Wind Power Developments for Sailing Boats Into Headwinds
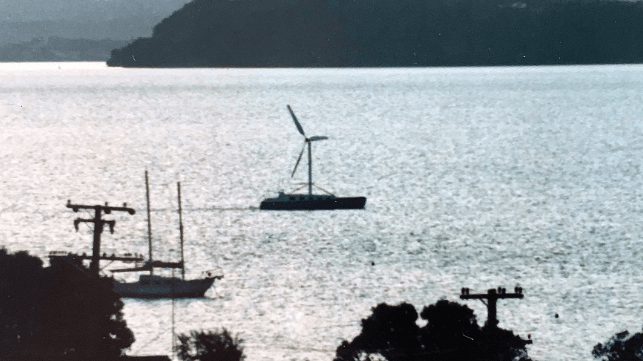
Ancient maritime history tells of the development of the lateen sail, which allowed wind-powered vessels to sail at a 30-degree angle into a headwind. It is the basis of windmill-driven vessels being able to sail directly into a headwind. During the 1970s, an inventor and mechanical engineer from New Zealand named Jim Bates built a windmill powered catamaran capable of sailing directly into a headwind at eight knots, preceding Canadian physics professor Brad Blackford by a decade.
Introduction
New Zealand based mechanical engineer Jim Bates and his daughter Jennifer designed and built his windmill powered catamaran vessel1 named “Tango”. Many years later, the concept was proven during a sail boat race at Halifax, Canada when physics professor Brad Blackford sailed a windmill powered boat directly into a headwind to win the race. British sail boat enthusiast Peter Worsley built a scale model windmill powered vessel to prove in a water tank, to illustrate that the forward thrust of a windmill-driven propeller can actually exceed the rearward drag of the windmill.
Worsley has built several small-scale windmill-driven vessels capable of sailing directly into a headwind. He discovered that using a slower-turning, horizontal-axis wind turbines that delivered high levels of torque at low RPM to be well suited for driving a submerged propeller. Worsley has developed and tested a small-scale windmill powered on a small inland lake using readily available wind. His initiative provides a basis for other enthusiasts to build and test their own small-scale versions of wind-powered vessels capable of using wind energy to sail directly into a headwind.
Early Experiences:
Jim Bates provided some insight into performance issues that he encountered when he sailed his windmill-driven catamaran at 8 to 9-knots directly into a headwind blowing between 20 and 30-knots. During powerful wind conditions that caused waves, Bates found it necessary to restrict speed so as to prevent damage to the vessel hull. The combination of propeller generating forward thrust below the water surface and the windmill producing rearward aerodynamic drag far above the water surface when sailing directly into powerful headwinds, caused weight to transfer from the bow area to the stern area.
Based on the experiences of Jim Bates, Peter Worsley built and tested many types of wind turbines intended for vessel propulsion. Unlike power generation wind turbines, he set blade angles at maximum of 45-degrees to reduce wind turbine drag and generate sufficient thrust to overcome that drag. Using smaller blade angles than 3-bladed power generation turbines has allowed Worsley to reduce turbine rotational speed and resulting blade induced wake and turbulence. He was able to install additional blades to his turbine, with the option of installing twin rotors on the same drive-shaft.
Direct Drive:
During mid-1980s, Professor Brad Blackford used direct-drive on the first windmill boat that he built and entered into a trans-harbor sail boat race at Halifax, Canada. He sailed directly into a prevailing headwind to win the race. Axial-flow wind turbines would still generate power when set at 45-degrees from water surface, with flexibility to divert up to 20-degrees horizontally from headwind direction. An angled drive-shaft on Blackford’s boat connected the windmill that was mounted high above the bow to a propeller submerged below the stern, perhaps setting a precedent for larger-scale, future wind-powered catamaran vessels.
Number of Blades:
The original into-the-wind boats built by both Jim Bates and Prof. Blackford were propelled into the headwind using 3-bladed axial-flow turbines. Peter Worsley6 has built wind-powered vessels that sail directly into the headwind using 6-bladed rotors. He set each blade at a maximum angle of 45-degrees to the drive-shaft, resulting in a slower turning turbine that drives a propeller and has sailed a vessel directly into a headwind. Recent developments in dual-rotor axial-flow wind turbines include designs where upstream and downstream rotate in the same direction and also designs where upstream and downstream rotors spin in opposite directions.
