Op-Ed: Is a Fossil-Free Future for Shipping a Realistic Goal?
Without extreme caution, we may pull high-carbon fuels into the value chain in pursuit of the zero-emissions dream.
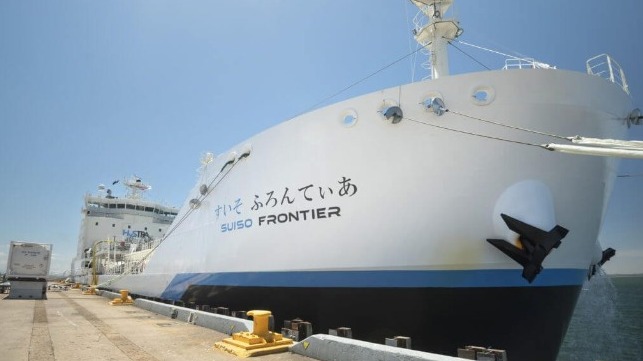
Countries around the world are adopting greenhouse gas (GHG) emissions targets of zero emissions by 2050. The global marine shipping industry is also evaluating whether to increase the current International Maritime Organization agreed target of a 50 percent reduction by 2050 to a 100 percent reduction. Large international shipping companies such as Maersk, MSC and CMA CGM, have already committed to achieve carbon neutrality by 2050 or sooner.
Replacing the current fossil fuels used in ships – such as heavy fuel oil – with cleaner alternative fuels could provide solutions to the challenge of decarbonization and Clear Seas’ ongoing research on reducing GHGs from marine fuels provides some valuable insights.
Electrify the fuel
To find a path to zero-carbon marine shipping, the complete system from fuel production through to its consumption to propel the ship needs to be considered. Fortunately, years of innovation have made ships the most efficient form of transport worldwide, and allowed the development of the most fuel-efficient engines and propeller drives. Energy efficiency measures – such as using high tech sails – can help reduce the amount of fuel ships need, but the remaining energy needed to power ships has to come from somewhere. Could renewable electricity be used as a clean source of power?
Electrification holds great promise for reducing GHG emissions from a whole range of existing fossil fuel intensive processes in industry, home heating and vehicles. This is because renewable low-carbon electricity from wind and solar has fallen in cost to make it a plentiful and economically viable alternative.
But how do we get this cleaner electricity from the source to the ships? Batteries are a great option for short trips on vessels like ferries and pleasure boats, but for large-scale ocean transport they are too heavy and bulky to store the required energy. This is where alternative fuels come in. By converting electricity into fuels – so called e-fuels – there is a potential means to solve the problem of how to transport the electricity to the ships.
Hydrogen as a building block
The best way scientists and engineers have found to convert electricity into a fuel is through a process called electrolysis that splits water (H2O) into the hydrogen and oxygen it is made of by running electricity through it in an electrolyzer. Large amounts of electricity are required for this process – the entire daily average electricity consumed by a Canadian household would only make half a kilogram of hydrogen through electrolysis, with the equivalent energy content to drive a family car just 12 miles. But the result is hydrogen gas produced without any fossil fuels – referred to as “green” hydrogen.
Unfortunately, hydrogen alone is not a very good fuel for ships. Though hydrogen can be burned quite efficiently in the ship’s engine, refueling and storage onboard the ship presents a significant challenge. Hydrogen is a highly flammable, lighter than air gas and, even when pressurized into cylinders or liquified through a cooling process, it remains too bulky in the quantities required to replace regular marine fuel. Hydrogen storage tanks are also costly, heavy and energy intensive to fill.
Example of a hydrogen factory concept powered with renewable energy sources. The hydrogen plant to be built in Varennes, Quebec, will use hydroelectric power.
But all is not lost for alternative fuels. By combining the green hydrogen produced through electrolysis with other gases like nitrogen, carbon dioxide and oxygen, found in the atmosphere, simple compounds like ammonia, methanol and methane can be manufactured and more easily stored in ship fuel tanks in the quantities required. These chemical compounds can still be burned in existing ship engines if small modifications are made to their design and construction. But to make these synthetic alternative fuels out of hydrogen, sustainable sources of the other chemical elements are needed.
Ammonia fuel is a front runner but it’s toxic
Of the synthetic alternative fuels under consideration, manufacturing ammonia from green hydrogen is perhaps the easiest. The process is widely used today for fertilizer manufacturing and the only other element required for ammonia, chemical formula NH3, is nitrogen – and this is in plentiful supply in the air that surrounds us. The bad news is that separating the nitrogen from the air is an energy intensive process, as is the ammonia manufacture. Another challenge with ammonia is that if spilled, it can turn into a toxic vapour cloud that is deadly for humans and animals. So why is ammonia even considered? Its ease of manufacture on a vast industrial scale and our experience in safely transporting it in bulk on ships, trains and trucks for the fertilizer industry are good reasons to back ammonia in the alternative fuels race.
