Saving While Spending
When it comes to coatings, upfront investments can pay off big later on.
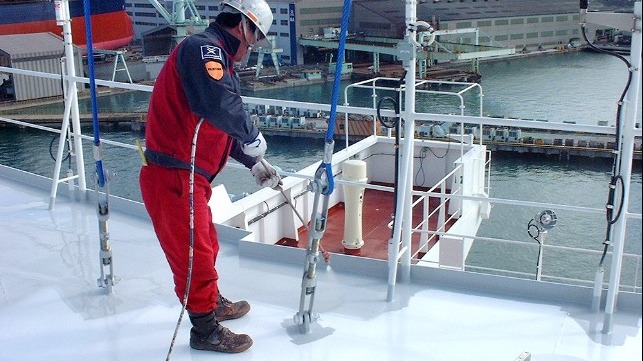
Vessel coatings and maintenance schedules may soon have to be reevaluated as a result of the extended layups over the last year or the sudden long waits at crowded ports now that global commerce has revived. Corrosion and biofouling wait for no man and can have dire consequences if left untended for too long, particularly given today’s stringent exhaust regulations and the intense competitive environment.
While vessel profiles may change unexpectedly, the paint community can help save on costs in inventive ways. The good news is that the coatings business is taking a big-picture approach including more data, improved preparation, new monitoring technologies and maintenance machinery and, of course, better coatings.
Most importantly, fuel and exhaust performance stay at optimum levels whether a vessel is moving, sitting or facing schedule disruptions. Tests have also shown that some new topside coatings and waterline paints resist abrasion and keep decks cool. Anti-corrosion prep and maintenance are also in the news, which we’ll cover after looking under the ship.
Hull Bottom Protection
Hull bottom protection has seen challenges between antifouling and low-resistance coatings, robotic cleaning and regulations concerning invasive species, and monitoring fuel costs and pollution. While these targeted efforts have had compromises and conflicts, Jotun Paint has just introduced a complete, coordinated approach to all these issues.
Jotun’s Hull Skating Solutions package begins by applying SeaQuantumSkate, a slick antifouling coating that answers the polishing problem by matching the bottom paint to its ROV hull-cleaner’s brushes. No biocides are released into the water during cleaning since the brushes are matched to the paint. No excessive biocide is released when the ship is moving because the paint is hard enough. The hull is maintained so well that invasive species are not carried around from port to port.
As a result, fuel use and exhaust pollution are always minimized, never worsened or compromised in any up-and-down cycles of biofouling and cleaning. Software monitors performance and lowers costs in real time. Initial cost is higher, but it pays for itself quickly.
Jotun, along with partners including Kongsberg, developed the HullSkater. It’s a bespoke inspection and cleaning ROV for this system only. You’ll always carry it onboard, and Jotun operates it for you. This avoids scheduling problems or the cost of getting to a port with a cleaning ROV.
There are obvious savings, and overall you eliminate surprise haul-outs and irregular expenses that upset both charterers and stakeholders. The system also includes recorded data on fuel efficiency on all voyages.
Performance Standard
To answer regulators’ concerns about fuel savings, a performance standard was developed called ISO 19030. Published in 2016, it provides practical, transparent methods for measuring changes in ship-specific hull and propeller performance. It’s a response to industry calls for a fair method of assessing claims of efficiency gains.
Commenting on the challenges, Stein Kjølberg, Global Sales Director of Jotun Hull Performance Solutions, says the focus on energy efficiency and sustainable shipping is critical: “If you want to stay ahead of the game, customers need to recognize you as a provider of proven and reliable services that can be measured. Irrespective of the cyclical nature of shipping, it’s the only way forward for responsible suppliers, owners and the environment.”
He adds that ISO 19030 “opens up a huge potential for owners/operators, management companies and charterers to establish performance levels for their vessels in a very inexpensive way.”
HullWiper, Hempel, Nippon Paint and others also offer ROV inspection and cleaning systems. With new standards from BIMCO and ICS for capturing organisms from in-water cleaning of moderate and heavily fouled bottoms, HullWiper makes use of water jets to clean off growth and then filters the effluent from its ROV. This approach limits invasive species.
On the other hand, Jotun’s “always clean” goal is to arrive in a harbor with a clean bottom and to wipe off only local biofouling after a prolonged wait in a port. All these programs also help control fouling problems when a newbuild is launched but sits in the yard during months of final fitting out.
On the coatings side, Nippon Paint has recently introduced an improved antifouling paint that works whether a vessel is moving or idle. This latest FASTAR coating can have hydro-gel added for increased fuel savings. FASTAR also has improvements in film thickness and drying time. It’s the fourth generation of its Aquaterras formula.
