Ecospeed Coatings Chemical Resistance
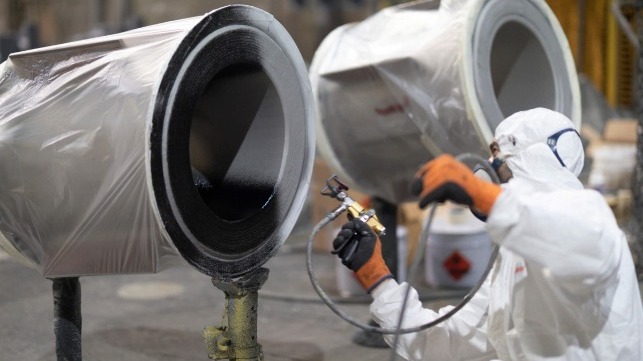
[By: Subsea Industries]
When Ecospeed coatings were being developed, Subsea Industries simply searched for the best protective coating for marine applications, period. This logically led to the type of thick, highly corrosion resistant vinyl ester coatings that are used to protect tanks. This type of coating is also highly corrosion resistant to many chemicals including acids and salt water. Glass was added into the mix to provide the toughest and most durable coating possible. Ecospeed coatings were born.
This added feature of being highly resistant to chemical corrosion only became apparent some time later. This made Ecospeed suitable for many applications where conventional marine coatings would be removed by corrosive chemicals.
The importance of chemical corrosion resistance
If steel is poorly protected with coatings that are not capable of resisting the chemicals they are exposed to, the paint will quickly be removed by the corrosive chemicals and the underlying steel will be subject to general corrosion, especially in a marine environment. Salt water is highly corrosive to unprotected mild steel.
Exhaust Gas Cleaning Systems (ECGS)
In 2008, the IMO accepted exhaust gas cleaning systems (EGCS), commonly referred to as “scrubbers,” as an alternative method for ships to comply with sulphur oxides (SOx) and particulate matter (PM) emission reduction regulations. By employing scrubber technology, ships can continue to burn heavy fuel rather than the much more expensive low sulfur fuel, and can thus save a considerable amount while still remaining compliant with IMO regulations. Thus, since the IMO decision, the use of scrubbers has become widespread.
However, the chemicals which are “scrubbed” out of the exhaust are highly acidic and corrosive. The pipes that are used to convey the wastewater into the sea, the recycle tanks which. form part of the system, the overboard pipes as well as the entire hull area of the ship around the scrubber overboard all come under attack from highly corrosive chemicals. The effects are rapid chemical corrosion. The hull paint is removed. The pipes start to corrode away to the point where there is a risk of water ingress into the engine room, endangering the ship.
When it comes to protecting steel from chemical corrosion, conventional hull coatings are not up to the task. The chemicals remove the traditional coatings such as antifouling and foul release very rapidly and the steel begins to corrode as a result The usual coatings used for scrubbers and the various parts of the scrubber systems do not adequately protect the steel. The result can be heavy corrosion damage which is not only very expensive and time-consuming to repair, but a safety hazard to ship and crew.
Repairs out of drydock
This came to the attention of Subsea Industries in 2016 when their sister company, Hydrex, was increasingly being called upon to perform emergency underwater repairs on ships employing scrubbers.
If an existing scrubber suffers corrosion damage, it is not too late to repair it. Hydrex regularly replaces scrubber overboard pipes. This is done on-site without the ship needing to go to drydock.
In all cases, the new pipes installed by Hydrex are protected with Ecospeed. If no welding needs to be carried out near the coated area, the new pipes are coated in advance. If this is not an option, Ecospeed is applied after the new pipe is installed and all welding completed.
Subsea Industries estimated that applying Ecospeed to the replacement pipe before it was welded into the hull and connected to the scrubber system would prevent a recurrence of the corrosion. Sure enough – once coated, the pipes are corrosion proof.
Preemptive use of Ecospeed
Many major shipowners and operators have found that coating the scrubber itself, the recycle tank, the overboard pipes and the area of the hull around the scrubber overboard with Ecospeed when the ship is in drydock or in the newbuild stage, protects the steel from the highly acidic scrubber exhaust effluents or other chemicals. This protection continues for the service life of the ship without the need to repaint. This helps avoid serious failures which can include leaks in the hull.
Ecospeed chemical corrosion protection in action
Following is a fairly recent dramatic case in point.
The image on the left below shows the typical state of a poorly-protected scrubber recycle tank when a ship comes into drydock routinely. In the case of this vessel, the recycle tank was repaired with welding and steel replacement and then the steel was grit blasted and Ecospeed was applied in two coats to a thickness of 1000 µm/40 mils.
What was not expected by those who had no prior experience to the results that can be attained with Ecospeed, was the excellent condition of the same recycle tank when the ship was again in drydock in China two years later.
The shipyard Paint Supervisor was shocked by the condition of the recycle tank coating. According to him he had never seen a coating in such good condition in a recycle tank as Ecospeed. “The coating is looking fresh after cleaning,” he said. “No hot work is required before painting, and only several touchups are needed, with minimal paint work.”
The project manager of Zhejiang Energy Marine Environmental Technology (ZEME) was “extremely satisfied with the performance of the coating,” he said that “Ecospeed offered the best acid and alkali resistance compared to other brands of paint I used in the past.”
Resistant to a wide range of chemicals and substances
It is not only the acid effluent of scrubber systems that Ecospeed is resistant to. The coating has been independently tested for chemical corrosion resistance.
In order to provide information on the impact of long term contact time on the integrity of cured Ecospeed coatings several substances including chemicals and fuels which ships typically carry were tested for their effect on the coating.
For tanker cargos, this included many types of oil and petroleum products including fuel oil, all types of diesel, jet fuel, all types of gasoline, naphtha, kerosene, lubricating oil and crude oil. Also caustic soda solution, molasses, palm oil and other frequently carried in tanks on ships.
For dry cargos, various metal ores were tested as well as salt, sugar, wood chips, coal, bauxite, salt as well as various grains were all tested.
The results of the tests were very positive, with no weakening, plasticizing or any other coating degradation observed with any of the substances tested.
Thus, the chemical corrosion protection applies not only to the scrubber system and related parts, but also to sewage tanks and other tanks that are subject to chemical corrosion.
Before Ecospeed was used for this purpose on ships, it was employed to protect the inside of pipes carrying hot gases with corrosive particles in a steel factory. The pipes were suffering from severe pitting from the chemical corrosion. After Ecospeed was applied, the corrosion and the pitting ceased.
General conclusions
To the general corrosion protection properties of the Ecospeed family of coatings (this family of coatings includes Ecospeed, Ecoshield, Ecolock) can be added their very high chemical corrosion resistance. This has been tested under very harsh conditions and proven effective.
The products and services herein described in this press release are not endorsed by The Maritime Executive.