Air Under the Keel
Since the first ships sailed the seas there’s been a need for ship repairs.
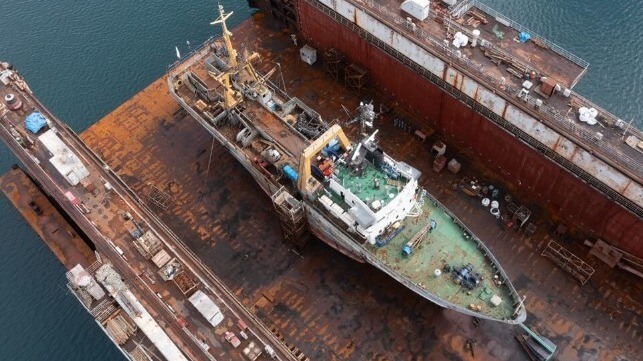
(Article originally published in May/June 2024 edition.)
In the beginning, the Greeks and Romans would wait for high tide, then haul their ships onto shore.
As ships increased in size, this became harder. The next big idea was to “careen” the ship at low tide, hauling it onto its side using ropes. In this way the hull could be accessed. Well, one side anyway.
The true sea change began in the 15th century with the British building drydocks around the world to service the Royal Navy fleet. Henry VII commissioned the first English drydock in Portsmouth, completed in 1495. This was a “graving” dock, cut from the ground and lined with stone in a stepwise fashion to roughly mimic the contour of a hull. It was fitted with gates sealed with puddle clay. These would be closed and the water pumped out, leaving the boats inside high and dry.
Gates gave way to caissons – floating structures wedged into place and ballasted down. Early caissons were designed with a traditional hull form rather than the square blocks we see today.
Across the pond in the U.S., the first drydocks were designed by Loammi Balwin Jr., a Harvard-educated engineer who spent his early years working alongside his father on the ten-year construction of the Middlesex Canal, connecting the Merrimack River to the port of Boston and completed in 1803.
The Charlestown (Boston) and Norfolk (Virginia) drydocks took six years to build, and the Charlestown dock was inaugurated in 1833 with the docking of the USS Constitution. Both docks still service the U.S. Navy to this day, a testament to their granite-based construction and sound engineering.
From Charlestown to Charleston
Head down the eastern seaboard from the Charlestown Navy Yard to North Charleston, South Carolina, and you’ll find yourself at Detyens Shipyards, where the proud tradition of shipbuilding and repair continues.
Founded in 1962 by William Detyens, the company serviced over 200 vessels in its first four years of operation from its yard along the Wando river. It was primarily government work in those days, everything from destroyer escorts and minesweepers to Coast Guard tugboats and cutters.
Today, Detyens boasts three graving docks with the largest capable of servicing Panamax-sized vessels. The facility has also grown to include modern enclosed shops for all crafts, eight 56-ton gantry cranes (on a continuous rail system), four tower cranes, rail access and over 8,000 feet of deepwater pier space – plus a floating drydock.
Maximizing the capability of the large graving docks, the yard uses keel blocks as high as 14 feet, allowing ships to fully extend their drop-down thrusters. An example of this is the recently drydocked North Ocean 102 – a McDermott-owned flex-lay vessel fitted with a swing down thruster, which completed a routine drydocking at the yard.
Other ongoing projects of note include the first intermediate drydocking of the dredge Baltimore (the largest bucket dredge in America), the Neil Armstrong oceanographic research vessel operated by Woods Hole, and the Alicon – a high-speed ferry chartered to MARAD.
Detyens Shipyards continues its support of the USN Foreign Military Sales program with employees stationed overseas who assist foreign governments with their ship maintenance programs, carrying on a longstanding tradition begun back in the 1960s.
South to the Gulf
Head further south down to the Gulf of Mexico and you’ll run into Alabama Shipyard in Mobile.
The yard has been active since 1917 as the Alabama Drydock and Shipbuilding Company. Operations expanded quickly during World War II, and the company was soon the largest employer in the area, building and maintaining vessels for the U.S. Navy. This contributed to Mobile’s growth, which became the second largest city in the state, behind Birmingham.
Tough times in the 1970s saw the yard close, and it changed hands a few times in subsequent years. Its current success began in 2019 when Alabama Shipyard LLC purchased the yard and quickly scaled from eight employees to over 300.
Once again, Alabama Shipyard serves as the largest maintenance, overhaul, repair, conversion and dismantling yard in the region.
Continuing its proud tradition of servicing military vessels, the yard currently has the Military Sealift Command (MSC) hospital ship USNS Comfort in for a 156-day drydocking and overhaul, scheduled for completion in January 2025. A few berths over you’ll find the MSC fleet replenishment oiler USNS Laramie in for overhaul. This work is scheduled for completion in September.
Currently, the yard’s next available drydock space opens in late July with pier space available immediately.
Down to the Equator
Heading farther south still – across the Gulf of Mexico, around Yucatan and down through the Caribbean – and you’ll tie up next at Astivik SA Shipyard in Cartagena, Colombia.
The ISO-certified yard has been operational for nearly 50 years. In 2004, a Florida-based company acquired a majority stake and made strategic investments with the vision of positioning Astivik as one of the leading shipyards in the Caribbean.
The yard sits on seven hectares and boasts three floating drydocks with a maximum lifting capacity of 4,000 tons – the highest in Colombia. There’s a 220-ton slipway drydock with three docking positions and an airbag slipway specially designed for barges. There are more than 300 meters of piers for alongside-works and 2,155 square meters of covered shop space.
Proudly serving the local industry, Astivik used 100-percent Colombian talent in building the Dorada, the most powerful pushboat ever designed and built in Colombia and the most efficient to operate along the Magdalena River – boasting a record 99,328 barrels transported in a single voyage.
With the Free Trade Agreement between the governments of Colombia and the U.S., the yard is free under the Jones Act to service U.S.-flagged vessels. This helps add to the impressive client roster from over 30 countries around the world.
Back Across the Pond
Take stores for a long voyage, cast off and head east. Cross the pond into the Med, up into the Aegean, through the Dardanelles and into the Sea of Marmara. A few short weeks and you’ll throw a line at a Gemak Group shipyard in Turkey.
Established in 1969, Gemak now stands out in Turkey and around the world for its wide range of skills and technical expertise. Having built 58 ships since the mid-eighties and repaired nearly 3,000, the yard is a preferred partner for vessel construction, conversion projects, vessel repairs and maintenance.
Equipped with a Capesize drydock, two floating drydocks, a 100-ton floating crane and forty-five dock cranes along 2,000 meters of wet berth space, the yard can handle just about anything that sails in.
A current project is upgrading the jackup wind turbine installation vessel Sea Installer. The upgrade includes a crane swap from 900 tons to 1,600 tons, the addition of sponsons, lengthening the spud legs by 10 meters and improvements to the jacking system.
The yard is capable of handling 5,500,000 DWT of ship repair per annum.
No More Careening from Port to Port
Modern shipyards require capacity, capability and fast turnaround for unexpected repairs.
With the advent of graving docks followed by floating drydocks, shipyards can now deliver all three essentials with the timeliness needed to get your ship back in the water doing what ships do best.
Because one thing that will never change while there are ships sailing the seas is the need for ship repair.
Master mariner Sean Hogue is a regular contributor to The Maritime Executive.
The opinions expressed herein are the author's and not necessarily those of The Maritime Executive.