Learning From U.S. Shipyards' Experience With a Digital Mindset
Australia's plan to expand its surface force will require a similar approach adopted by US shipbuilders to service US Navy contracts
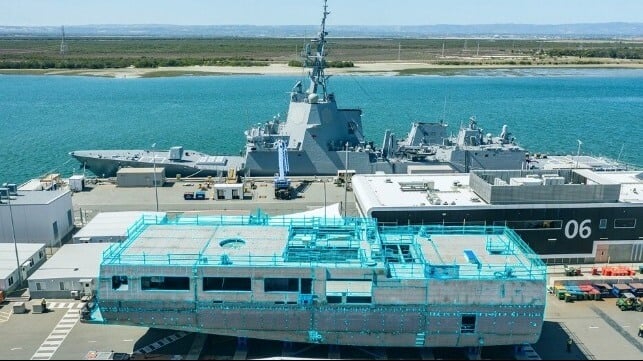
The announcement that Australia plans to more than double the size of its naval fleet did not come out of the blue. The Defence Strategic Review of 2023 clearly outlined the need for a holistic approach to the strategy, planning and procurement of assets for the defense organization.
The plan for A$11.1bn of investment that will add 11 new frigates and six further large vessels with long-range missile capability is designed around building new warships more rapidly than in the past while maintaining a commitment to increasing defense shipbuilding capability in Australia.
The question that arises immediately is, can the program be delivered on schedule and somewhere near budget? A fully digitalized approach to the design, engineering and production process is essential for this to happen.
Only in this way can the government be confident that they have the best possible vessels on delivery and that they can be efficiently operated and maintained across their lifecycle.
This will mean assembling and managing more data than has previously been possible and making it available to underpin long-term maintenance to keep the vessels available. The yards, main contractors, vendors, service providers – and the Navy itself - will all need to adopt a digital mindset.
Learning from experience
While the challenges of the Australian industry are unique, many similar problems have arisen as part of other nation’s naval shipbuilding programs. In other cases, shipbuilders focusing on delivering commercial vessels have been forced to address similar challenges.
Australian shipbuilders can look to international examples of successful digital strategies that they can implement within their organizations.
For example, the complexity of maintaining and upgrading existing vessels and the need to build and integrate new vessels into the fleet has forced the US Navy to implement a single, unified product information and digital engineering strategy. In this case, the product refers to configuration-managed models and technical data for ships and weapon systems.
The situation the US Navy, NAVSEA, and US Navy shipbuilders faced before introducing this new strategy has many facets that mirror the current situation in Australia. These included an urgent and increasing need to deliver more vessels more quickly and upgrade existing vessels with more advanced systems at an increasing rate, no existing standards on asset data types and interfaces, and end of life of numerous software packages commonly in use across the larger naval ecosystem.
Shipyards play a pivotal role as they generate, and in many cases own, the information that is key to program management. Through our work with defense shipbuilders in the US and the US Navy, we identified and initiated the technical steps required to create a trusted and reliable method to communicate vessel requirements from the Navy to shipbuilders and systems models in the reverse direction.
Shipyards are choosing an information platform that integrates seamlessly with the Navy’s Product Lifecycle Management (PLM) system. This approach eliminates a significant portion of the implementation work that the shipyard would otherwise need to take on. In effect, the effort of examining what data needs to be mapped, how it will be exchanged and building this exchange is short-circuited.
One of the realities of defense programs is the need to perform data and model conversion. For older vessels, this is often because the legacy systems used as part of the original design are either unavailable or unsuitable for use in repair/refit work.
In the case of new vessels, designs may originate from a CAD system that is not in use at the shipyard responsible for building the program, or multiple shipyards are building the same vessel but have different technology infrastructures. In both cases, the need to convert data quickly and in a way that reduces conversion costs (both in terms of time and post-processing requirements) is a core requirement.
Having worked with major defense shipyards and design agencies as a partner on numerous conversion projects, our team has revealed the significant cost and time savings of converting existing information into a new platform rather than spending labor hours on additional detail design work.
Achieving the desired outcomes
The Australian shipbuilding industry is quickly being forced to speed up an already rapid digital transformation to meet the new defense reality. Doing so will depend on shipyards employing new technologies but also on a changing mindset and approach to building ships.
A shipbuilding-specific PLM approach supports the industry's unique nature, allowing a fleet of vessel configurations to be managed discretely but remain linked to each other. A PLM tool allows for the effective use of a vessel or fleet’s digital twin(s) that can’t be managed via traditional spreadsheets or non-industry-specific tools. With proper implementation, the organization is set to handle and share data in a controlled and systematic manner that permits greater granularity, revision control, and confidence when planning for change, be it for new builds or vessels in operation.
A digital-first and always strategy can ensure alignment between Navy and shipyards, through the creation of a deep digital thread and a framework for getting assets in service quicker than before.
The digital innovations that minimize information conversion costs serve as the basis for the first 80% of the journey. The remaining 20% will require further commitment and agreement across the industry to ensure success.
Simon Crook is a Senior Solution Specialist at SSI.
The opinions expressed herein are the author's and not necessarily those of The Maritime Executive.