The ammonia molecule (formula NH3)
Burning ammonia in a ship engine has been proven to be possible, and although there are concerns regarding GHG emissions from the nitrous oxides produced in its exhaust as well as the smog-producing nitrogen oxides (NOx), these look like they can be managed. Ammonia gas can be turned into liquid for transportation and storage by chilling it to a relatively modest -27 degrees F.
Methane fuel draws on fossil fuel experience
Synthetic e-methane has an advantage over ammonia in that its fossil precursor has already been widely used as a ship fuel in the form of liquefied natural gas. This means that we already have processes, standards and regulations for the safe design and operation of ships using methane as a fuel. However, one major drawback of synthetic methane is that, like the prime component of fossil natural gas, it is itself a greenhouse gas. Though relatively short lived compared to carbon dioxide, its unintended release would need to be vigilantly prevented in a similar way to other synthetic GHGs like refrigerants.
The second disadvantage is one that it shares with methanol: manufacturing methane (chemical formula CH4) requires the addition of carbon represented by C in the formula. Although carbon in the form of carbon dioxide emissions from fossil fuel combustion surrounds us, capturing it and using this source of carbon does not produce zero GHG fuel because the carbon originates from a fossil source.
Instead, manufacturers of zero GHG methane need to either capture carbon dioxide (CO2) from the combustion of plant matter, for example at pulp mills or wood-fired power plants, or capture it directly from the atmosphere.
The supply of carbon dioxide from biological sources like wood that captured the carbon dioxide from the atmosphere through natural processes is limited, so long-term solutions for zero GHG marine fuels would need to rely on so-called direct air capture methods that chemically extract carbon dioxide from the atmosphere. It remains to be seen if the cost of carbon captured this way can be decreased low enough through scaling up of these processes to make synthetic fuels containing direct air captured carbon dioxide.
The methane molecule (formula CH4)
Methane’s main advantage over other synthetic fuels is that it can be used in existing LNG-fuelled ships without modification and can utilize the existing and growing infrastructure built for the transportation of fossil fuels. The same infrastructure and fuel tanks could potentially also be used to store ammonia, even though its storage temperature of -27 F is not nearly as low as the -260 F that is required for LNG. Ammonia has a higher density than liquefied methane, so this would also need to be factored in to designs of LNG fuel infrastructure.
Methanol fuel is a complex but easier to manage alternative
Methanol, while still toxic, would be easier to manage than both ammonia and methane because it is a liquid at room temperature. There is significant experience safely transporting it in bulk on ships for the global chemical trade and burning it in an engine seems to present few problems.
Methanex Corp., of Vancouver, B.C., operates the largest fleet of methanol tankers in the world, a growing proportion of which are now equipped with methanol burning engines. Unfortunately, the methanol burned in these engines is produced from fossil natural gas, and Clear Seas research has revealed that more GHG emissions come from this fossil methanol than from existing fossil fuels produced from oil.
But the fossil methanol production infrastructure also presents an opportunity. Usually, industrial methanol is produced using hydrogen made by splitting fossil natural gas in a steam methane reformer. The first step in producing zero GHG methanol is to substitute the hydrogen from fossil natural gas with green hydrogen produced from electrolysis. Unfortunately, like methane, methanol also requires a source of carbon because its chemical formula (CH3OH) contains a C for carbon. Like e-methane, direct air capture of atmospheric carbon dioxide would once again need to be deployed to manufacture e-methanol.
The methanol molecule (formula CH3OH)
The challenge of scaling up green hydrogen production from electrolysis
Ammonia, methane, and methanol rely on a plentiful supply of green hydrogen from electrolysis. This is the crucial and potentially weakest link in the chain. Plans are starting to be put into effect to develop a network of green hydrogen production facilities and Canada’s low-carbon electricity grid supplied through hydroelectric power makes it an attractive location. Varennes, Que., will be the site of one of the world’s largest green hydrogen facilities. Costing $200 million, the plant will consume 88 megawatts of electricity and produce 11,000 tonnes of hydrogen annually. But this only equates to enough energy to supply just over half the fuel needed for a single large container ship with pure hydrogen.
Clearly, it’s not economically viable or practical for each ship to have two $200 million fuel production facilities supplying it. Advances in electrolysis technology will be required to improve the output, but fundamental limitations created by the chemical energy required to split water molecules make this a challenge – a maximum of just 26 grams of hydrogen for every kilowatt hour of electricity consumed. So, if the Varennes plant could be made 100 percent efficient and ran 24 hours a day, its output would only increase to 20,000 tonnes of hydrogen per year, enough for one container ship. Making the synthetic ammonia, methanol or methane with the hydrogen does make it go a little further, but making enough green hydrogen to decarbonize the global marine shipping industry remains a significant challenge.
Could hydrogen from fossil natural gas bridge the gap?