“Chasing Rust”
Rust prevention and removal will get more attention now that NACE (National Association of Corrosion Engineers) and SSPC (Society for Protective Coatings) have combined to form the newly minted AMPP (Association for Materials Protection and Performance).
“We all know corrosion is expensive and negatively affects asset availability,” says Buddy Reams, Chief Technical/Maritime Officer at AMPP. “One of the fundamental issues we face on asset management and integrity, particularly with ships, is that corrosion-control efforts are largely after the fact or, as some describe it, like ‘chasing rust’. Designing and building with corrosion in mind is hard because it’s perceived as being higher cost, but it almost never is if you factor in the total lifecycle cost related to corrosion.”
Reams says effective corrosion management has to include actions and decisions during the asset’s operational life: “It’s never too late to start using corrosion management because the cost savings can be significant. Leveraging all the benefits of existing materials and methods in a strategic and coordinated fashion can help keep your crews and maintenance teams ahead of the game and ships operating. Participating in a technical exchange with groups like AMPP can help match your company’s specific needs to the many different solutions that exist in the market.”
The need to remove old paint and rust has spawned methods ranging from chipping to sand blasting and some interesting developments in between.
Since the 1970s Rustibus Worldwide has been an innovator in the business of mechanically removing old coatings and rust from decks and cargo holds, including vertical surfaces. Its most popular unit looks like a lawn mower with flailing rotating chains and an optional vacuum to collect dust. There are various sizes and larger devices for vertical surfaces like cargo hold walls on bulkers.
“We are also working on new innovations in cargo hold cleaning methods,” says CEO Kristian Dalseide.
Demonstrating its commitment to green solutions, Rustibus in 2018 launched the nonprofit “Rustibus Clean Ocean Initiative” (RCOI), a global program to promote and collaborate with clients to reduce plastic and waste in the oceans. It pledged to “promote, endorse, and execute R&D on products that can be provided to shipowners that share our commitment to making a difference in our oceans worldwide. We will also dedicate a portion of the Rustibus Group profits and resources towards this initiative as well as seek sponsors in ship-owning organizations, maritime authorities, maritime forums and foundations who share our vision of a cleaner ocean for all.”
Another big name in corrosion prevention is Singapore-based DEN-JET, which has developed a wide range of water blasters and waterjets to remove coatings and corrosion above the waterline, all the while holding dust to a minimum to prevent pollution. With multiple offices around the world, DEN-JET products are used in marine, industrial and offshore applications.
Deck Paint
What’s black and feels like white paint? Answer: Black paint with special pigments that reflect solar infrared rays. Although it’s readily available for vessel decks in light to dark grey, other colors are possible too.
Marine coatings like Coolshield and Nippon Paint’s Ever Cool deck coating have been applied to vessel decks around the world. The Low Solar Absorbing pigments can be neutral in low-temperature weather but heat-reflective in hot, sunny conditions.
U.S. military research has led to “cool” non-skid coatings from NCP Coatings. Formulated by the Navy Research Laboratory, the SiloXoGrip Polysiloxane Non-Skid coating – beyond the temperature advantage – mixes, pours and spreads more easily than previous deck coverings based on epoxy or silicone alkyd.
In addition, NCP’s non-skid coating technologies, while performing like a conventional two-component urethane system, use no unhealthy catalysts. You get the durability advantage over epoxy deck coatings and avoid the safety concerns from urethanes.
Paints that resist abrasion, when applied properly, continue to find places to serve on topsides that rub against lock chambers, canal seawalls, ice floes and piers. With a bit of non-skid, they go onto walkways and with more non-skid resist vehicle tires on ferry and ro-ro decks.
AkzoNobel’s International Intershield 163 Inerta 160 is a proven ice-abrasion resistant coating with high solids and low VOC content. A special mix of ingredients makes for a durable surface in cold weather to resist ice but also withstands hot weather. Intershield 163 Inerta 160 has been providing vessels that traverse icy waters with a durable, smooth surface and low frictional resistance for 40 years.
On the Horizon
Fumeless coatings for tight, contained spaces are being developed in Korea, and the trend is moving around the world to other coatings companies.
Look for software developments from paint companies that will help vessel managers with maintenance and performance efficiencies, thereby avoiding expensive surprises.
Maritime consultant John Minetola is a frequent contributor to The Maritime Executive.
The opinions expressed herein are the author's and not necessarily those of The Maritime Executive.