Q&A: Christoph Rofka, President of Medium & Low-Speed at Accelleron
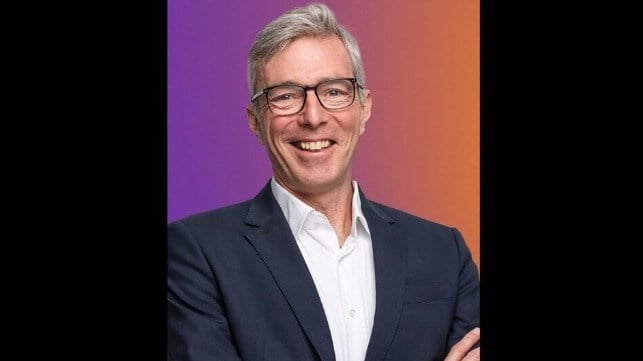
Maritime's energy transition will depend in large part on a time-tested technology - the internal combustion engine. Originally designed to run on fuel oil, two-stroke and four-stroke marine diesels will continue to provide the industry's propulsion power for decades to come, though the requirements for running them are changing. A new breed of green fuels is coming, and shipowners need as much efficiency as they can get to keep compliance costs under control. Suppliers like Accelleron - the Swiss company that introduced the efficiency-enhancing turbocharger to the industrial market 100 years ago - have a key role to play in this transition. To learn more, TME spoke with Christoph Rofka, President of the Medium, Low Speed & Rail Division.
To start off, can you tell us about Accelleron's history, and about your career with the company?
We had the honor this year of celebrating our company’s centennial anniversary. It’s amazing to think that we produced the world’s first heavy-duty turbocharger in Baden, Switzerland in 1924, and now we have over 180,000 turbochargers in operation around the world.
Before 2022, we were the turbocharging division at ABB. With their increased focus on electrification and automation, turbocharging didn’t fit anymore, so, we separated in 202, and become an independent, listed company.
At that time, we were already a global leader with a 40% market share in turbocharging, with our products in many of the world’s largest ships, from containers and tankers to cruise ships. But being an independent, midsize company gave us the chance to expand our portfolio selectively but swiftly, to integrate new technologies and services that maximize efficiency and support the maritime energy transition and path to net zero. In the process, we have further increased our business and resilience.
In 2023, we acquired Officine Meccaniche Torino (OMT) fuel injection, and in 2024, in response to the uptake of dual fuel engines and the doubled demand for fuel injectors, we added production capacity through the acquisition of OMC2.
We have also expanded our digital offering this year, through the acquisition of True North Marine (TNM), so that we can more comprehensively help shipping companies to meet their combined sustainability and commercial objectives.
My own history has been closely aligned with Accelleron’s for a quarter of a century. I graduated from Leibniz University in Hannover with a master’s degree in mechanical engineering and went straight to ABB as a turbine development engineer. I have found an interest in turbochargers, engines, ships, and the whole industry, so I stayed, and I have taken on various roles over years – which have somehow passed very quickly! In 2020, I was appointed President of the Medium and Low Speed Division, just in time to help us through the spin-off and to form the new company. I am also the Vice President of Communications at the International Council on Combustion Engines (CIMAC).
So, for the past five years, all of my efforts have centered on creating a company dedicated to sustainability and on supporting the shipping industry to reach net zero.
Q: Why is turbocharging and fuel injection so important for low-speed, 2-stroke main propulsion engines, and why do OEMs/owners choose Accelleron's turbos and fuel injection systems to meet the need?
Well, people don’t think of it this way, because it was launched 100 years ago, but turbocharging was one of the first sustainable technologies. By simply harnessing the energy from engine exhaust, turbochargers then drive compressed air into engines, offering the most economical and sustainable way of boosting engine power and efficiency, quadrupling power without adding size or weight. Over the past century, turbochargers have become integral to engine systems and a driving force behind the development of the global shipping industry.
As for Accelleron, we are good at sticking to what works, and at keeping to our roots as a Swiss company with exacting standards of quality, precision, material integrity, and service. Our headquarters is in the same location where we began 100 years ago. And when we acquired OMT, we chose a 94-year-old company that shares our values, and is also a global leader working at the forefront of innovation.
