Crew Training is a Crucial Factor for Efficient BWTS Operations
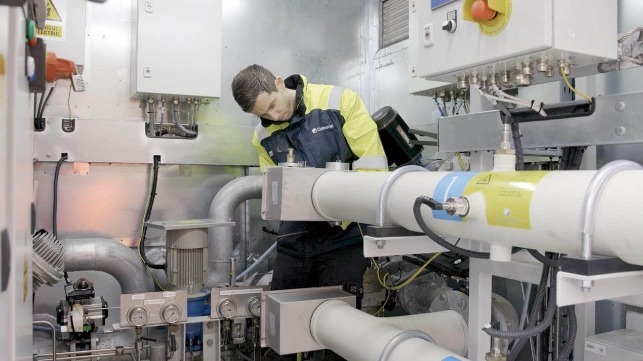
[By: Optimarin]
Improper operation of a ballast water treatment system (BWTS) can result in additional costs, delays and compliance issues for shipowners. Crew training is an essential element in a BWTS installation to provide technical insight, operational expertise and regulatory knowledge to avoid trouble and ensure smooth-running ballasting operations, according to Optimarin.
The Norwegian BWTS supplier, which has delivered over 1000 such systems to date for vessels worldwide, has therefore developed an online training programme dubbed OptiLearn as part of its educational efforts to empower crews for effective ballast water management. OptiLearn courses have so far been completed by more than 1200 successful participants with positive feedback.
In addition, Optimarin provides training on system simulators at various onshore locations and through its service engineers during BWTS commissioning onboard.
“The purpose of such training is to give the crew a good overview of the system to understand its functionality and components, how it operates and what are the maintenance requirements,” says Optimarin System Engineer Øystein Myhrvold, who created the OptiLearn portal and content.
“This ensures a good user experience for operators of the system and correct operation of the BWTS in accordance with laws and regulations for handling of ballast water.”
BWTS learning curve
Many crews are still on a learning curve with ballast water treatment, which is relatively new technology for shipping as it only became a regulatory requirement in September 2017 when the IMO’s Ballast Water Management Convention entered into force.
The convention, which will require all ships to comply with the so-called D2 standard for ballast water discharges from September 2024, stipulates that each vessel must have a valid Ballast Water Management Certificate, a Ballast Water Management Plan and Ballast Water Record Book.
“There are several risk factors with ballasting operations. A major one is incorrect operation of the BWTS that can result in both environmental damage and serious financial consequences in heavy fines from port states due to non-compliance with the convention, which they are required to follow,” Myhrvold explains.
And simply installing a class-approved BWTS is not sufficient to achieve compliance in the longer term as it requires crew knowledge of different ballast water testing requirements in various parts of the world, such as the US.
Clearly, inefficient ballasting can also result in costly delays at port that can have a commercial impact for the shipowner by affecting voyage schedules and delivery times.
Saving money on maintenance
Another potential risk factor is damage to BWTS equipment and components due to a lack of operational competence, such as through running the pump dry. This may necessitate premature replacement of such spare parts, resulting in higher maintenance costs.
Optimarin Service Manager Arne Lund says the company conducted a test in which it compared ballast water management on two vessels with identical equipment. This found that relatively higher maintenance expenses on one of the vessels was a direct result of poor operation of the BWTS.
“By providing training for the crew, we saw consumption of spare parts and other wares could be reduced significantly, thereby saving money. If the operator understands the system and knows how its components work, this makes it possible to anticipate and quickly resolve issues so the BWTS can run effectively with low maintenance costs over many years,” he says.
The OptiLearn training platform hosts technical, operational, and service and maintenance courses that give participants a comprehensive overview of the Optimarin Ballast System. These cover system components and their functionality, operational and emergency procedures plus contingency measures, and how to maintain the BWTS.
“We are confident this will benefit the user in operating, servicing and troubleshooting the BWTS, avoid damage to equipment and reduce system downtime,” Myhrvold says.
User-friendly system
Course participants have responded positively, giving it a rating of 4.7 out of 5 and stating it was “very educational”, “well explained” and gave “nice and clear training about the BWTS”. The course is available online 24/7 and can be accessed anywhere via an app on mobile devices, enabling participants to study whenever they want, with results uploaded to the OptiLearn portal.
Myhrvold highlights the fact the Optimarin Ballast System is designed for ease of operation with a user-friendly interface and a high level of automation, having been steadily upgraded with improved functionality based on client feedback over more than 20 years of BWTS deliveries.
“Using the Optimarin Ballast System has been simple and intuitive since the first version. Our advanced and fully automated system requires little work from the operator. This makes ballast water treatment as uncomplicated as possible, thus allowing crew to focus on cargo operations and other high-priority tasks,” he explains.
Functions such as single-click start-up, a visual display of ballasting progress in the control panel and alerts on component status minimise the need for user intervention with the system, while giving a full overview of operations.
Furthermore, the cloud-based digital solution OptiLink enables Optimarin technicians to remotely monitor the system through internet connectivity and thereby provide maintenance support, with over-the-air software updates. In addition, tracking of BWTS operations with OptiLink can help to pinpoint where crew training is needed.
Hands-on training
Along with e-learning, Optimarin provides crew training on fully functional demonstration systems located at a test facility at its head office in Sandnes, Norway, as well as at ship management company Anglo-Eastern’s maritime training centres in Mumbai, India and Manila in The Philippines that host regular courses and workshops for seafarers in BWTS operation.
Optimarin also prioritises hands-on instruction for operatives during system commissioning to ensure they are familiar with the BWTS and enable them to ask questions. The company’s service engineers have clear guidelines to provide basic guidance and determine specific training content for different segments of crew, such as engine room or bridge personnel, during handover of the BWTS.
“We see that a lot of start-up issues with new systems could be avoided simply by including crew training in the planning phase. It is also an ongoing process to ensure crew have the knowledge they need during service visits to minimise the need for maintenance,” he says.
Myhrvold says there is now a greater industry awareness of the need for expertise in ballast water treatment, with a heightened focus among both the ship’s management and crew on training in both the technical and operational aspects of a BWTS.
“The crew and customer should be trained to have a good technical understanding of the Optimarin Ballast System, as well as in-depth knowledge of running the system. This will result in fewer operational problems, reduced need for support and an enhanced customer experience overall,” he says.
The products and services herein described in this press release are not endorsed by The Maritime Executive.