Clean and Pure
In an environmentally conscious world, water treatment technologies are doing their part.
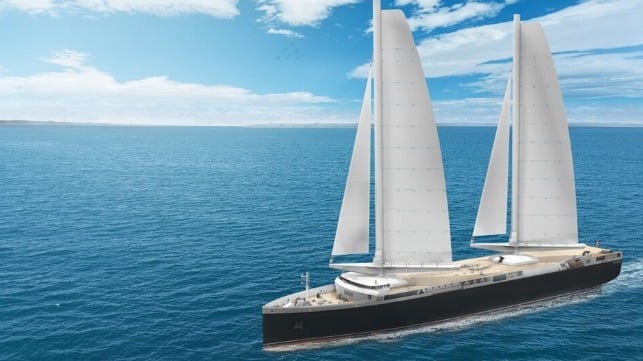
(Article originally published in Jan/Feb 2024 edition.)
Shipowners have every incentive to ensure the cleanliness of their operations and go to great lengths to find the best solutions to keep environmental impact to a minimum. Ballast water and sewage need proper handling before discharge, and the penalties for noncompliance are steep in some jurisdictions.
Proper treatment requires the right equipment for the vessel and its mission: Each ship's specifications and trading patterns are different, and the key to high uptime and good performance is to find the right combination for the vessel.
Trusted suppliers can help with selection, engineering, installation and aftersales support, keeping the environment protected – and the ship out of trouble.
Listening to the Customer
French water treatment company BIO-UV grew its business onshore in the early 2000s, years before ballast water discharge was regulated by the International Maritime Organization (IMO). Today BIO-UV is a mainstay among ballast water treatment system (BWTS) manufacturers, and it’s made its name by meeting the specific needs of each sector.
“We listen to our customers’ requirements and react. This is the key to our success,” says Maxime Dedeurwaerder, head of BIO-UV Group’s maritime division.
This approach benefits BIO-UV in the yacht and OSV markets. For these small vessels, minimizing equipment footprint is a top priority. BIO-UV’s latest low-flow-rate system is the smallest and most compact BWTS on the market, designed for smaller vessels that have a discharge rate of 150 cubic meters per hour or less.
It was first developed to meet the needs of an Italian yacht builder who had to fit a system into a limited space in a machinery room, and its compact size makes it popular with other small vessel operators too. Like all of BIO-UV’s ballast water treatment units, it relies on filtration and UV-C disinfection, without any chemicals.
"We’ve also received orders for OSVs, research vessels and tug retrofits in Korea that have limited ballast capacity but still need to comply with the BWTS convention,” Dedeurwaerder notes.
The offshore sector is a growth area for BIO-UV, reflecting both the rebound in offshore activity and the suitability of the firm's products for the oil and gas industry. BIO-UV prides itself on rapid and reliable service, which is key for the high-uptime requirements in oil and gas. Its international service team provided the equivalent of six years of service days in 2023.
“We have more than fifteen years’ experience in the commercial newbuild and retrofit sectors, and these skills can be easily transferred to offshore supply vessels, drill boats and drilling platforms," Dedeurwaerder adds. “The recent uptick in the offshore energy business is delivering confidence that the sector is looking to invest again.”
The jewel in the firm's crown, though, is its partnership to supply the ballast water treatment system for a new sail-powered cargo ship, the Neoliner. This novel, 136-meter vessel is under construction at Tuzla Shipyard for Neoline, a French firm with a mission to commercialize sail-powered transport. Neoline’s first 5,000-dwt ship will operate in the North Atlantic beginning next year, and it’s expected to consume up to 90 percent less fuel on a dedicated liner route.
It’s a high-profile assignment: The sail-powered ro/ro will be a "flagship of the French merchant navy," and BIO-UV will be there to help along with a who’s-who of French maritime enterprises. "As a company, we’re very concerned about global climate change and sustainability. Our chemical-free ballast water treatment systems are designed to be the most environmentally safe solutions available. It was the obvious step forward to team up with Neoline and other shipowners and yards in developing wind-powered vessels,” says BIO-UV Group CEO Laurent-Emmanuel Migeon.
BIO-UV also supplied a ballast treatment system for the well-known sail cargo ship Grain de Sail, and Migeon expects there’ll be even more sailing-vessel project announcements in the near future.
Difference Maker
Ships are floating communities, and like any town or city they generate wastewater. Near coastlines and in environmentally-sensitive regions, wastewater discharges are tightly regulated. Reliable, quality equipment is required to meet these standards and keep operations running smoothly.