For both turbocharging and fuel injection, we cocreate with ship engine designers from beginning to end of the engine design process, so that every single turbocharger and fuel injection system is precisely designed and calibrated to fit perfectly within the unique overall engine design. Hardly two large ship engines are identical, and the same is true for our turbochargers, and to a large degree, our fuel injection systems.
That intimate cocreation process results in extraordinary precision in both the turbochargers and fuel injectors, and that precision provides an extra margin of power, efficiency, and durability. It also creates partnerships of mutual trust.
We have seen those partnerships with engine designers and engine makers expand over the years. One reason is that we have established licensing agreements, and in some cases joint ventures, especially with partners in Asia, to make engine building faster, and the whole value chain more sustainable and economical.
Another reason for those flourishing long-term partnerships is that we have supported our technology from the beginning by developing a world-class global service network in 100 locations in 50 countries. Every single member of that network is trained in Switzerland and gets two weeks of additional training to stay on top of technology changes and, of course, new sustainability regulations. So, we can ensure that those 180,000 turbochargers continue to run optimally for their exceptionally long lifespans of 20, 30, and sometimes even 50 years.
What role is Accelleron playing in the industry's drive to reduce carbon?
If you look at the historical role of turbocharging and fuel injection systems – they have been fundamental to the progress of global shipping in the past century.
Coincidentally, this year we also celebrated our golden anniversary – 50 years – in China and Hong Kong. Those five decades show exactly how instrumental these technologies are. We were one of the first companies to bring advanced power technology to China, which helped launch a movement that, in five decades, has made China the world’s largest shipbuilding and ship repair economy, right at the center of the Asian trifecta of shipbuilding countries – including Korea and Japan.
Now, as the industry reinvents itself to become sustainable, these technologies will be equally as critical.
We have entered an incredible new era in shipbuilding, predominated by dual fuel engines and the transition to future carbon-neutral fuels. Yes, the first wave of dual fuel engines was for LNG, but in 2024 we have seen methanol orders come in a very close second, and ammonia is about to see the first commercial deliveries in 2025. The Accelleron order books for turbochargers and fuel injection systems mirror those trends.
Our next-generation turbochargers are adaptable for dual fuel engines running on methanol, ammonia, hydrogen, and LNG. And we are intensively innovating and producing new fuel injectors, with new materials, shapes, and configurations for the intense chemical demands and complex design requirements of dual fuel engines running on carbon-neutral fuels.
At the same time, from now to 2030, the industry must focus on efficiency in order to reach the 2030 International Maritime Organization (IMO) target of reducing global shipping emissions by 40%, compared to 2008. The IMO has already reported that the technologies already exist to reach the 2030 target, maybe even exceed it. 25% would depend on carbon-neutral fuels, 25% wind-assisted propulsion and other energy efficiency technologies, and the rest through operational measures and lower sailing speeds. The Det Norske Veritas (DNV) classification society also calculates that shipping companies could use energy efficiency measures to cut fuel consumption across the industry by 16% by 2030, which would have the same impact on emissions, as if the largest 2,500 ships converted to carbon-neutral fuels.
Given the growing backlog of new build orders – in the thousands – and an average age of 12.6 years in the global fleet, we are not only focused on making new ships more efficient and able to run on carbon-neutral fuels, but we are also looking at quick and easy ways to cut emissions in older vessels.
You can lower the speed in those vessels, but of course, they were built to run most efficiently at higher speed. So, we have developed an upgrade program called Engine Part Load Optimization (EPLO) that combines turbocharger component upgrades with engine derating to reset the optimal engine efficiency point to around 50 to 60% of maximum power. We have been able to use our global service network to get ramp up that program quickly in the past few years, and it’s saved our customers tens of thousands of tons of carbon emissions.
Conservatively, that program delivers a return on investment through an average 3% fuel savings, within three years at the latest. In reality, the savings is usually bigger, so are the emissions cuts. And the return on investment is also much bigger, because you are preventing ships from being scrapped prematurely, and preserving that asset value.
For example, we partnered with Hanwha Engine on an EPLO upgrade that turned into a fuel savings of 10g/kWh, 5% of total fuel consumption. On a tanker, we were able to combine EPLO with a propellor upgrade, lifting the CII rating substantially and delivering a massive fuel savings of 25%.
Accelleron has been introducing 3D printing into its processes for some time, and has been working on 3D-printed turbo components - how is 3D printing useful as a manufacturing process, and what are the challenges in working with it?
