Challenging China's Shipbulding Dominance
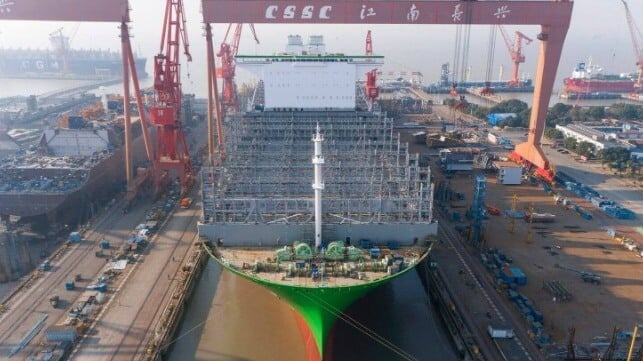
(Article originally published in May/June 2025 edition.)
China has become the most dominant player in the shipbuilding industry since World War II, when American builders like Henry Kaiser cranked out thousands of ships for the war effort.
U.S. tonnage ruled the waves in the 1940s, but times have changed. Chinese yards took home three-quarters of the world's newbuild orders by gross tonnage in 2024, according to the latest numbers. But competitors are pushing back to rebuild sovereign capacity and regain market share.
In the E.U., a nascent effort to launch a bloc-wide maritime industrial strategy promises more support for high-end shipbuilders like Meyer Werft, Remontowa and Damen. In the U.S., leaders in Congress and the White House are contemplating the most significant structural supports for shipbuilding in a generation: steep tariffs on Chinese ships, strengthened cargo preference rules for U.S.-built tonnage and a "strategic commercial fleet program" to underwrite construction of 250 new ships, among many other provisions.
The measures would create much-needed demand for American yards of all shapes and sizes – from builders like NASSCO and Philly Shipyard to repair specialists like Detyens and Colonna's Shipyard.
These plans interconnect. U.S. policymakers want to attract foreign expertise from South Korea and the E.U. to revitalize American shipbuilding and even export the most successful products (like Fincantieri's Constellation Class frigates) to allied nations. Shipbuilding is a strategic, sovereign capability, but it's also an ideal opportunity for international collaboration.
AMERICAN ROOTS, FOREIGN EXPERTISE
For decades, America's shipbuilding industry has benefited from the technology and support of foreign investors like Norway's Aker Group, South Korea's Hanwha Ocean and Italian shipbuilding giant Fincantieri, which has invested heavily on the Great Lakes.
Fincantieri Marine Group (FMG) has a history in U.S. shipbuilding dating back to 1918, the year a predecessor company opened its doors in Sturgeon Bay, Wisconsin. Its Bay Shipbuilding division is still famous for its work on "lakers," the iconic bulkers that trade the Great Lakes – like the 2022-built Mark W. Barker, the first new full-size American laker since the 1980s.
Today, Bay Shipbuilding is leading the way forward with pace-setting projects like the LNG barge Progress, the largest Jones Act-compliant LNG carrier. The 400-foot barge entered service last year and carries up to three million gallons of LNG at a time to bunker dual-fuel boxships at the Port of Savannah, Georgia. Operated by Crowley and chartered by Shell, it provides clean-burning fuel for the growing number of LNG-powered container ships that call at U.S. ports, and FMG takes pride in serving that mission.
"From a shipbuilder's perspective, being involved in a build like this is extremely rewarding," said Bay Shipbuilding Director of Program Management Jeff Frank on the occasion of the barge's delivery. "Part of you is in the ship. It goes with the ship when it leaves the yard."
FMG takes a forward-looking approach to workforce development, a pressing concern for American shipbuilders (and for many of those abroad, too). In an "extremely tight" shipbuilding labor market, it's boosted the pay and benefits package for mission-critical employees at its Marinette Marine division. As an incentive, staff at Marinette Marine may be eligible for up to $10,000 in retention bonus payments over 2024-25 plus up to $5,000 in tax-free benefits for child care.
"This benefit gives you peace of mind that your child is being cared for," says Marinette Marine engineer Hilary Homa. "Both parents can work to provide for their family."
HIGH-PROFILE JOBS
Gulf Copper has developed a reputation for tackling some of the biggest and most challenging jobs on the U.S. Gulf Coast – a region with plenty of shipbuilding expertise – like its work on the high-value, high-profile TX-10000 (formerly the VB-10000), the largest heavy-lift vessel ever built in the U.S.
TX-10000 removed the wreck of the car carrier Golden Ray from Georgia's St. Simons Sound in 2021, and her new owners picked Gulf Copper to perform a complex, five-year drydocking on this one-of-a-kind vessel, completed earlier this year.