Hydrogen for the petrochemical industry is usually produced by heating fossil natural gas in the presence of steam – so called steam methane reforming. Could this be used to substitute for the green hydrogen until electrolysis technology is improved? Clear Seas research indicates that hydrogen produced through this method emits more GHGs than conventional marine fuel produced from oil. It should not be considered as an alternative.
Carbon capture and sequestration is often proposed to fix this problem of excessive carbon dioxide emissions created when hydrogen is produced from natural gas. Canada is the site of one of the largest carbon capture and sequestration plants in the world. Shell Canada’s Quest facility near Edmonton, Alberta cost $1.35 billion and can capture and store just over 1 million tonnes of carbon dioxide per year in underground caverns. This may sound like a lot of carbon dioxide, but in reality, it equates to the annual carbon dioxide emissions of just five large container ships.
Although Shell plans to expand the capacity for carbon dioxide capture and sequestration to almost 10 times the Quest facility, these projects are primarily designed to deal with the emissions from Shell’s gas processing and oil refineries and could never cope with the emissions from large-scale hydrogen production for marine fuel. And even if capture and sequestration could be scaled up, there is uncertainty in the scientific community about the ability of the underground rock formations to sequester carbon dioxide without it leaking out over time.
Canadian renewable energy company Ekona Power Inc., of Burnaby, B.C., is piloting an alternative technology called pyrolysis that splits the methane in natural gas into hydrogen and carbon dust. This carbon dust could be more easily managed and disposed of than carbon dioxide gas, but the technology is still at a very early stage of development.
How about biofuels?
Biofuel versions of both methane and methanol can be produced from any organic material. Plants are where most organic material comes from, and they capture carbon dioxide from the atmosphere as they grow, so when they are turned into fuel to be burned it is considered carbon neutral.
Bio-methanol can be produced by heating wood chips until they produce a gas and then cleaning and purifying that gas to create the final product. Methanol is also produced in wood pulp mills as a by-product of the pulping process, but this is usually burned by the pulp mills to generate energy. In theory, these sources of bio-methanol could be directed to providing ship fuel. But global production of bio-methanol is currently extremely limited and is estimated at only 0.2 million tonnes per year by the International Renewable Energy Association. This would only be enough fuel for fewer than two large container ships.
Bio-methane is more common than bio-methanol, and the Canadian Biogas Association calculates that six petajoules of gas is currently produced at 280 sites across Canada alone. These include digesters of animal waste as well as gas captured from landfills and sewage treatment works. For context, six petajoules is only enough gas to fuel two or three large container ships.
These two examples illustrate the immense scale of the challenge to provide biofuels for use in the marine shipping industry. With increasing demand for net-zero emission fuels, competition for the organic raw materials for fuel production will only intensify. Dedicated sources of organic matter for fuels like genetically engineered algae have failed to deliver, and concerns about the local ecological and climate change impacts of land-use changes from new vegetation plantations make these options less and less viable. Though biofuels might play a role in the transition to zero GHG marine fuels, it will likely only be a limited one.
More work is needed to achieve zero greenhouse gas emissions from marine fuels
Considering the full energy system from fuel production through to energy use on the ship, ship technology is not necessarily the weak link in the chain. Solutions for fuel tanks and engines that can store and burn zero GHG emissions alternative fuels are ready now or have development programs well underway. Retrofitting the large 2-stroke engines predominately used in ocean-going ships to allow them to burn any combination of alternative fuels looks to be relatively easily accomplished, and ship designers are responding to the challenge of modularization of fuel storage to allow methane, ammonia or methanol tanks to be installed in existing ships.
The critical gaps seem to be upstream in the fuel production part of the value chain, and the large-scale production of green hydrogen from electrolysis. Current solutions will need significant advances to scale up to the volumes of production needed. If methane or methanol are to be used, then major advances in direct air capture of carbon dioxide will also be needed to provide the other raw materials for the fuel. Biofuels can help in the interim, but only a tiny amount and they don’t present a solution for the full-scale decarbonization of marine shipping.
It appears that extending our reliance on fossil fuels with carbon capture and sequestration of either carbon dioxide or solid carbon may need to be considered as a least bad interim option, but extreme caution is needed to guard against unintentionally bringing higher carbon intensity fuels into the value chain in the pursuit of the zero GHG emissions marine fuel dream that may never be truly realized.
Although synthesized alternative fuels provide a potential pathway to zero GHG marine shipping by 2050, it is still a narrow and treacherous one, and there is certainly scope for innovation and more radical solutions to help open the way to a truly fossil fuel free future.
Paul Blomerus is the Executive Director of Clear Seas and an internationally-experienced researcher and leader in innovation with a proven track record in industry and university research management. He holds a Ph. D. in Engineering Science from the University of Oxford, England, and a Mechanical Engineering degree with first-class honors from the University of Cape Town, in South Africa.
This article appears courtesy of Clear Seas and may be found in its original form here.
The opinions expressed herein are the author's and not necessarily those of The Maritime Executive.