Kawasaki Wins Approval and Provides Details for Large Hydrogen Carrier
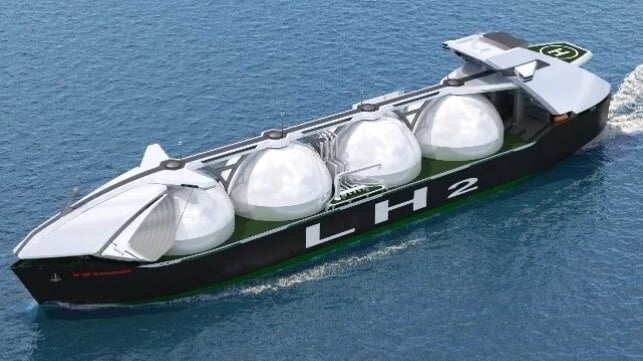
Kawasaki Heavy Industries is making significant progress in its efforts to design and commercialize the first large-scale liquified hydrogen carrier. The Japanese shipyard announced a year ago that it was pursuing the design of a large-scale vessel based on the anticipated rapid development of hydrogen as an alternative energy source. The company has now received design approval for both the cargo containment system and the vessel overall as it continues detailed design work targeting commercial operations starting in the mid-202s.
Announcing the receipt of approval in principle (AiP) from ClassNK for the vessel’s design, Kawasaki provided additional details on their concept and the challenges they are working to overcome for the design. The shipyard is working to leverage its many years of experience building liquefied natural gas (LNG) carriers and other liquefied-gas transport vessels.
“In order to build this large-sized carrier, Kawasaki leveraged design and shipbuilding technologies as well as safety-related technologies and knowledge utilized in the construction of the globally pioneering, 1,250 m3 liquefied hydrogen carrier Suiso Frontier,” the shipyard noted. Kawasaki was the shipyard and one of the partners in the project which developed the ship which completed the first international shipment of Australian-produced hydrogen to Japan at the beginning of this year. The project focused on the handling and transport developing the concept for the loading and transport of hydrogen on a 5,500-mile voyage.
Kawasaki’s large hydrogen carrier has a total capacity of 160,000 cbm of liquified gas. The vessel would be 1,135 feet long and have a beam of 187 feet. In developing the design for the hull, Kawasaki said the hull and draft of the vessel were designed with consideration for the low specific gravity of the liquefied hydrogen cargo. The vessel’s horsepower also reflects the properties of the cargo which permitted them to keep total horsepower low resulting in a higher-efficiency propulsion performance.
The propulsion system includes a boiler and steam turbine plant capable of operating using hydrogen for its fuel, and a dual-fuel propulsion system that makes use of natural boil-off gas as fuel to power the ship. The design also developed a hydrogen-gas-fuel supply system comprising hydrogen gas compression equipment, hydrogen gas heat exchanger equipment, and other components to enable the supply of boil-off gas from the cargo containment tanks to the propulsion system.
The concepts for the cargo containment system have been further refined since Kawasaki received an initial AiP from ClassNK in May 2021 for that element of the overall vessel. The 160,000 cbm of cryogenic liquefied hydrogen would be divided into four 40,000 cbm carrying tanks cooled down to a temperature of –253°C. Cooling hydrogen to that level reduced to one eight-hundredth its initial volume, making possible the transportation of larger volumes, which according to Kawasaki will help to reduce hydrogen supply costs. The cargo load would equal approximately 10,000 tons of liquid hydrogen.
These tanks utilize a newly developed, high-performance insulation system that minimizes boil-off gas. The cargo handling system is designed to load large amounts of liquefied hydrogen onto the vessel in a short time, and it is equipped with vacuum insulated double wall pipes in order to efficiently and safely transfer hydrogen in its cryogenic, liquefied state from onshore storage facilities to the vessel tanks minimizing vaporization.
During the design process, risk assessments were also carried out for the vessel’s propulsion system, cargo handling system, and other elements in relation to liquefied hydrogen. A focus was placed on developing suitable safety measures to eliminate liquefied-hydrogen-caused risk to the ship’s crew, the ship environment, structural strength, and overall soundness of the ship while ensuring safety.
Kawasaki is one of several companies working to develop the designs and systems necessary for the shipment of hydrogen. The project is part of a subsidized effort supported by the Japanese government. The project subsidy is coming from NEDO (National Research and Development Agency New Energy and Industrial Technology Development Organization) a national research and development agency. NEDO is sponsoring several projects focusing on hydrogen as it seeks to promote technological development necessary for the realization of a sustainable society.