We have used 3D printing, or additive manufacturing AM, for a few years.
One of the most obvious advantages for us is the ability to print a one-off component for any kind of turbocharger. If you think about the fact that we have 180,000 turbochargers in operation around the world, then you realize that there are a lot of older turbochargers out there. We couldn’t possibly keep a standing inventory of components for all of them. So, AM allows us to quickly print a one-off nozzle ring or other spare part for any of them. It’s a dynamic and cost-effective way of maintaining older turbochargers.
However, we do need to address several challenges, before we can implement AM on a wider scale. For one, the mission-critical nature of our turbocharging applications demands that we put the AM parts through extensive testing and validation, under extreme temperatures and pressures. We to balance things like weight reduction with structural integrity and high-precision aerodynamic performance. Quality control is going to be crucial, because any kind of inaccuracy can directly impact the durability and reliability of rotating parts.
In terms of environmental impact, historically, some metal AM processes have been energy-intensive, but we are seeing rapid technological advances that are increasing AM efficiency across the entire production chain. Increasingly, printing materials like metal powders can be recycled and reused to further reduce waste.
AM also gives us new design freedom and the potential for new turbocharging geometries, using far less material than traditional manufacturing methods.
In both additive manufacturing and conventional production methods, we are focused on minimizing our carbon footprint, energy use, water consumption, and waste. So, in addition to assessing immediate AM production advantages, we are conducting a lifecycle assessment, which we will use as the basis for decisions about how to grow AM production capabilities sustainably.
Could 3D printing unlock possibilities for higher-performance designs?
We have already achieved a significant milestone by successfully printing a hollow compressor and turbine wheels that matches the performance of traditionally manufactured parts, but weighs substantially less. Those lighter components improve engine responsiveness. Engines can react faster to load changes due to reduced inertia in the rotating parts of the turbocharger. In addition, such rotating components make meeting containment requirements easier, so they can further enhance operational safety.
I think we have barely scratched the surface of AM design potential, and the sustainability implications are positive.
Accelleron is active in the digital solutions space as well - can you tell us about the advantages of Tekomar Xpert, and how it is solving your clients' needs?
For us, digitalization is about making ships as efficient as they possibly can be, cutting emissions, and in the process, reducing both operational and service costs, and even supporting the energy transition.
Tekomar XPERT starts with the engine. It helps operators to keep the engine performance as close to its new condition as possible. We also have a digital module for the hull and propellor, emissions reporting, and CII forecasting. It’s all about saving fuel, thereby cutting emissions and costs for individual vessels.
With the acquisition of True North Marine this year, we have added operational and voyage optimization at the fleet level, as well as charter consulting by former ship captains and seafarers. So, now, we have end-to-end digital services that help ship owners and operators work together to manage fleets sustainably and cost-effectively.
Of course, digitalization has come to the shipping industry much later than to other industries, so we have barely begun to prove what the DNV published this year in its Maritime Forecast report, which was that digitalization could contribute to almost 20% of a ship’s efficiency.
Digitalization then becomes a no-brainer, especially since digital tools cost a tiny fraction of typical hardware solutions. Shipping companies can quickly recoup a very nominal digital investment through operational savings, while slashing their emissions. Add the EU ETS and FuelEU Maritime regulations to that equation, and you are also talking about avoiding financial penalties which will become increasingly more expensive in the next several years.
The chief advantage we can offer shipping companies is the blend of deep mechanical expertise and digital solutions that continue to evolve and improve rapidly, as digital tools do. That combination brings an especially elevated level of precision in the optimization process. But you don’t have to have our turbochargers or fuel injectors to use our digital services, they are available to everyone.
Do you see all of this moving the needle on decarbonization?
Good question. We met with a former President of Switzerland at our recent 100-year celebration. He said that after many years in office, one day, it dawned on him that it wasn’t politics shaping the world; it was technology.
Politics is playing a vital role now in helping to incentivize decarbonization, but it’s up to the industry leaders to deliver the technologies and services that actually get us there.
I have been in this industry my entire 25-year career, and for the first two decades, not much changed! But I have been deeply impressed by the way the whole value chain has come together to tackle climate change. We are in the process of using technology to reforge the industry and create a new sustainable shipping economy. What Accelleron will be doing is continuing to find new ways to make that change easier and faster.