Stainless Steel Critical for the Reliability of Marine Scrubbers
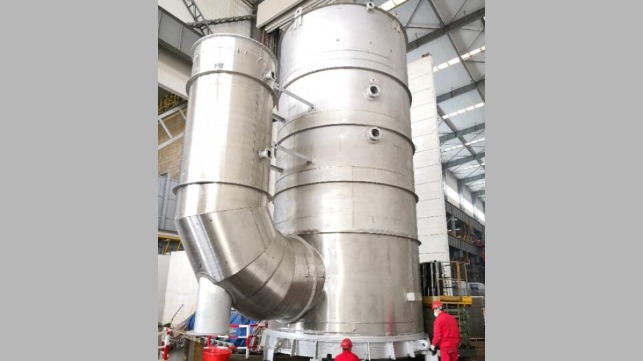
Björn Helmersson, a corrosion specialist with Outokumpu, explains why stainless steels are vital to withstand the aggressive corrosion conditions found in marine scrubber units.
Merchant sailing vessels are relying increasingly on their marine scrubber units (known otherwise as exhaust gas cleaning systems or EGCs) to meet increasingly stringent environmental legislation. Inside a scrubber the operating conditions are very harsh, thanks to the combination of acids, elevated temperatures and a high chloride content in the wash water. For reliability and a long service life it is essential to choose the very highest quality construction material, which is typically high-alloyed stainless steels.
Material selection can be challenging due to the wide range of alloys available and the varying conditions in different scrubbers. Using a construction material that cannot survive the conditions will result in poor reliability. Equally, commercial considerations mean that it is important not to over-specify. That is why we have worked to support Outolumpu’s years of practical experience in marine scrubbers with extensive field and laboratory testing.
Scrubbers fall into three main types
Wet scrubbers are used generally by the shipping industry (see Figure 1). They wash the exhaust gas stream by forcing it into contact with water to remove the sulfur dioxide (SO2), a toxic gas that is directly harmful to human health. Scrubbers units feature three main design:
Open-loop: This uses seawater to scrub the exhaust gas to remove SO2. The wash water is then treated and discharged back to sea.
Closed-loop: Fresh water is used in a closed circuit that is treated with an alkaline chemical such as caustic soda.
Hybrid: This can be used in either open- or closed-loop mode according to operational needs.
Figure 1 – Open-Loop EGC system (credit: Exhaust Gas Cleaning Association).
Different service conditions mean different corrosion risks
Marine scrubbers experience three main types of corrosion risk: pitting corrosion, crevice corrosion and uniform corrosion. Where they appear depends on the service conditions in the scrubber. At the inlet, where the uncleaned gas meets the wash water, there is a mix of wet and dry conditions, with condensing acids from gas and chloride-rich wash water and elevated temperatures. These conditions are very aggressive with a risk of uniform and pitting corrosion.
In contrast, within the scrubber body there is a slightly acidic wash water combined with a lower temperature than the inlet. The main risk here is pitting corrosion. Similar conditions apply for other parts of the scrubber system, such as packing material, demisters, tubing and spray nozzles
Crevice corrosion may occur in areas where two surfaces are in close contact, such as flanges, packing material and under deposits.
Field testing is vital to match material and application
Outokumpu supplies stainless steel used to construct around 60% of the marine scrubbers installed every year. We are engaged in extensive R&D activities to support this business. This includes laboratory testing designed to simulate the aggressive conditions found in scrubbers. However, the most informative experimental work is long-term field testing carried out in cooperation with marine scrubber OEMs and their customers. The results of our test program have shown that material selection must always be done on a case by case basis.
For the scrubber body, Ultra 254 SMO is one of the most widely used grades. This is a 6% molybdenum and nitrogen-alloyed austenitic stainless steel with extremely high resistance to both uniform and localized corrosion.
However, in some cases it is possible to use a 25Cr super duplex stainless steel such as Forta SDX 2507. This offers similar corrosion resistance to Ultra 254 SMO and improved mechanical strength.
Standard 22Cr duplex stainless steel can also be used successfully in less aggressive applications such as closed-loop designs and some parts of open-loop scrubbers. A typical example is Forta DX 2205, which is the most popular duplex product on the market. It offers very good resistance to uniform and localized corrosion and stress corrosion cracking in combination with high mechanical strength.
For the scrubber inlet, our test program has established that Ultra 654 SMO offers a viable, cost-effective solution. This is a 7% molybdenum and very high nitrogen-alloyed austenitic grade that is the most corrosion resistant stainless steel in the world.
Practical examples
Ecospray Technologies S.r.l. Italy (Figure 2) needed a highly corrosion resistant material for exhaust gas cleaning scrubbers. Ultra 254 SMO proved to be the best combination of performance, price and dimensions.
Figure 2 – Ecospray Technologies scrubber in Ultra 254 SMO.
ContiOcean Environment Tech Co., Ltd. delivers open-loop scrubbers to cargo ships of various size classes. Forta SDX 2507 provides the necessary corrosion resistance for the harsh conditions in the scrubber body (see Figure 3).
Figure 3 – Open-loop marine scrubber manufactured by ContiOcean Environment Tech Co., Ltd in super duplex stainless steel
The products and services herein described in this press release are not endorsed by The Maritime Executive.