No Tapping Required
Achieving optimal performance with condition-based maintenance has come a long way
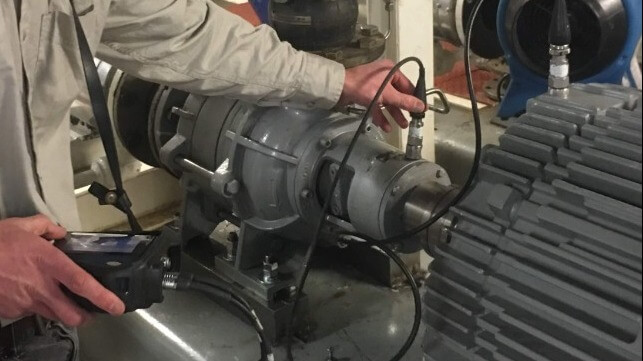
(Article originally published in Sept/Oct 2022 edition.)
For as long as mankind has built machines there’s been a need to keep them in peak operating condition.
We can imagine the earliest sailors with their hand on a line, feeling for unfamiliar vibrations through the deck boards – making use of all their senses to determine when something felt “off.” As the complexity of machinery increased, so too did the techniques. The advent of the steam engine found engineers walking alongside the train, tapping steel wheels with a small hammer. The resulting sound would indicate condition: A clear ringing meant the wheel was good; a dull thud meant it was cracked and needed attention.
Vibration analysis was born.
The First Breakthrough
One of the earliest breakthroughs in equipment maintenance theory didn’t come from a mechanic or engineer, but a biologist.
Conrad (C.H.) Waddington was a British scientist conscripted into the Royal Airforce Command in World War II. Tasked with figuring out how to more effectively combat German submarines led Waddington in an unlikely direction – maintenance.
He found that the B-24 Liberator bombers in use spent an inordinate amount of time in the shop for maintenance, both scheduled and unscheduled. At the time, it was felt that more maintenance would ensure flight readiness, but after collecting the data it was discovered that unscheduled repairs rose sharply right after the 50-hour scheduled maintenance.
Scheduled maintenance was doing more harm than good!
The team realized that instead of preventing unscheduled breakdowns, the frequency of scheduled maintenance was in fact increasing them. This became known as the Waddington Effect. By adjusting the frequency of maintenance to correspond to the actual condition of equipment and the frequency of use, Waddington’s team was able to exceed best averages of all squadrons by 79 percent.
The Second Breakthrough
Moving into the 1970s, maintenance theory became more defined and machines more complex.
Increased efforts to minimize downtime led to the creation of Reliability Centered Maintenance, as delivered to United Airlines following a study by Nowlan and Heap (1978). In it, they identified that almost 90 percent of failures were random in nature with the majority of those being “infant mortality.” Only 11 percent were age-related. This led to the conclusion that nearly all the equipment would benefit from condition monitoring while only a small percentage truly required time-based overhauls.
Condition monitoring (CM) hit the mainstream.
Into the Present
One of the longest running American companies specializing in CM is the Condition Analyzing Corporation (CAC). Founded in 1969 with headquarters in Florida, CAC serves ships and tugs worldwide.
In the 1980s the founder, Robert H. Wallace, worked directly with the Society of Naval Architects & Marine Engineers (SNAME) to set the original standards for vibration analysis. Wallace also helped pioneer a class-approved maintenance program that eliminated the need for opening certain equipment for inspection when approved condition monitoring was in place. To this day, the company stands at the industry forefront with the Senior Engineer sitting on the ISO committee, setting vibration standards for shipboard rotating machinery.
CAC works with vessel operators by sending engineering technicians onboard at preset intervals to work with the chief engineer and take vibration readings. But what are they measuring?
Vibration measurements are an effective way to quantify the forces acting on a machine to assess its condition. The measurements are evaluated by trending levels over time, comparing levels between sister machines and to vibration standards. The analysis is entirely dependent on the accuracy and repeatability of the data as well as the knowledge of machine operating conditions (rpms, loads, external vibration influence) at the time of data collection. For these reasons, trained technicians are sent to collect the data and record essential information.
With a list of critical machines, the technician takes vibration measurements on shipboard machinery at bearing locations in three measurement planes using a handheld analyzer. The tech ensures exact placement of the sensor to ensure consistent measurements and notes operating conditions and any visible issues.
A team of analysts reviews the data in many different forms including spectrum, time waveforms and phase diagrams. The analysis is similar to that of a doctor interpreting an EKG reading. Reports are generated that focus attention on those machines that may require maintenance. This helps prioritize maintenance funds and man-hours. Further, it enables proactive spare parts planning and ordering, thus avoiding costly overnight shipping and overtime for unexpected failures. These reports are available to clients on the CAC Decision Point® website.
