Syncrolift® Makes Dynamic Launching a Thing of the Past
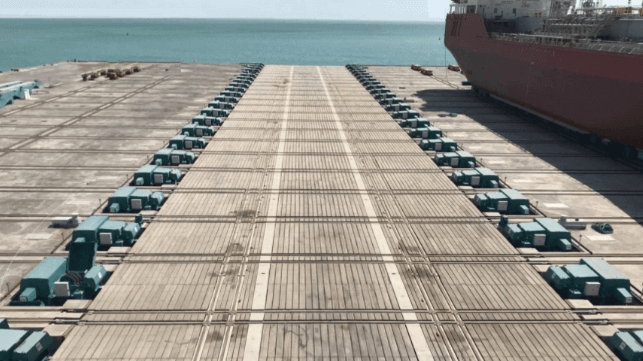
[By Geoff Stokoe]
In 1862 the USS Monitor was lifted on a mechanical lift for repairs after the Battle of Hampton Roads. Elsewhere there are other records of mechanical docks in India and Malta in 1872 and 1873, respectively. These were all substantial structures and “one-offs” which would be very costly by today’s standards.
In the last 70 years. there have been significant changes in the development of mechanical lift-docks – the most significant of which are platform structure, and the use of an adjacent transfer system.
The first Syncrolift® - was installed in 1957 at Bertram Yacht in Miami, FL. It was the first to control the synchronization of its lifting media simply and effectively. Primarily a marketing man, the Inventor sold 134 (mostly smaller) units, in the 22 years which followed Bertram.
Wanting to see his concept survive, and realizing a “mom and pop” business was too small to survive product liability damages, he sold in 1979 to one of his suppliers - a British company NEI which was then merged with Rolls-Royce in 1988.
Recognizing the strength of the eponymous brand, the company name was changed to Syncrolift® Inc. by Rolls-Royce North America. After subsequent changes in ownership, the company became a part of the Norwegian Nekkar Group as Syncrolift® AS in 2018. Today it is still the OEM for every one of the 283 Syncrolift®s which have been contracted since 1957.
The early years had left little time for innovation. The new ownership provided financial, engineering strength and organizational stability and Syncrolift® Inc. quickly matured and its products grew in size and application. A record-setter in 1983 was at Todd Shipyard in San Pedro CA having 110 240-ton hoists and a lifting capacity of 20,000 tons. In the early 90’s the British Vanguard Class of nuclear boomers were launched and serviced at Barrow and Faslane in the U,K. on Syncrolifts rated in excess of 28,000 tons.
The original design concept was innovative at the time in that synchronization was achieved using synchronous reluctance motors which all move at exactly the same speed. This required the platform to be articulated to prevent peak loads at individual lifting points.
However, an articulated platform is more likely to fail than a rigid platform if maintenance is neglected or if the platform is overloaded. An articulated platform is by definition made up of loose sections. If one wire rope breaks one or more adjacent sections will fall apart into the water and maybe even lose the ship being lifted. As installed lifts become older, any reduction in maintenance can become critical. Today’s Syncrolift® control system varies individual motor speeds to keep the platform level so that it is possible to make the platform rigid. Now, if a wire rope breaks the rigid platform absorbs the released energy and keeps the ship safe.
For many years now every new Syncrolift® has been designed in accordance with Lloyds Code for Lifting Appliances in a Marine Environment (CLAME) , MIL-STD 1625 and other relevant codes including UK’s Nuclear Safety Directorate. The number of new Syncrolift®s has grown to the point where 80% of the world’s mechanical lifts are Syncrolifts®. A list of the 20 largest units is listed below.
Nuclear Submarine construction has been revolutionized in the process. In Admiral Rickover’s day a steel tube was slid down a slipway and workers had to find ways to install the numerous operating components. Internal access to the “guts’ of a submarine was very difficult. For example, no scaffolding was available which meant welders were required to do up-hand welding while lying on their backs.
Today “boomers” are built, launched, or serviced using modern Syncrolift® transfer systems in Maine, Connecticut, Virginia, England, and Scotland. Thanks to the Syncrolift® Fluid Bed Transfer Systems, submarine hulls are built in open cylindrical sections fully scaffolded for ease of access. Almost the last things builders do today is to join the sections together, like chopping salami in reverse. The transfer bogies work as manipulators in the joining process.
