Low-Labor Cost vs Productivity in Ship Management
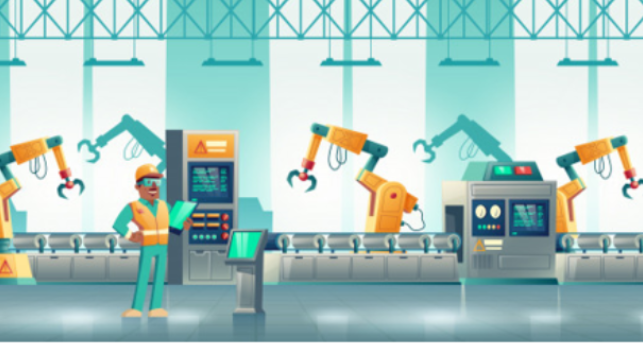
I have talked in previous articles about the fact that Ship Management has become a very commoditized service where the cut-throat competition makes it increasingly harder to grow steadily, stay profitable & sustainable, and provide high-quality services. All these sound like a lot for companies that must work hyper-hard to keep themselves in business.
What these companies do is heroic. Sadly though, heroism was a good trait for companies of the past but is no longer the key to success in a digital world.
How can they use technology to become more adept in a digital economy?
In business, all players have two parts of the equation to make a profit: to generate revenue and to avoid spending:
1. Generate revenue
- Create value and/or
- Add value
2. Avoid spending
- Cut labor costs and/or
- Increase productivity
In today’s article I will dedicate my attention to the second part of the equation: to avoid spending.
Cutting labor costs vs Increasing Productivity
Many Ship Management companies decide to relocate certain departments, or the entire organization, to low-cost-labor countries to keep their profits healthy. Indeed, some companies have already left Singapore for India.
Nevertheless, I think that move is similar to acquire a huge loan at a very high rate of interest but with low monthly installments. In the long run, the technical debt will be huge on the company's balance sheet. In today's world to seek low-labor relocation strategies to stay in business is shooting yourself in the foot. You will enjoy for a while a good profit, but you will not do the required investments in digital technologies, or any other, that allow you to increase your productivity. It’s a trap.
For Ship Management companies in Singapore and Europe, is paramount to invest in Digital Technologies to increase the productivity of their teams. That is to say that the same amount of staff can handle more vessels without working longer hours, or for those less ambitious, that one can keep the same number of vessels with less staff.
How to increase productivity with Digital Technologies?
First, it is required to understand that work is work and always will be. What I mean by that is, that work cannot be destroyed, only transformed. Even if you automate processes, the work is still done, not manually but by a machine or robot. Just let the robot stop and you will see what I mean.
One of the most difficult concepts for non-Tech people to understand in Robotic Process Automation (RPA) is where the work goes. I like to explain this with an analogy:
Let’s imagine that you have a production line for physical products. Initially, you have 4 employees with 4 steps on the assembly of the product. Eventually, you automate the 4 steps with robots, but the product is still the same product and the steps are still the same.
It seems self-explanatory, but you need to revisit what is logic to understand what is less obvious. Now, the same goes for an office job, there are different people involved doing different tasks. Eventually, those tasks get automated, in turn, you free the people for higher-value work, but the robots -invisibly - continue doing the job that was done before by a human. By the way, robots are way faster than us.
I wanted to explain this at length because one of the most common mistakes in RPA is that Operations believe that this is now an IT issue. That is deadly wrong. Work never gets destroyed, just transformed. Of any digital tools that help an employee or a team, that person or group of people are still accountable for its success and must report accordingly. Needless to mention, this should be part of their Job Description. IT is responsible for keeping tools up and running, and for making the organization data-driven, but the success of the operation is still under the Technical Team. The fact that you have fewer people under you does not mean that you are less responsible and accountable for the operations; instead of humans, you have machines.
I like to use another analogy to make it even clearer. In the 2nd Industrial revolution, electricity made almost all tasks more efficient and hence you required Electrical Engineers that were not required before. That is the same for the 4th Industrial Revolution, your electricity now is called data and you need IT to keep that data available at any given time. Having a tool or system down might be comparable to having a blackout in a section of your company.
Now that we all understand how work can be transformed by RPA, the mission is to map out from end to end all the processes of the company and identify where the bottlenecks or inefficiencies are. You need to identify areas that are:
1. Overstaffed* and underperforming**
2. Overstaffed but performing
3. Balanced but underperforming
4. Balanced and performing
*Overstaffed: you should have a capacity based on the number of vessels per function, but not follow blindly industry standards as average numbers hide mediocre operations from other companies. A company should have an optimum target for each function.
**Underperforming simply means, your staff needs to work long hours to deliver, and/or quality is not predictable.
If your thorough analysis shows that more than 50% of your processes are under 1 and 2, please consider changing your core system with a new one that comes with the latest technology. You needn’t more complexity in your systems. On the other hand, if your processes are below 50% under 3 and 4, look for automation solutions. This is only a guideline.
For both cases, Process Re-engineering is a must, as many processes were developed based on the available technology decades ago. You will reap huge benefits by doing so. Sadly, I have seen broken processes with expensive robots.
As the popular adage goes, if you don’t measure it, you can’t manage it. In a nutshell, you now understand why is important Data Visualization, Business Intelligence, and later Advanced Analytics. It is purely business, nothing to do with technology. If you don’t measure it, you can’t do anything of what I mentioned above.
The end goal of increasing productivity is to produce more value in the same amount of time and to reduce the total cost of work. If you go for the low-labor-cost strategy you will never be able to produce more value in the same unit of time, although you can reduce the total cost of work.
Do you want more productivity or lower labor cost?
Some people will say both, but let’s not fool ourselves. The increase of productivity with technology in a developed country is not given exclusively by the technology we implement. Productivity is the outcome of the amalgamation of technology deployment and the other industry services that the country renders: ease of doing business, efficiency, transparency, advanced infrastructure, etc.
Let’s make productivity increase a serious goal for Ship Management.
The products and services herein described in this press release are not endorsed by The Maritime Executive.