Wärtsilä and Maersk Develop Solution to Prevent Scrubber Corrosion
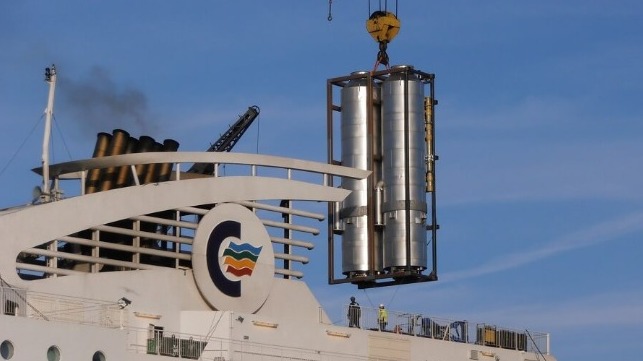
Scrubbers to treat exhaust emissions have been enjoying a resurgence as the shipping industry rushes to comply with the pending IMO sulfur regulations and the likelihood of EU and others regulating carbon emissions. While the number of scrubber installations is increasing, issues still exist with the technology, including a potential problem of corrosion due to the acidic nature of sulfur which can cause weathering to the discharge pipes, overboard pipes, and the scrubber system itself in an open-loop system.
To address the problem, technology company Wärtsilä has partnered with Maersk in developing a unique ”pipe in pipe” solution that is designed to prevent scrubber discharge pipe corrosion. The company, which is the leading manufacturer of exhaust gas scrubbers, reckons that the permanent in-pipe solution will help solve corrosion problems associated with open-loop scrubber washwater discharge. The solution will help the growing number of shipping companies installing exhaust gas cleaning systems addres the potential increase in maintenance, service, modifications and repairs costs of the system due to corrosion.
“We have noted corrosion incidents occurring on some scrubber equipped vessels and wanted to be proactive in solving the problem. Additionally, taking a vessel out of service is extremely costly,” said Jorn Kahle, Maersk Senior Lead Specialist.
Maersk, the world’s second largest shipping line by container capacity, is among companies that have invested heavily in scrubbers, installing the system aboard nearly 100 of its container vessels as part of its 2040 net zero ambitions.
Just recently, Bermuda-based independent bulk carrier Himalaya Shipping announced plans to install scrubbers on its entire fleet of 12 Newcastlemax dry bulk vessels under construction at New Times Shipyard in China. Similarly, tanker operator DHT Holdings also said it is investing $25 million to retrofit an additional eight vessels on its fleet with the system.
An analysis by intelligence firm Alphaliner shows that by the end of last year, almost a third of global container capacity, approximately 850 ships, were fitted with the gas cleaning system.
According to Wärtsilä, the majority of the estimated 5,000 scrubber systems installed across the global fleet are of open-loop configuration. With the system, seawater is used to scrub SOx from the exhaust gas, with the used water then being discharged back to the sea after cleaning.
Under IMO guidelines, the washwater from scrubbers, should have a pH of no less than 6.5. However, in reality the pH of scrubber washwater is typically acidic, prior to being diluted by seawater. This creates the risk of structural corrosion to the discharge pipes.
The risk is particularly high for pipes made of mild steel. In some cases, if the discharge pipes are inadequately protected, severe corrosion can damage the surrounding mild steel hull plates, resulting in water ingress.
The company contends that the new “pipe-in-pipe” solution allows for the original overboard pipe to remain in place while a new glass reinforced epoxy (GRE) pipe is inserted into it. No metal cutting or welding is necessary. A SMO steel sleeve is inserted between the new GRE pipe and the existing steel pipe. An adhesive permanently secures the GRE pipe in place. Since this solution has a small impact on the internal diameter of the pipe, it is best suited for overboard pipes with a diameter greater than 300 mm.
“This is a long-term solution that can be planned for at any time, even if corrosion has not yet occurred. The component pipes can be prepared and stored either on board or at an engineering facility ready for fitting either during a scheduled drydocking or port-call or, if necessary, whilst afloat and in operation using a cofferdam at a convenient time and location,” explained William Winters, Wärtsilä Underwater Services Managing Director.
The solution, which is intended for long-term protection of ocean going vessels by reducing complications associated with welding work required on pipes and sometimes hull plates, particularly in underwater repair situations, can be installed in less than two days thus preventing ships from having to go off hire.