Almost anything is possible provided there is the space on shore to do it. Modern transfer systems make it possible to provide major reductions in civil costs by absorbing the peak loads which any vessel could experience while moving onshore. Reductions of peak loads by up to 50% are possible.
In addition to serving multiple berths, adjacent transfer systems can also be used to modify a ship’s hull and even change a ship’s function in a very short time. For example, a ferry can become a casino ship in a matter of weeks. Hulls can therefore be off-hire for a fraction of the time it would have taken in other types of drydock.
More recently, modern control systems have come into play obviating the need for synchronous reluctance motors which are both expensive and energy hungry. The use of modern load monitoring systems has given the Dockmaster much more knowledge about the type of vessel he is trying to lift. It has also made him much more capable and given the ability to safely maintain his ward in her berth onshore.
On his monitor the Dockmaster can now easily see:
- Changes in a ship’s center of gravity,
- How she is sitting properly on her blocks
- If she is evenly loaded
- If she has high block loads at any point
- If a tank floods when entering the water.
The operation will stop automatically stopped any time there is a potential for damage to hull, weapons, sensors, or cargo. Submerged conditions for submarines can be simulated so the Exec knows which tanks to flood when she dives for the first time. Previously this was very much an iterative process done after launching
Nekkar emerged from TTS which had pioneered the Syncrolift® Fluid Bed Transfer System around the world. The parallel development of lift plus transfer systems is what has made Syncrolift® the drydock of the future. Multiple ships or ship sections can be serviced by just one lift. The record is 40 berths serviced by one lift with an adjacent larger lift servicing 12 berths and linked by a common transfer system. 2 into 52 really does go – up on one lift and down on another. Another installation achieves 400 dockings in a year handling ships up to 10,000 dwt with just one lift.
The Fluid Bed Transfer System has been very successful in industry because, in addition to supporting the ship on the equivalent to a floating mattress, the loads transferred to the ground are much reduced. For example, the peak loads applied by an Arleigh Burke Class destroyer can be reduced by up to 40%. This makes for massive saving I the cost of new civil construction.
Launching a ship from a slipway is a risky business and many a Naval Architect has had his heart in his mouth as his charge slid backwards down a slipway with champagne dripping from its bow. Side launching is even more risky and alarming.
At a conference of the Royal Institution of Naval Architects in 2003, the Chief Executive of the UK Warship Support Agency declared the British Navy had undertaken it’s last dynamic launch. He did so in the knowledge of just how safe launching on a Syncrolift® can be. The combination of intelligent lifting and transfer system engineering is what makes the eponymous Syncrolift®, the safest drydocking process of all.
70 years later, it’s not so exciting as a dynamic launch, but a whole lot safer!
Geoff Stokoe is Vice President Shipyard Development at Syncrolift Inc.
# | Name | Capacity - Tons | OEM |
1 | ASC India | 23250 | Syncrolift AS |
2 | King Salman, Saudi Arabia | 26000 | Chinese Corp |
3 | Mers El Kebir | 15295 | Syncrolift AS |
4 | Indian Navy Vizag | 33650 | Syncrolift AS |
5 | ABG, India | 30000 | Syncrolift AS |
6 | Turkmenbashi Port | 14400 | Syncrolift AS |
7 | Casablanca Port | 11685 | Syncrolift AS |
8 | X52 Naval Base | 10000 | Syncrolift AS |
9 | NOSCO, Viet Nam | 30000 | Syncrolift AS |
10 | Port Adelaide | 16000 | Syncrolift AS |
11 | Venice Barrier | 25200 | Syncrolift AS |
12 | Indian Navy Karwar | 14875 | Syncrolift AS |
13 | Vokswerft Stralsund | 18000 | Syncrolift AS |
14 | MMHE Johore Malaysia** | 23320 | Syncrolift AS |
15 | MOD(N) Faslane | 28000 | Syncrolift AS |
16 | Royal Iranian Navy | 16800 | Syncrolift AS |
17 | BAE Systems Barrow | 23300 | Syncrolift AS |
18 | Todd Shipyard** | 21100 | Syncrolift AS |
19 | Tandanor | 16000 | Syncrolift AS |
20 | Astican | 12490 | Syncrolift AS |
** Relocated to Malaysia and upgraded
The products and services herein described in this press release are not endorsed by The Maritime Executive.