Is There Room in the BWT Market for a Filterless Treatment Method?
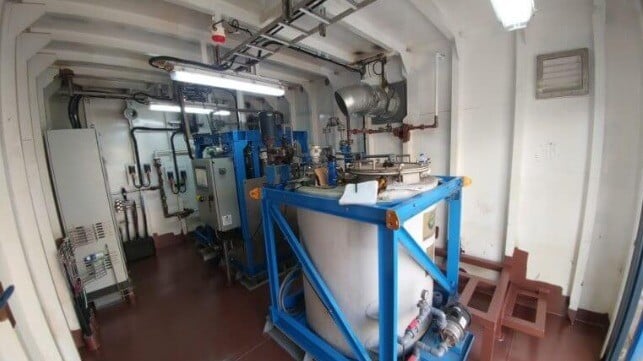
The U.S.-based company Scienco/FAST® believes that there is still room in the market for a filterless approach to ballast water treatment. The company's InTank® BWTS is changing the way vessels can achieve ballast water management with less impact to operations and more certainty of compliance.
Giles Candy, InTank® Business Development, answers some questions about this different approach to ballast water treatment.
What are the big differences between traditional and InTank® BWTS?
The biggest differences are that InTank is filterless and treats ballast during the voyage. This allows a vessel to complete its in-port ballast operations normally. No treatment, power use or crew resources are needed in port to achieve ballast water compliance. Operators can ballast and deballast, including by gravity, as normal, whatever the water quality. On discharge, ballast is already recorded as treated and neutralized – discharge as normal. The work of treatment is still done but at sea where there is more time and less stress on vessel and crew.
How does InTank® work as an alternative to in-line BWTS?
In port operations are normal. InTank’s work starts at sea when the crew elects to start treatment. Then a circulation pump draws ballast aft, usually through the ballast main, to a “Dosing Module” (DM), and returns it to the same ballast tank through in-tank mixing nozzles. This circulation loop provides the means of adding bleach (NaOCl solution) to the ballast water and mixing in the tank to achieve target total residual oxidant (TRO) levels. The NaOCl can be generated using the InTank Electro-Chlorination (EC) option or stored onboard as a bulk chemical using the InTank BC option. The DM enables monitoring of TRO levels inside a circulated ballast tank and, importantly, it is used to apply and mix neutralizer in the tank before discharge.
In contrast to in-line BWTS, InTank measures TRO during the treatment process. If the target TRO is not present, a second “maintenance dose” of NaOCl (TRO) is added. This interim treatment step allows InTank to fully treat even the most challenging waters. An in-line “one shot and done” system cannot account for more challenging waters. When complete, treatment is noted by the control system. The tank can be left in the “treated” state until a day or two before discharge when the tanks are neutralized. Again in contrast to in-line BWTS, InTank neutralizes in the tank before discharge.
How does InTank® improve vessel operations?
Being filterless and operating during the voyage, InTank allows a vessel to complete its ballasting operations as normal. I think crews appreciate this benefit of InTank as much as any, since port time is busy time. Treatment still has to be completed – but at sea when there are fewer demands on the vessel and crew. Clogged filters or slow ballasting / deballasting, due to poor water quality or wrong salinity, are not issues.
If there is an issue with the InTank treatment during the treatment process, the vessel is at sea. The issue can be solved, and treatment completed – no port time has been lost. The vessel’s commercial schedule is not affected, so it’s easier for the crew.
Treatment, even of challenging waters which require re-dosing, is completed automatically. Crews start the InTank system when they want to during the voyage. InTank completes treatment automatically and notifies when tanks are treated. The crew then chooses when to run the neutralization process; and again, InTank automatically completes the process. It really is a simple robust solution for the crew and the vessel.
Interestingly, InTank sizes its hardware to match the volume of ballast and time available to treat. For larger vessels, where the size of the treatment system is usually fixed by the size of the ballast pump(s), InTank can offer smaller, less expensive hardware, particularly the Bulk Chemical option.
Another niche but significant application for InTank is semi-submersible vessels. The normal operation of these vessels is very difficult to achieve given the ballast water regulations. However, InTank allows a semi-submersible to complete its rapid “in-place” flood and drain operation without treatment. No other BWTS can do this. Notably, InTank is now installed on seven of Boskalis’s most iconic vessels, an achievement for a newcomer to this market.
How does InTank® provide the value of Ballast Water Compliance to a vessel?
The ability to re-dose partially treated ballast, if necessary, with additional TRO is something unique to InTank. Re-dosing ensures that a uniform intensity of treatment is applied no matter what quality of water is ballasted. This adaptive, robust approach ensures the most confidence of biological compliance, however challenging the water is. Unfortunately, the value of D2, biological, compliance is not recognized today. As compliance becomes required this value will be significantly more appreciated.
Recording neutralization in the ballast tank is also unique to InTank, and again, a robust way to ensure technical (TRO) compliance. InTank will have a record of the tank’s treatment and neutralization status before ballast discharge begins. There is no in-line measurement, treatment or conditioning required; simply discharge pre-neutralized water. Again, this takes pressure off the crew, providing more value and the knowledge the vessel is not chlorinating the bay.
Are there any new InTank® developments?
Scienco/FAST® is bringing the InTank FITT® system to market. This system is a remarkably small (about 0.5m2) version of the InTank Bulk Chemical system. It is aimed at the smaller end of the commercial vessel market. Fully assembled, the hardware is small enough to fit through a watertight door. The OPEX of the Bulk Chemical system is slightly higher than the Electro-Chlorination system, but the CAPEX, particularly where FITT can be used, is fractional. We are excited about the value we are bringing to market with this evolution of InTank.
The InTank FITT® BWTS
FITT will use an amperometric probe to measure TRO, a significant improvement over current TRO measurement devices, making InTank even more robust and crew friendly.
What is Scienco/FAST® and what commercial success has InTank had?
For over fifty years, Scienco/FAST has been internationally recognized as an original equipment manufacturer specializing in robust sewage and water treatment equipment for the marine industry. Mr. Robert Rebori, president of parent company BioMicrobics, had been quietly researching ballast water treatment systems for some years; when the opportunity came, he added InTank to Scienco/FAST’s suite of marine products. InTank was developed and certified with great investment by Envirocleanse, producing an innovative second generation BWTS –something much needed in this market. Being robust, simple, and effective, InTank fits the profile of Scienco/FAST’s established product lines.
The system is already installed from MR to VLCC, Handy to Cape. Additionally, many semi-sub HL vessels, barges and drill rigs have installed InTank for the unique operational advantages it brings to their operations.
Ask your questions and find out how this innovation could work for your vessels. Find out more at www.intankballast.com, or visit SciencoFast on Twitter, Facebook or LinkedIn.
This message is sponsored by Scienco/FAST.
The opinions expressed herein are the author's and not necessarily those of The Maritime Executive.