Gulf Copper also gets the call for demanding emergency repair jobs. When the ultra-luxury cruise ship Scenic Eclipse developed problems with an azipod last September, the "discovery yacht" went to Gulf Copper for a short-notice replacement. The job was so urgent that the owner had a spare thruster flown out to Galveston aboard one of the world's largest cargo aircraft. Gulf Copper got the new azipod installed ahead of schedule and put Scenic Eclipse back in the water, allowing the "six-star" expedition cruise vessel to depart in time for its Antarctica cruise season.
The project that really sets Gulf Copper apart, though, is the ongoing refit of the USS Texas (BB-35), the last surviving dreadnought battleship from the First World War era. Texas fought in both the Atlantic and Pacific Theaters during WW II, and she provided fire support for four of the most important amphibious operations of the war – the Allied invasion of North Africa, the D-Day landings in Normandy, the Battle of Iwo Jima and the invasion of Okinawa.
USS Texas was given to the State of Texas after the war to serve as a museum ship and operated by the nonprofit Battleship Texas Foundation on the state's behalf since 2020. The foundation's biggest job on taking over management was to arrange a much-needed drydocking, the first out-of-water repair period for the century-old ship since the early 1990s.
As the battleship's long-term berth was in Houston, Gulf Copper's nearby Galveston yard was a natural choice. But the shipyard didn't have a drydock that would work for the job. As an inventive and swift solution, Gulf Copper acquired a damaged floating drydock in the Bahamas, carried out structural repairs to put it back in service, then had it towed all the way to its new home in Texas.
In 2022, when the dock was ready, USS Texas got under way on a short transit from her berth to the Gulf Copper yard. Once the battleship was out of the water, workers fitted massive new torpedo blister tanks to the hull and replaced hundreds of tons of steel from wasted framing and shell plating.
In March 2024, after an estimated 200,000 man-hours of work, USS Texas was successfully refloated and towed to a nearby pier. Final repairs and fitting-out are still under way including removal and reinstallation of the 40-ton steel foretop – the enclosed crow's nest atop the ship's superstructure that housed the directors for her 14-inch guns. (T&T Salvage donated the use of a giant floating crane for the hoisting.) Workers are also installing thousands of square feet of pine decking on her weather decks, and from top to bottom she's getting a clean new coat of period-correct Navy Blue.
The quality and thoroughness of the work were enough to win the USS Texas project the Excellence Award from Naval History and Heritage Command in 2024 – a recognition that puts Gulf Copper's Galveston yard permanently on the map. When the multimillion-dollar project is completed later this year, USS Texas will move to a new permanent berth at Galveston's Pier 15, ready for her next 111 years on the water.
TUG SPECIALISTS
In the global market for specialty vessels, Turkish yards have a prominent presence.
Tugs have been a staple of Turkish shipyard production for years, and they remain a key area of strength – especially high-spec harbor tugs with advanced technology. The country even beat out shipbuilding giant China for tugboat exports in 2023, according to Turkey's Ship, Yacht and Services Exporters' Association (GYHIB).
Sanmar Shipyard, based in Tuzla, has been building tugs for export for decades. In recent years its footprint has grown to include two yards and a block-building shop, and it can produce dozens of tugs a year. Sanmar is known for world firsts like the first LNG-powered tug and the first remote-operated tug, and it's a leader in the production of battery-electric tugs as well. To date, it's delivered more than half a dozen all-electric tugs and has plans for more.
"Our fully electric tugs stand out with zero carbon emissions, silent operation and environmental sensitivity," says Fatma Karagöl, Sanmar's public relations specialist. "These tugboats contribute to future-oriented port operations with minimal environmental impact. A fully electric tug must be considered as a whole – combining energy efficiency, long-life system design and low operating costs. This is exactly the approach we follow."
In a competitive global market, Sanmar can draw on more than 50 years of experience in tug construction, supported by its long-running collaboration with Robert Allan Ltd., the Canadian design house known for innovation in towing technology. Sanmar's portfolio covers diesel, hybrid and LNG power options, but Karagöl says green propulsion is in demand thanks to global regulations and carbon-neutral targets: "In coming years, we expect green technologies to make up a larger portion of our portfolio."
Working with the Robert Allan team and battery-maker Corvus Energy, Sanmar is making that ambition a reality. Its ElectRA series has been selected for first-of-a-kind, battery-electric projects on three continents: the BB Electra, the first electric tug in Europe; the Trapananda, the first in Latin America; and the HaiSea Wamis, the first in Canada.
Wamis is one of three Sanmar-built electric vessels imported by Seaspan's HaiSea Marine. In April, together with sister vessels HaiSea Brave and HaiSea Wee'git, Wamis welcomed the first LNG carrier to call at Canada's first West Coast LNG terminal, marking the start of a new era for the Canadian energy economy.
The opinions expressed herein are the author's and not necessarily those of The Maritime Executive.