Super Efficient Bulker Concept Meets CII While Using Conventional Fuels
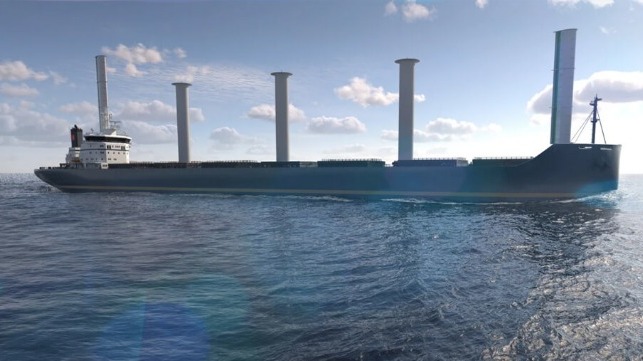
A new design study undertaken by Kongsberg Maritime and Deltamarin demonstrates that by using a combination of technologies it is possible to meet future emissions targets while using conventional fuels. The companies report by using a combination of technologies they were able to develop a “Super Efficient Bulker” offering shipowners the means to meet stringent future compliance targets without abandoning conventional fuels.
One of the concerns of many in the shipping industry is the availability and quantity of alternative fuels that will be required to support the transition for the maritime sector. According to the companies, this design offers an alternative that would also have a short payback period of five years making it a practical alternative.
"While low-carbon fuels are an option, many prefer to stick with conventional fuels,” said Oskar Levander, Vice President of Strategy and Business Development for Kongsberg Maritime. “Our goal was to design a vessel capable of complying with predicted CII regulations throughout its lifetime, using advanced energy-saving technologies.”
Kongsberg Maritime and Deltamarin selected a Kamsarmax bulker for the study because it is a popular and versatile vessel type. The 82,000 dwt bulker they report faces restrictions due to the concerns for the global availability of low-carbon fuels, making it an ideal candidate for the study.
The design concept incorporates wind-assisted propulsion, elements to reduce hydrodynamic resistance, and operational management. The result is a bulker that promises a fuel cost savings of 40 to 50 percent depending on the operational profile.
The approach to wind-assisted propulsion uses a combination of three tiltable rotor sails and two suction wing sails. According to the companies, this dual approach maximizes wind power utilization, adapting to varying wind conditions to ensure optimal performance.
Air lubrication is combined with a new hull shape to trap the air bubbles under the vessel (Kongsberg)
The hull form drastically reduces hydrodynamic resistance through a design that will trap bubbles, from an air lubrication system, underneath the vessel. This concept will maximize the effects of resistance reduction and the companies report a patent application has been filed to implement the concept.
“The inclined hull, with a 1-degree slope from bow to stern, and vertically turned bilge keels create 'walls' to keep bubbles in place, enhancing fuel savings,” explains Kongsberg.
The vessel's system also integrates a Hybrid Shaft Generator with frequency control, optimizing electrical power usage and reducing emissions, while supporting increased loads from wind-assist technologies and air lubrication compressors. It will further enhance overall efficiency.
Technology is used by equipping the vessel with an Intelligent Energy Management System (iEMS) and route optimization software, to ensure optimal energy use. Emphasizing the benefits of slow steaming, the vessel is designed to operate at a reduced speed, balancing fuel efficiency with operational viability. They explain that a 1-knot speed reduction contributes to substantial savings in fuel, emissions, and maintenance costs.
“This project has been a real eye-opener. The combination of advanced technologies creates significant savings, making our new design a game-changer,” said Levander. “The 'Super-Efficient Bulker' is a novel design and advanced operation will, according to Kongsberg Maritime’s analysis, reduce fuel costs by more than half compared to a state-of-the-art vessel equipped with only conventional technology.”