Biological digestion followed by disinfection is the common method for treating blackwater waste, and there are many options on the market that use this established technology. Czech/German manufacturer ACO Marine says that while the method is proven, the details matter.
"The difference is how the technology is packaged in order to maximize treatment efficiency and handle a denser wastewater load while keeping the equipment space envelope as low as possible," says ACO’s Head of Sales, Chaitanya Shah.
Its Clarimar MF model uses UV disinfection before discharge, unlike many competing designs that rely on chlorination and chlorine neutralization. This allows the company's systems to operate without any added chemicals, eliminating the need to source and stock consumable supplies for sanitation on board.
The tanks are made of a polymer material for a long, corrosion-free lifetime with about 40 percent less weight than a steel plant. They also come in a flat-pack format so they can be installed without a yard period. The tank components can be moved into the ship's machinery spaces and assembled in place without cutting into the hull or taking the ship off-hire.
"We have the Clarimar MF units fitted everywhere from tugboats to offshore platforms and mega-yachts to modern navy frigates," Shah says. "We’ve seen increased activity overall post-Covid-19 in most areas of shipbuilding and retrofit repairs, especially in the military and cruise sectors."
In partnership with local stakeholders in the Baltic, ACO has developed a system that meets or exceeds all the special requirements for the region's sensitive waters. "Our ties to the local industries and communities ensure we can perform ‘real-world’ prototype testing and assess the performance and results," says Shah.
ACO's Maripur NF range controls nitrogen and phosphorous levels in the discharge water, as required for at-sea discharges from passenger vessels in this designated "special area." Maripur NF's ultrafiltration treatment also addresses microplastic pollution, going beyond the letter of the law and helping with a growing environmental issue.
Technical performance is critical, but for shipowners and operators the flexibility of the installation footprint and the possibilities for customization are also important. "It’s our team's willingness to engage and contribute from the initial design concepts to final installation that adds further value," says Shah.
Made-in-America
Fort Lauderdale-based Headhunter has been in the marine sanitation business since the early 1980s when it began providing plumbing services for South Florida's luxury yacht industry.
The company quickly grew into manufacturing with the introduction of the Royal Flush marine toilet, which has become a standard in the yacht market. Today, it also builds sewage treatment plants and provides both biological and chemical/physical treatment options for clients of all stripes. Headhunter products can be found on rigs, OSVs, yachts, warships and merchant vessels with the naval and yacht markets being its biggest.
Headhunter's Tidal Wave system uses biological treatment supplemented by additional oxygen to speed up the decomposition process. The discharge water is treated with a mild disinfectant to ensure a "complete kill" of any pathogens. These systems are Coast Guard-certified to meet 33 CFR Part 159, and are well suited for U.S.-flagged vessels.
The company also makes a chemical/physical treatment plant that meets the tough standards of IMO MEPC 227(64), which is now in force for internationally-trading ships. The TidalWave HMX uses a combination of chemical oxidation (chlorination) and physical processes to break down, separate and disinfect the biomass, followed by polishing the effluent with an activated-carbon filter.
It can handle graywater too, and it’s available in treatment rate ranges from 300 to 50,000 gallons per day. This is enough to cover everything up to the size of a rig or an expedition cruise ship.
As might be expected for an all-American firm, Headhunter is a frequent supplier for U.S. Navy ships like the Spearhead-class Expeditionary Fast Transport (EPF) USNS Cody. EPFs are capable of moving as many as 300 troops at fast-ferry speeds of up to 40 knots. For the Cody, which will be specially configured as a hospital ship, Headhunter’s team supplied a 15,000 gallon-per-day treatment system based on its Tidalwave HMX.
Headhunter builds and tests all its systems in-house in a 50,000-square-foot facility in Fort Lauderdale and believes in vertically-integrated manufacturing (down to soldering its own circuit boards). This allows the team to provide customization for each vessel’s unique needs. It has its own team of pipefitters and welders and can provide turnkey installation of a full sanitation system from the head to the discharge pipe – a rarity for a manufacturer in this segment.
This level of quality control allows the company to offer a five-year warranty on its sewage treatment systems. "Headhunter offers quick delivery and a quality product that is fully functionally tested in our factory prior to delivery,” says Vice President Mark Mellinger. “Some of our competitors do not undertake such rigorous quality checks."
This provides more certainty that the vessel will stay compliant and keep running without a breakdown – the kind of certainty that every shipowner needs.
Paul Benecki is the magazine’s News Editor.
The opinions expressed herein are the author's and not necessarily those of The Maritime Executive.