CAC also provides thermographic inspections that improve safety by evaluating the operating condition of the ship’s electrical systems. Reports provide locations of "hot spots" and recommend necessary corrective procedures.
Transporting Data, Not People
Advanced Mechanical Enterprises, another firm based in Florida, also offers CM analysis – but with a twist. Helping operators reduce costs, AME’s solution is to provide crews with the needed tools and training and then provide analytical and technical support remotely, leaving the onboard team to perform the actual data capture.
Starting with a baseline survey onboard, the technician maps the machinery and data collection points and trains the ship’s crew on how to operate the collection device – a highspeed handheld data collector from Pruftechnik (now Fluke). Machinery is marked with RFID tags, and the handheld has graphics to assist with placement.
Data is then collected onboard at fixed intervals and sent ashore for analysis.
While ready and able to attend onboard for more complex issues, a customer study found a 45 percent cost savings over five years in data collection alone while, at the same time, collecting twice as much data due to increased frequency as the engineers make their standard rounds.
The company is ABS-certified as approved external specialists for Condition Based Monitoring and celebrated its 30th anniversary this year.
Analysts to the Rescue
All machinery has a mean time between failures. This is the average time between system breakdowns and is used as a measure of reliability for complex or critical equipment. The real work of condition monitoring is the analysis of the spectral plots, building of trends and tracking of equipment time in operation.
Typically approached in a tiered fashion, the analyst will start by looking at the overall vibration that falls within a range specified by the ISO and assigned a color of either green, yellow, or red. Next, the spectrum and time wave form data can be used to determine vibration severity. Finally, the vector of vibration (phase) is checked. Out of balance or out of alignment are very similar but require different fixes. This helps pinpoint which issue it is and where it’s coming from.
By taking the trends over time and providing a simple traffic light-style report, analysis can show equipment degradation at a fine level and provide recommendations for repair or replacement based on real data. The result is fewer spares required, less maintenance and reduced downtime.
Sensing Vibrations
Condition monitoring doesn’t only happen while making the rounds anymore.
Valmet, a leading global provider of process technologies, automation, and services, develops automation systems and flow control solutions for a range of industries. Its DNA Machine Monitoring system utilizes fixed sensors installed on machinery, cabled to I/O stations for real-time collection of data for critical machinery and at cyclic intervals for auxiliary machinery. This enables 24/7 monitoring using alarm limits, trend tracking and signal analysis.
Combined, the vessel is prepared with the tools for predictive maintenance and appropriate service scheduling.
Valmet has taken this a step further and developed a suite of wireless sensors including piezoelectric accelerometers and temperature sensors, triggering sensors, velocity RMS sensors and dynamic pressure sensors. Using these eliminates the costly installation of a wired system to an existing plant. The sensors can be paired with the Valmet Maintenance Pad, which can connect and measure with four units simultaneously during a walk-through data collection.
At the most advanced end of the remote condition-monitoring spectrum sits Siemens SISHIP EcoMain.
The system’s goal is to collect information in a consistent format, then use that both onboard and ashore to help optimize operational performance. It does this by collecting data using existing standards, which allows for analysis regardless of the equipment supplier. The data is then sent to either a Web or local server where it can be analyzed using a suite of available apps.
The applications used onboard include modules such as Maintenance, Logbooks, Energy Efficiency, Emissions, Fuel Consumption and more. Meanwhile, the data is also sent to the EcoMAIN Fleet Management Platform shoreside. With secure remote access, this allows for land-based evaluation of data collected for the entire fleet.
The goal of the EcoMAIN Suite is to provide an open digital ecosystem that allows different suppliers to offer their solutions while giving the operator a secure system in which to optimize daily operations. This breaks down silos and moves the industry toward the next level of digitalization while also supporting decarbonization and sustainability targets.
Where we go one, we go all.
The Next Evolution
Maintenance theory has yielded impressive advances over the past 200 years.
From tapping on steel to advanced pattern recognition and trend analysis, machinery that is increasingly complex can now be managed in such a way that optimizes uptime and allows for maintenance to be performed when it is needed – not when it fails.
The cost savings from avoiding unnecessary, strictly time-based maintenance is huge. Taken a step further, a smart strategy of critical spares helps reduce the amount of costly equipment sitting on the shelf. Instead, it leaves operators free to focus on what needs to be fixed. The entire operation relies on a few key components.
No tapping required. – MarEx
Master mariner Sean Hogue is a frequent contributor to the magazine.
The opinions expressed herein are the author's and not necessarily those of The Maritime Executive.