Shipowners Need to Prepare for Phaseout of Legacy Firefighting Foam
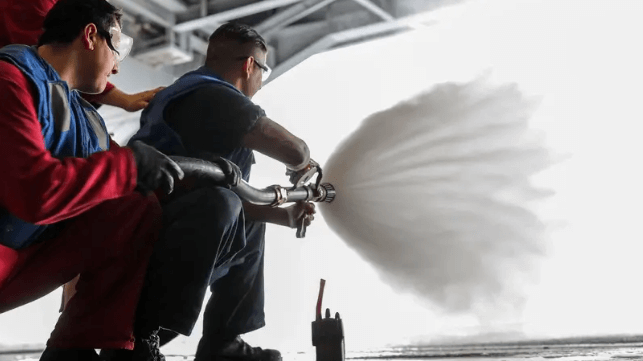
Dealing with PFOS and PFAS contamination from firefighting foam can be a pricey proposition, as the U.S. Navy has learned over the last few years. The Pentagon expects to spend about $5 billion to clean up sites used for training with fluoroalkyl-based aqueous film-forming foam (AFFF), and independent estimates suggest that the cost could grow by a factor of 10. The foam may have health effects on regular users, like professional firefighters, and it is rapidly being phased out across the armed forces. The same wind-down is happening in the civilian market, whether commercial shipowners are ready or not, according to the safety experts at Viking.
Viking says that the main issue for vessel operators is that petchem plants don't plan to make the "forever chemical" ingredients for conventional AFFF anymore. For example, chemical giant 3M - a market leader in PFOS and PFAS, and an early target of litigation - has announced plans to get out of manufacturing the substances altogether by the end of next year.
"Shipping is only a minor consumer of these products, and what is becoming clear is that rather than legislation, the driver for transition to different types of firefighting foams has quickly become OEMs stopping production," says William Gielen, Global Director of Viking Marine Fire Service.
Viking says that up to 40,000 merchant ships worldwide continue to carry PFAS-based firefighting foams. Conventional AFFF is a proven solution to protect life and property aboard tankers, rigs, offshore vessels and merchant ships of all kinds - but owners need to be prepared to see it replaced, and soon, Gielen says. New global regulations will require vessels to switch by the next five-year drydocking after January 1, 2026. After that point, Viking expects port state control officials in some jurisdictions to enforce the rule strictly, given the stringency of PFOS and PFAS regulation in many nations.
Even before the regulatory requirement takes hold, owners may have incentives to switch early. The older PFOS products may be hard to replenish or replace like-for-like, since they are being phased out by OEMs, and some marine insurers already refuse to provide cover for claims related to PFOS pollution.
Regional restrictions on newer PFAS variants may limit use of this class of AFFF chemicals as well. Two months ago, the EU's chemicals agency recommended banning PFAS in firefighting foam, and Canada, Australia and individual EU nations could make similar moves.
"It’s vital that owners and operators get ahead of developments and factor in the switch to fluorine-free foams now," Gielen emphasizes, noting that it can take time to make the switch and get class approval for a redesigned foam system. "I don’t think people realize that if foam onboard is condemned from now on or if they need a top up, to comply with existing regulations it’s already an issue."
When owners take the leap, the transition to a new foam product requires a certain amount of time and effort, says Gielen. It's not as simple as putting the new compound in a tank: first the piping has to be flushed and thoroughly cleaned, the old foam has to be properly disposed of, the pumps and nozzles may have to be replaced to handle a different fluid viscosity, and class has to review the revised system to make sure that it meets requirements. Ideally, this is a project to undertake during a drydocking.
"Disposal of old foams is a more significant issue than many will be expecting," he says. "Some ports don’t have the facilities, for example, while auditing the process is part of the regulatory obligation. While we are not a disposal company ourselves, we see this as a critical part of managing the full chain of responsibility."