’ employees. “Maritime is an old and traditional industry,” Chiesa adds. “But employee training can decrease the time needed for new technology transitions.”
Made in the U.S.A.
Founded in 1938, Carver Pump has been providing U.S.-made pumps to commercial and governmental vessels from the very start. The Muscatine, Iowa company is a third-generation family-owned firm. Its tried and true designs are regularly being evaluated and refined for greater effectiveness and are built to meet Department of Energy standards.
“All of our pumps are made here in the U.S. with most U.S.-made castings sourced locally,” notes Rohan Joseph, Applications Engineer Manager. “We buy local as much as we can.”
In an age of offshoring industry to foreign lands, Carver Pump still counts on U.S. manufacturers to build its products. The company is connected with American foundries that are located within a few hundred miles of its headquarters.
Its solid reputation is well-earned as it’s been assisting the U.S. defense industry for more than 80 years. “We’ve been working in the Navy world since our inception,” says Joseph. “Our designs are always simple and robust. We’re well-recognized in the defense industry.”
To impart greater efficiency, certain things have changed in the firm’s pump designs over the years. For example, composite materials are now used for some pump parts, such as impellers, because composite parts are less likely to corrode than metal parts. Fewer breakdowns due to broken parts mean less downtime and greater overall ship efficiency.
Proof of the company’s products is seen in their longevity, which often outlast many other parts of a ship. “Some of our pumps are out there still working for over 40 years,” Joseph adds.
Another company with deep roots in the U.S. is SIMS Pump Valve of Hoboken, New Jersey. Its origins go back more than 100 years.
“SIMS Pump was founded in 1919 by Admiral William Sims and his brother with the invention of the SIMS pump valve for reciprocating pumps,” explains John Kozel, President. “It started in the Red Hook section of Brooklyn and eventually moved to downtown Manhattan and then to Hoboken as it steadily grew. From the beginning it offered a guarantee of complete customer satisfaction, unheard of in those days and a rarity even today. It’s part of what distinguishes us.”
Recognizing that conventional metallic centrifugal pumps were subject to electrolysis, corrosion, erosion and cavitation when used in corrosive services like seawater, wastewater, sewage and chemicals, SIMS developed and patented the first Simsite® impellers and casing rings in 1955.
The success of these products led to the development in 1985 of complete Simsite pumps, which won numerous awards and received approval from – among others – the U.S. Navy, which remains a big customer. In addition to marine and Navy applications, SIMS provides pumping solutions for companies, municipalities and cities around the world for many different services and applications.
In 1995, for example, it designed the largest composite vertical turbine pump in the world – two of them, in fact – for Potomac Electric Power in Virginia. More recently, SIMS designed and built a two-stage horizontal split case pump for a BP refinery in the Midwest.
Simsite itself is a patented carbon fiber structural composite manufactured exclusively by SIMS in the U.S. It’s 100 percent machined and utilizes a tridimensional weave, affording outstanding mechanical properties. SIMS pumps, impellers, casing rings and other parts never corrode in seawater, wastewater, sewage or river water and have excellent corrosion resistance for many chemical applications as well.
Because SIMS products are completely machined from solid blocks of Simsite, they aren’t subject to internal voids, cracks or imperfections like cast or molded products.
“The proof is in the performance,” says Kozell. “One very large Simsite impeller and casing ring set was installed in a main circulating pump in 1965 and ran continuously until 2020 when it was sent back to our factory for reconditioning. It was designed and engineered for 14,000 gallons per minute of seawater and lasted 55 years in seawater service without a hitch.”
Unlike other manufacturers, SIMS does not make “standard pump products.” Its products are custom-engineered for the customer's operating point, making that point the best efficiency point and thereby increasing reliability, durability and performance. SIMS’ products are value-added and must be requested and specified by the customer’s engineering or maintenance departments and not through standard purchasing departments.
“Most purchasing departments only look at ‘low price’ and don’t consider reliability, longevity, efficiency and durability,” Kozell says, “so engineered products like ours must be specified in order for purchasing to select them. That’s given us a leg up.”
Added Value
With the help of often old but proven technology and the addition of new technological advances, companies like GF Piping Systems, Carver Pump and SIMS Pump Valve are helping shipowners boost performance, save on fixed costs and avoid unplanned expenditures.
Added value comes in the form of fuel savings, lowered emissions, longer life and the use of eco-friendly materials – the unexpected but welcome side benefits that follow naturally from choosing quality vendors.
Jonathan Barnes is a Pittsburgh-based freelance writer. This is his first appearance in the magazine.
The opinions expressed herein are the author's and not necessarily those of The Maritime Executive.