Smart Containers: Value Add Gain Efficiencies
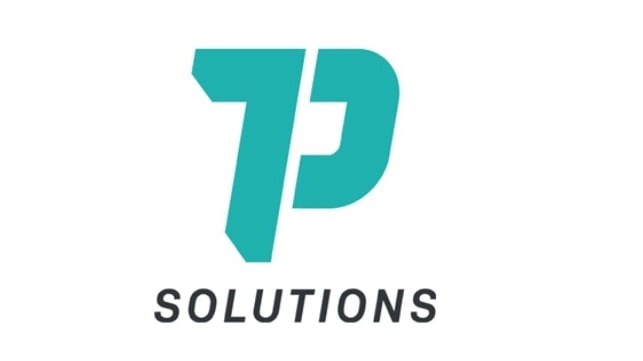
Using technology within the global and maritime supply chain is not new to the industry, yet at the same time we must ask ourselves, how effectively is technology used? I began my career in global transportation in 1978 and have witnessed many changes from typewriters and dumb terminals to online technology and IoT used today. However, when entering the office of a global transportation company today the environment and the desk remain much the same as they did decades ago - file folders representing clients and agents on the telephone tracking shipments.
Throughout the years we learned to utilize technology as a competitive advantage; automating processes on behalf of export and import customers. In the mid-90’s we saw enhancements through the use of Electronic Data Interchange (EDI) and other data integrations to streamline the processing of moving commercial invoices and other documents electronically - facilitating export and import. Even with these advancements, we continued to battle the challenges of visibility. Decisions are reactive when events have already taken place. In 2003 we had the opportunity to start a company that would manage, store, and build libraries of patient samples and drugs from pharma and biotech clinical trials. There was a need for better visibility to protect the important research of these irreplaceable samples. In 2007 we began to design a “purpose-built trailer” to move and protect large amounts of expensive and irreplaceable research. The trailer went into service in 2010 and gave us access to real-time information.
As a result of these experiences, and understanding the needs of the industry, 7PSolutions provided real-time information and added value to the supply chain. We quickly understood that what we had developed raised the standards within the GPS service provider industry - using real-time GPS solutions with a transportation management and a data analytical platform. Interest for our business came from all directions, including retailers, transportation companies, law enforcement and pharmaceutical companies. Providing real-time visibility to their individual shipments, regardless of the mode of transportation became a reality – including maritime shipping.
The challenge we faced was who would pay for this service? The shipper? The carrier? The service provider? Today all stakeholders within the supply chain recognize the importance of real-time visibility and has become easier as GPS platforms are device diagnostic. Having the ability to point a GPS device to our servers is fairly simple. However, we believe device diagnostic situations can lead to providers NOT fully utilizing the device capabilities. During the 2019 IoT Worldwide conference in LA, we learned from several GPS device manufactures that less than 40% of the device capabilities are used by GPS providers today – why? Cost and developer experience.
One of our first adopters was a manufacturer of a climate-controlled shipping container, fully equipped with two-way communication and visibility. The ability to manage temperature remotely, set-points, equipment diagnostics add value for all stakeholders – proactive decision making and increased productivity. Since then, we have our telematics now in 3 containers and working with others.
We still don’t understand why this technology is not installed and included in all climate-controlled ocean containers? Why has the bar not been raised for marine executives? I see bits and pieces of news as the maritime industry attempts to add this visibility, which at times seems like sticking your toe in the water before getting in. The industry does not know what it does not know, meaning as we did in other industries we must educate container manufacturers and steamship lines what they should expect with real-time GPS technologies, not what is being sold.
Utilization of GPS providers who use 100% of the device capabilities have experienced value in smart containers, including maritime telematics have the ability to change the industry almost overnight. Because these technologies do exist today, entry to market is cost-effective and development is limited only to creating the communications of the containers refrigeration units with the real-time device.
The efficiencies gained far exceed the cost of implementation and ongoing cost. Every stakeholder now has real-time data at their fingertips and can manage by exception. Shippers receiving automated event-based communications, departures, transit points, arrivals, and deliveries. Event-based communications regarding the condition of product, live, and historical data. Steamship lines have the ability to create demurrage invoices in real-time, container inventory management, maintenance schedules, and drayage companies managing container pools, deliveries and storage charges.
Why then do we not see this as the industry standard? Marine executives have a chance to improve logistics with some simple changes. The technology and platform exist, exploratory programs and recreating the wheel adds cost to market entry and prolongs the utilization of real-time visibility to all stakeholders. Let’s keep it simple.
What are your next steps? What is your real-time visibility plan? Are you implementing a competitive advantage?
7PSolutions was founded in 2010 to fulfill an unmet need in the supply chain and transportation industries: a single solution for climate control, security, fleet management and quality management through every stage of the supply chain. We leverage the extensive knowledge, experience and expertise of our leadership team comprised of logistics, cargo security, cold chain and quality assurance industry veterans – all of whom understand the critical importance of providing real-time supply chain visibility so our clients can manage their supply chain, fleets and assets. Today our real-time GPS solutions combined with our RouteWatch SaaS are utilized globally to ensure product integrity and protect our customers Brand.
About Jeff Clark
Jeff Clark is Founder and CEO of 7PSolutions, starting the company in April of 2010 to enhance the pharmaceutical supply chain and improve patient safety. Using his extensive background in transportation and the life science industry his vision was to combine a GMP quality management system with technology, providing training and tools to the supply chain allowing for real-time visibility and faster decision making.
Prior to starting 7PSolutions, Clark held management positions within the global transportation industry with a focus of combining global transportation with unique software technologies to enhance processes and data flows. Other expertise includes Good Manufacturing Practices, Good Distribution Practices, Food Safety and Dangerous Goods transported by air and ground globally.
The products and services herein described in this press release are not endorsed by The Maritime Executive.