X-Press Feeders Converts Methanol-Ready Ships on Delivery
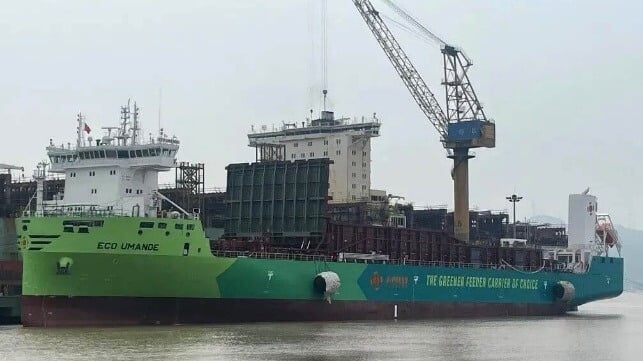
The pace of uptake for methanol-fueled operations is even surpassing the expectations of the industry from just a few years ago. X-Press Feeders which is preparing for the launch of a methanol-fueled feeder network in northern Europe this year has decided to convert several of its vessels from methanol-ready to methanol operations immediately.
The Eco Umande marked her handover to X-Press Feeder for the second time in months yesterday, June 23, and immediately began two days of sea trials with its new methanol propulsion systems. Chinese officials are calling the ship the first methanol conversion for the ship was built methanol-ready, but when delivered in March 2024, X-Press Feeders immediately sent it back into a shipyard before entering service to complete the methanol plant.
X-Press Feeders highlights that it is building 14 ships of similar design at several Chinese shipyards. The first, Eco Maestro (13,900 dwt) was built by Yangzijiang Shipbuilding Holdings and was handed over just about a month ago. She fueled last month in Singapore and is completing her delivery run due to reach Las Palmas on June 30.
The class of ships was designed by German naval architects TECHNOLOG Services and is 485 feet (148 meters) in length. They have a capacity of 1,170 TEUs. They were designed for the new MAN 5S5ME methanol engine and will have a speed of 14.5 knots. The ships were designed for efficiency including shaft generators, adjustable propellers, and suspended flap rudders.
The next vessel, Eco Umande was built by New Dayang Shipbuilding and delivered to the company in March. She however was immediately shifted to Zhoushan Pacific Offshore Engineering for conversion from methanol-ready to fully operational on methanol or green methanol.
The shipyard detailed a complex process for the conversion of the ship completing its methanol capabilities. The modifications involved the installation of seven systems, including the methanol fuel system, nitrogen system, methanol equipment room bilge water system, methanol tank ventilation and stripping system, LFSS instrument air system, and foam system. At the same time, eight systems required alterations, including the CO2 system, ship-wide air measurement system, engine room water supply system, high and low temperature fresh water-cooling system, compressed air system, control air system, fire water system, and ventilation system.
DNV has highlighted that methanol is quickly overtaking other options to become the system of choice for new orders. It reports there are 269 vessels currently on order for delivery over the next five years that will be outfitted for methanol operations.
X-Press Feeders has said that Eco Maestro would undergo further testing once reaching Europe before the next work launched in the third quarter. The 14 ships will be delivered through mid-2025, but Zhoushan Pacific reports it is already working on the second vessel outfitting converting the ship from methanol-ready to immediately capable. This second project is expected to be carried out in July 2024.
China’s Zhoushan Xinya Ship Repair Company is due to start the first total conversion in the coming weeks. Maersk contracted the yard to undertake the conversion of Maersk Halifax (178,257 dwt / 15,262 TEU) and the vessel is currently on its final run. She is due to reach Shanghai on July 10 and five days later arrive at the yard to begin the conversion of its traditional fuel plant for methanol operations. The project is expected to take about three months and will make the ship the first large, ocean-going containership retrofitted to methanol operations. Hapag working with Seaspan and CMA CGM have also contracted for some of the first conversions of in-service containerships to methanol while Stena has designated two of its ferries also for methanol conversions.