New Tank System Could Make Hydrogen Carriers More Efficient
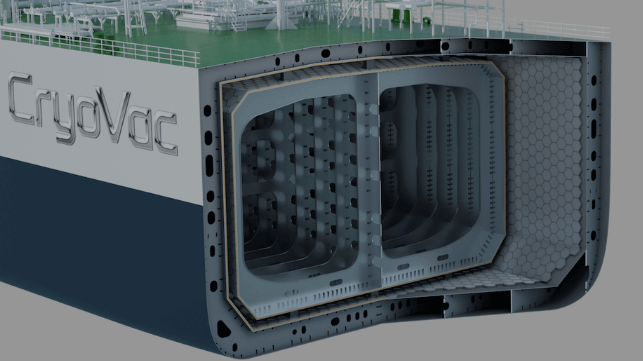
DNV has awarded approval in principle to a novel system of containing liquid hydrogen for long-distance transport. LH2 is difficult to handle: it requires refrigeration to -423 degrees Fahrenheit to maintain it in liquid form; the tiny H2 molecule can penetrate into seal materials and metals; and it makes steel dangerously brittle after extended exposure.
Existing designs - like the world's first LH2 carrier, the Suiso Frontier - use spherical tanks for the technically-challenging task. The new CryoVac panel system is designed for construction of Type B-like prismatic tanks, which are a familiar feature in modern LNG carrier construction.
Prismatic tanks conform better to the shape of the hull, leaving less unused space than spherical Moss-type tanks and allowing more room for cargo. To get there, CryoVac has invented a unique prefabricated panel system that is applied to both the outside of the tank and the inside of the hull, creating a double layer of insulation. The panel is the center of the system, and the center of the company's technology.
Each standard panel is a hexagonal steel box, which is fully sealed and then pumped out to create a vacuum. These flat boxes are designed to be factory-produced on an assembly line and then delivered to the shipyard for installation. The hexagonal shape allows for the construction of complex forms by changing the size of joining pieces, so that a continuous layer of panels can be welded together around the outside of each prismatic tank.
"This provides efficient insulation with very low boil-off rate, without challenging the integrity of the steel," said CEO Aage Bjørn Andersen, a serial entrepreneur in Norway's maritime-tech sector.
Courtesy CryoVac
The tank structure sits independently within the hold in a nitrogen-filled void. A second set of panels would be welded onto the interior of the hold for additional insulation. According to CryoVac, the panels - since they are welded together - also provide extra layers of gas-tight containment for the cargo.
The next step for CryoVac is to develop a complete design for a 45,000 cubic meter LH2 carrier with three cargo holds, each containing a 15,000 cubic meter tank.
"There is a lot of interest worldwide for a safe and cost-efficient solution for shipping of liquid hydrogen. This is the technology gap we are aiming to fill. We will going forward be entering into dialogue with shipowners and hydrogen producers," said Andersen.