One Knot at a Time
They play different roles, but seals and bearings are what keep a ship running smoothly.
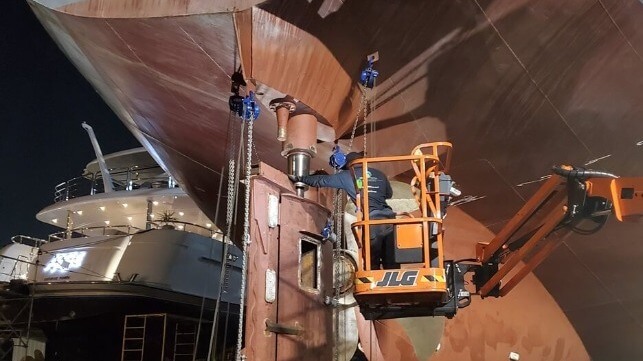
(Article originally published in May/June 2024 edition.)
Seals are important for the role they play in containing pressure and eliminating leakage and contamination. Bearings reduce friction and are key components for transferring motion. When functioning properly, seals and bearings are the furthest thing on the chief engineer’s mind.
They keep ships moving in a consistent and reliable manner, one knot at a time.
“Ship Happens”
Life on the water brings something different every day. If the weather is fair, then the odds are pretty good that something else isn’t, and mariners don’t want that something else to be seals or bearings failure. The best way to prevent that is through monitoring and preventive maintenance.
AME Solutions understands this. Founded by Rich Merhige in 1992, it quips that “In a world where ‘Ship Happens,’ AME stands out as a reliable partner you can count on to help you get back to smooth sailing. Our precise solutions ensure your path is clear, aligned and your objectives are met.”
When shipowners contact AME, they choose a team with deep understanding of a ship’s machinery and equipment. This translates into a well-developed, innate knowledge of the leading indicators that can direct attention to mechanical fault points, often the seals and bearings.
The company is keen on the current state of AI and cloud-based software as well as on how “Industry 4.0” will affect ship management systems in the very near future. A goal is to have wireless sensors that provide data to cloud-based software with the ability to interpret the data and provide recommendations to correct issues at the root cause.
As vessels are built lighter with more power than ever, vibration issues are becoming more common. Vibratory movements place stress on every joint in a vessel’s machinery, and AME knows this makes seals and bearings important strategic points of reference for a vessel’s structural and mechanical health.
To monitor vibration’s effects, AME uses multiple cutting-edge technologies, sensors to monitor temperature and pressure and complex, laser based, three-dimensional measuring and data acquisition tools that are highly customizable for each customer and their specific applications. It’s a winning formula.
Global Name
Thordon Bearings began making seals and bearings for the maritime industry in the late 1960s out of Ontario, Canada and has since become a global name. A revolutionary product is the TG 100 Tail Shaft Seal, which is pneumatically activated in the event of a catastrophic failure such as a broken or bent tail shaft. Upon activation, this device will reseal the tail shaft and eliminate the potential for flooding and the environmental release of hydrocarbons.
Thordon’s product list includes deck equipment bearings, shaft seals, shaft bearings, rudder stock housing and bearings. In addition, Thordon provides turnkey service to install, maintain and custom-fit its products in over 100 global locations. It’s a level of service that is often best accomplished through partnerships with other great organizations.
Minnesota-based Mactech is one such organization. The company is well-known for on-site precision cutting and machining and offers services such as pipe beveling, line boring, diamond wire sawing and internal pipe cutting.
Just this past year an inland marine towing company consulted with Thordon on a project installing steering gear bearings in one of its tugs. The company owns a repair facility in Illinois and preferred to complete all repairs and maintenance in-house. However, after several unsuccessful attempts it opted for external assistance and consulted with Thordon. The initial step was to measure and fit the bearings.
Mactech technicians were on site for this phase and, after analyzing the spacing issue, proposed the solution. Mactech’s field team utilized its specialized boring drills to complete the necessary propulsion strut housings, steering systems as well as 12 total rudder bores. The collaboration resulted in a precision install and the vessel back on the water for the satisfied customer.
Aftermarket Services
For vessel owners who require aftermarket services, Dutch-based AEGIR-Marine has been a go-to solution since 2000.
AEGIR will respond globally for customers requiring services on thrusters, propellors, stabilizers and stern seals. It provides customers with expedited global support via a sophisticated infrastructure involving four regional offices with service hubs located on every continent except Antarctica. Servicing a market of primarily commercial vessels ranging from yachts to cruise ships and deep-draft tankers, an AEGIR technician may be offshore with a dive team making an emergency seal to a stern tube, or in a shipyard for a service call, or advising a customer on options for a retrofit.
A can-do spirit of innovation is key to its success.
AEGIR is currently working with Bureau Veritas to develop a system to remanufacture thrusters to a class-approved “As New” standard that goes beyond just reconditioning a used thruster for extended service life. Rather, the goal is to restart the service life. The cost benefits and emissions reduction for this type of service provide an advantage that every vessel owner should be excited about.
Positive Impact
Helsinki-based Wärtsilä’s history goes back nearly two centuries to a time when the majority of seagoing vessels were still under sail power. It has since grown into a global leader in smart technologies and complete lifecycle solutions. Today, its commitment to sustainability and cutting-edge technology is evident across its diverse product range.
Among its many specialized divisions, Wärtsilä Shaft Line Solutions stands out as an original equipment manufacturer with over 100 years of experience in designing, manufacturing and servicing shaft line products for the marine market. The division is dedicated to enhancing the performance, reliability and sustainability of marine and power generation systems, spearheading the development of advanced shaft line technologies to ensure optimal efficiency and longevity.
It recently introduced a new suite of products as part of its modular FuTube technology. By improving the efficiency, performance and availability of the vessel, these products – EvoTube, IntelliSafe, 10-year Airguard Seal and the Shaft Line Monitoring System – reduce costs while increasing profitability.
EvoTube redefines shaft line maintenance with its compact design and versatile lubrication options that enhance the system's efficiency and reliability while reducing its environmental impact. IntelliSafe, a game-changer in bearings technology, optimizes performance and significantly reduces operating costs through integrated smart sensors and analytics to monitor performance in real-time.
The 10-year Airguard Seal ensures watertightness and durability with upgraded features designed for extended service life while the Shaft Line Monitoring System offers real-time insights, enabling proactive maintenance and optimized powertrain performance.
Wärtsilä’s commitment to technical excellence is evident in the new offerings, designed to enhance operational efficiency, minimize risks and contribute to a more sustainable maritime future.
“At Wärtsilä, it’s not just about innovative products – it's also about the positive impact they create,” says Rob Burford, Vice President of Shaft Line Solutions. Adds Sales Director Panu Sorvisto, “We take sustainability below the waterline. By combining innovation and sustainability, we want to be one step ahead of our competitors.”
Commercial diver Pat Zeitler is Director of Business Development & Program Advancement at The Ocean Corporation.
The opinions expressed herein are the author's and not necessarily those of The Maritime Executive.