Test results involving a pair of 5-bladed rotors counter-rotating on the same horizontal-axis suggest possible future application in vessel propulsion. Wind turbine powered vessels are subject to limitations on blade diameter along with its weight and height above the deck. In such operation, each of the rotors would be installed on a horizontal-axis upstream and downstream sides of a gearbox placed at the top of a tower, with concentric counter-rotating vertical driveshafts inside the tower. At the bottom end, bevel gears and a differential would recombine power from the vertical shafts to drive a propeller with steering capability.
Vertical-axis Turbines
A vertical-axis turbine offers the advantage of being able to directly drive a propeller, including an axial-flow propeller operating on a vertical axis and using inlet and outlet ducts to redirect water to achieve propulsion. A Voith-Schneider type cam-type mechanism located below the turbine assembly would continuously reset turbine blade angle during each assembly rotation cycle, to allow forward thrust below water to exceed wind drag above water. Vertical turbine blades that resemble airfoil-sails would continually change angle and duplicate the sail angles of a sail boat tack-sailing into a headwind.
Installing a narrow-angle deflector upstream of counter-rotating vertical-axis twin turbines of small diameter that inter-mesh like gears, would redirect the headwind to the downstream side of each turbine and reduce drag by shielding the upstream side from air flow. The air deflector would allow the vessel to sail within 15-degrees of wind direction, assuring that both turbines provide propulsion. At larger angles from the headwind, a single turbine would remain operational and assisted by either deck-mounted sails or airborne kite-sails. Both a single turbine with movable blades and twin counter-rotating turbine would require further research and testing.
Large Axial Turbine
Windmill-powered vessels built by Jim Bates and Prof. Blackford represent small-scale prototypes of future windmill-powered large vessels. The vessel built by Bates used a 3-bladed turbine of 33-feet in diameter and delivered sufficiently low torque to allow gear systems to transfer power from the wind-mill hub to the propeller. As the physical size of axial-flow wind turbines increases, rotational speed decreases, with torque increasing dramatically. In a 30-mile per hour wind, a 120-ft diameter turbine will deliver over 500-Hp at 50-RPM at over 50,000-lb-ft of torque.
When wind speed reached just under 60-miles per hour, power output would rise to over 3,600-Horsepower at 50-RPM and over 185,000-lb-ft of torque. As an alternative to costly and heavy gear trains, a multi-section large-diameter hollow drive-shaft installed an angle could carry power from a large-diameter wind turbine installed above the bow to a propeller located below the stern, where exit ducts could redirect the flow of water. There may be scope to install a pair of wind rotors that rotate in the same direction, at a distance apart from each other on the angled driveshaft.
Combined Wind Technologies
Some designs of wind turbines that directly drive propulsion technology have sailed vessels directly into headwinds and able to deviate up to 20-degrees from headwind direction. As angle between wind and sailing direction approaches 30-degrees, other wind power technologies such as deck-mounted airfoil-sails including telescopic versions, airborne kite-sails and deck-mounted rotating Flettner rotors become more effective than wind turbines as providing for vessel propulsion. Future wind-powered commercial vessels and passenger cruise vessels would include multiple different wind-power technologies to provide propulsion, including kite-sails for sailing with prevailing trade winds.
Conclusions
Boat builder Jim Bates and physics professor Brad Blackford proved that windmill-driven vessels could sail directly into a headwind. Sail boat enthusiast Peter Worsley has undertaken research into optimal blade angles for axial-flow wind turbines. His work with working scale-model wind-powered boats provides a basis for other enthusiasts and researchers to expand on researching and developing wind-powered technology capable of sailing vessels directly into trade winds, including on trans-oceanic voyages. Worsley’s findings provide a basis to undertake further research into adapting vertical-axis wind turbines to vessel propulsion that includes sailing directly into headwinds, with little directional deviation.
On very large vessels, large-scale vertical-axis wind turbines including typhoon capable versions offer the combined advantages of lower center of gravity than axial-flow turbines and directly driving a propeller, including an axial-flow propeller combined with ducts to redirect water flow. While axial-flow wind-mills with gear drive would be suitable for smaller catamaran vessels, large-scale axial-flow turbines operate at low RPM with extreme levels of torque that make gear drive problematic. While a suitable typhoon capable axial-flow propulsion wind turbine is possible, it would need to use an expensive electrical generator and propulsion motor(s).
The opinions expressed herein are the author's and not necessarily those of The Maritime Executive.