Engine Manufacturers Get Ready for the Green Transition
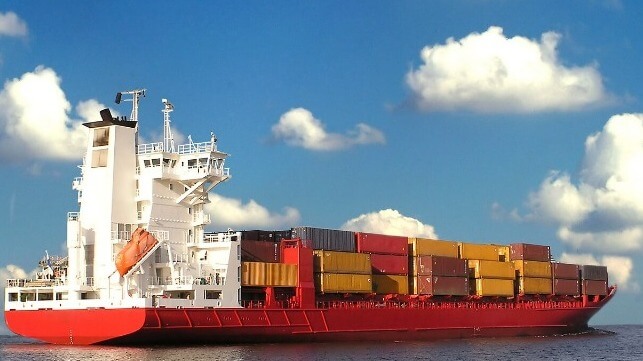
More than anyone else in the maritime world, engine OEMs have to prepare for a future without fossil fuels, and they are working hard to build diesel power systems that are future-proof and ready to make the leap.
Since the future fuel mix is not yet known for certain, one solution is in building flexibility into the product line. A ship that runs on diesel today might need to run on methanol, hydrogen or ammonia tomorrow, and a shipowner can breathe a bit easier by buying an engine that can be adapted to next-gen fuels.
Wärtsilä has taken this tack with its new Wärtsilä 25 four-stroke engine, which is designed from the outset to make the changeover. With variable valve timing, high pressure common-rail fuel injection and modular construction, the 25 is intended from the outset for simple alteration to accommodate future fuels. In fact, modifying the 25 for a next-gen fuel would be a relatively minor part of the work when it comes to a vessel retrofit.
"Switching to another fuel is primarily a change to the top side of the engine - the fuel injection system, replacement or remachining of the cylinder heads, automation system reprogramming and retuning. But in a retrofit situation, the engine is a small part of the work package. The tank and fuel pipe alterations are much more demanding and costly," says Stefan Nysjö, Vice President Power Supply - Marine Power at Wärtsilä.
The Wärtsilä 25 will likely be the company's first engine to run on ammonia, and development work is under way towards technology concept readiness in 2023. A commercial ammonia-fueled variant of the 25 will follow soon after.
In the meantime, the Wärtsilä 25 can be configured to run on natural gas or diesel, and it is Tier III compliant (with an exhaust aftertreatment system for diesel operation). An extra-long 32,000-hour time between overhauls (TBO) helps keep downtime and cost under control for the owner, and data-driven predictive maintenance can extend that timeline even further, according to Wärtsilä.
Solving fuel injection
Fuel injectors are among the key components that will have to change in order to adapt marine diesels to run on different fuel mixes. Fort Collins-based manufacturer Woodward works with all of the major engine OEMs to design the injectors they'll need for methanol, ammonia and (potentially) hydrogen conversion.
During the changeover from fossil fuels to green alternatives, owners will want to be able to use both, depending on fuel availability and price. LNG dual-fuel vessels are a great example: most LNG-powered deep sea ships have chosen to switch to VLSFO this past year because of the high price of LNG. Owners will need the same flexibility when it comes to green methanol or ammonia - and that means that engines have to be designed for dual-fuel operation.
"The biggest challenge is when you have high pressure direct injection with a dual fuel system, because there are two injectors in one unit," says Rick Boom, Woodward's director of marketing for large engine systems. "There are four needles packed in the nozzle for diesel and a second green fuel, so it's a really complex system. And making this in production and making it last under pressure - that's the challenge."
There is a cost associated with this sophisticated system, but it's worth it, says Boom. With a twin-fuel injector, the OEM can buy a "ticket to the game" for ammonia or methanol dual-fuel operation, but without the expense of retooling the entire cylinder head to accept two injector units. "That's the competitive edge we have: we can provide the solution in the same physical envelope of the cylinder head," he says.
Hydrogen is a different animal. The tiny H2 molecule is famously leaky, skilled at escaping through pipe joints that would hold any other substance inside. This is a challenge for designing injection systems, which must be able to contain fuel at high pressures in a tough operating environment. Any leakage in the engine room could have serious consequences.
"The details are still to be sorted out, but if you look at marine type approval rules, there will be some challenges getting class for hydrogen," says Boom. "However, the solutions for methanol are quite tangible. You already have the first engines in the market. Ammonia will take three to five more years, and we think it is manageable with the same component materials we use today."