Technology, Regulation and a Case of Oily Separation
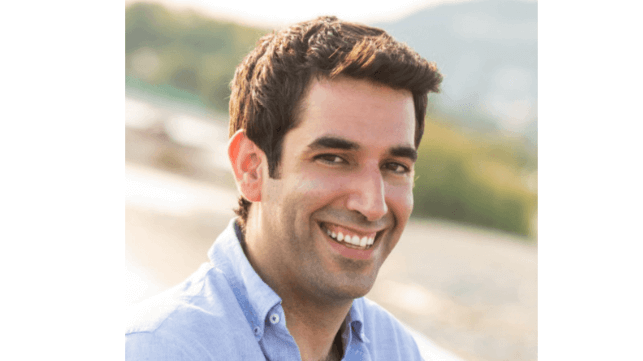
[By: RWO]
The quiet role marine equipment manufacturers often play in supporting regulators has been making ripples in bilge water circles – a part of maritime law which has been largely becalmed for two decades.
Leading water and wastewater treatment systems supplier RWO says it recently received a request from a tug builder to run unofficial tests of B100 biodiesel and establish how the low carbon emission blend worked under oily water separation.
The work follows a growing number of requests for the ERMA FIRST GROUP company’s dedicated testing and training facilities in Bremen to examine alternative fuel types and verify their behaviours in practical conditions, according to RWO.
Regulators often consider guidance from marine equipment suppliers as they develop new rules covering safety-related and environmental legislation. The fact that makers frequently need to provide training as a condition of equipment approval, once new rules have been agreed, further emphasises their important role in upholding maritime law.
Recently, however, Stratos Papamichalis, Managing Director, RWO says that oily water separator system suppliers have needed to provide another bridge between users and the authorities, based on the way an established piece of legislation has been applied. “In March, the Australian Maritime Safety Agency acknowledged that flow or pressure sensors are ‘not specifically’ required for the alarms mandated in IMO oil filtering provisions for bilge water under MEPC107(49),” says Papamichalis. “However, AMSA Marine Notice 2024/03 went on to interpret the failure of a 15ppm bilge alarm to activate the automatic stopping device in the absence of sample flow as non-compliance.”
In such cases, the AMSA advisory adds that a ship is likely to be detained until the system complies with MARPOL requirements, says the RWO Managing Director.
In June, ClassNK recommended countermeasures to address the AMSA notification which would require equipment modification where sensors were fitted in the sampling line or the
removal of the valve where they were absent. “We have confirmed that manufacturers' responses vary, with some finding it difficult to comply… and others needing more time to respond to the issue,” said ClassNK.
In July, Sire24.com characterized AMSA’s guidelines as ones that “expand upon the existing IMO Resolution”, and went on to recommend interim measures that could include “sealing
sampling valves in the open position”.
Also in July, the Bahamas Maritime Authority told owners: “If not already fitted, the company should consider the installation of the flow sensor and/or pressure sensor in the effluent sampling line as this would aid officers in verifying that a representative sample is flowing through the line.”
By September, the matter was no closer to resolution, with China Classification Society advising: “If the ship cannot meet the requirements, it is recommended that the shipowner fitted the pressure and flow alarm device on the sampling line, or upgrade the existing 15ppm alarm device to meet the inspection requirements of the ship in Australia.” Various classification societies advocate for sensors and flow meters to be included in bilge water sample lines and, as the company first to market in offering the capability over a decade ago, RWO fully aligns with the view. In fact, a flow sensor is installed on the sample line in all OWS-COM models. Even when its equipment pre-dates RWO’s inclusion of a flow sensor, a retrofit kit is available for any unit.
“RWO invested in a technically superior solution and the market has increasingly come round to our way of thinking, but we have also been liaising with our customers and with AMSA to make sure that this misunderstanding of the rules does not stand,” says Papamichalis.
“In the meantime, we are in the pleasant position to reassure many customers that have called us regarding the AMSA Marine Notice, that we’ve got them covered!” But, according to Andreas Rosebrock, Sales Director, RWO, the supplier’s decision to go above and beyond regulatory requirements in pursuit of best practice is wholly separate to its duty to ensure that customers enjoy peace of mind when it comes to compliance.
Going beyond what the rules prescribe, RWO has developed the Clean Bilge monitoring system CBM+, for example. CBM+ does not replace the bilge water separator required under IMO Res. MEPC.107(49), but it does provide an additional line of defence against contravention of the rules and records the date, time, location, flow rate and oil content over 18 months, says Rosebrock.
“CBM+ features a flow meter and GPS recording system to verify that non-compliant oily water mixtures are not discharged,” he says. “If the system detects that the oil content is above the predetermined limit, it automatically recirculates it back into the bilge tank.”
The products and services herein described in this press release are not endorsed by The Maritime Executive.