A Convergence of Technologies Under the Hulls of Boats
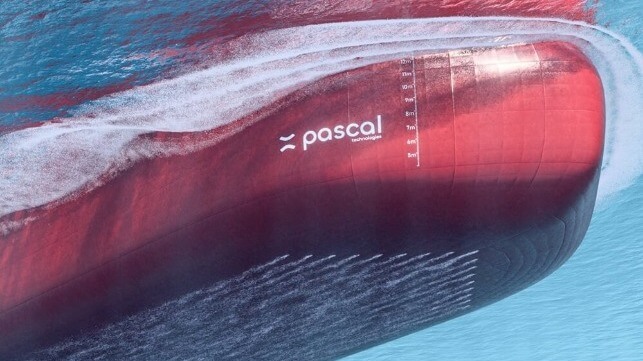
In his classic treatise entitled "Competing for the Future," University of Michigan professor of business Dr. C. K. Prahalad focused on the “convergence of technologies” to develop future products and services. There is potential to combine maritime technologies that pump air below the hull and a large hydrofoil at the stern, to reduce water drag and reduce power requirements on transportation technologies that travel on water for all or part of a journey.
Introduction
During the 1950s, British inventor Christopher Cockerill demonstrated that a large expanse of low-pressure air could carry the weight of a large transportation vehicle, dubbed the hovercraft that could transfer between a water surface and smooth coastal land. A flexible skirt made from rubber surrounded the perimeter of the hovercraft which was introduced into commercial service. Many decades later, Pascal Technologies of Norway and Damen of the Netherlands borrowed from Cockerill’s concept and dispensed with the rubber skirt, pumping air under the hull to partially lifting the vessel from the water and reduce hydrodynamic drag, also reducing propulsive energy requirements.
The history of hydrofoil technology dates back to France during the late 1800s, and involved efforts to raise the speed of row boats. After 2020, a boatbuilder added hydrofoils to an oar-powered kayak that when rowed, lifted its hull above water and accelerated to greater speed. Hull Vane of the Netherlands has developed a unique stern-mounted hydrofoil that re-directs the stern wave behind boats and indirectly reduces water drag and required propulsive power. There is potential to combine technologies from Pascal Technologies, Damen Industries and Hull Vane to improve performance of a variety of vessels.
Inland Waterways
Pascal Technologies and Damen Industries have installed their air pressure technology under several boats hulls. Following activation of the air pumps, vessel hulls rise to higher elevation in the water and reduce the submerged cross-section across the bow, reducing propulsive energy requirements when the vessel is in motion. There is still potential to develop a wave at the stern and installation of technology from Hull Vane re-directs the water drag imposed by the stern wave, further reducing propulsive energy requirements. Authorities in many countries require vessels sailing along inland waterways to produce minimal bow and stern waves.
While vessels that sail on the ocean and on very large inland lakes are at risk of encountering large waves, vessels that sail along inland waterways encounter very small waves produced either by wind or by other vessels sailing in the opposite direction. Vessels with hulls built to the configuration recommended by Pascal Technologies and Damen Industries would sail at higher elevation above shallow sections of waterway, minimizing or eliminating damage to boat hulls while carrying normal commercial payloads. Installing a hydrofoil across the vessel stern would assist in maintaining stern elevation while further reducing vessel propulsive energy requirements.
Hydrofoil Vessels
Large-scale hydrofoil vessels require immense propulsive power to push water around a large submerged bow cross-section and accelerate to sufficient speed to rise up on to the hydrofoils, to produce smoother across choppy water. Designing a large vessel with a hull configuration that includes a recessed chamber filled with pumped air, would allow the vessel to accelerate to hydrofoil lift-up speed, with reduced propulsive energy requirements. The combination of air pressure under the hull and hydrofoil across the stern could allow for development of much larger and much heavier vessels that could sail on hydrofoils at speeds above 20-knots.
Possible applications for air-hull assisted hydrofoil vessels would include ferry services between nearby coastal cities, or between mainland and offshore islands. An American builder of wing-in-ground effect technology, Regent Craft of Boston, has proposed to include low-speed hydrofoils on their vehicles to allow for sailing between port area and open water where the vessel would be able to accelerate to lift-off speed. The initiative by Regent Craft is currently being tested and results so far suggest that their approach would be successful. That initiative provides the basis for future development of vehicles that transfer between waterborne and airborne operation.
Airborne Watercraft
The combined initiatives of Pascal Technologies, Hull Vane and Regent Craft provide the basis for possible future development of large vehicles that transition between travel on water and airborne travel. Large seaplanes may sail on either a large single mono-hull or on twin catamaran type hulls, as is the case with most small seaplanes. The majority of international airports are reaching operational capacity, with future increases projected for airline transportation, both domestically in many nations as well as internationally. Mega-size seaplanes that operate between designated seaplane runways are one possible future alternative for freight and freight transportation.
A future mega-size seaplane or ground-effect plane might combine air pressure being pumped under the hull, transverse stern hull with the possible option of a series of multiple hydrofoils in tandem configuration, placed far below the main hull. The combination offers the possibility of the mega-plane being able to accelerate on the air pressure main hull before making the transition to hydrofoils and then to winged airborne flight mode. Some designs might dispense with hydrofoils and incur take-off weight in excess of two million pounds or 1,000 tonnes, using the combination of air pressure under the hull and stern hydrofoil.
Ground Effect Planes
While the lowest sections of seaplanes are built to maritime structural standards, wing-in-ground effect planes are classified as maritime vessels and entirely built to maritime structural standards, the two technologies also differ vastly in their wing configuration. While seaplane wings guide air flowing over the upper wing surface downward to remain aloft, ground effect wings generate a dynamic below the wing lower surface to remain aloft to an elevation equal to the mean wingspan, for Type-A vehicles. Pilots holding a legally valid boat operator’s license are allowed to operate a Type-A ground effect plane.
Type-A ground effect planes flying at around 100 feet elevation will consume fuel at the same rate as seaplanes flying at 10,000 feet altitude at the same speed. The combination of pilot shortages, the cost of training airline-capable pilots, and future capacity problems at commercial airports enhances the attractiveness of ground effect flight. Combining pumped air under the hull(s), stern hydrofoil and possible hull-above-water hydrofoils enhances the ability of mega-scale ground effect planes to lift above the water surface during acceleration, requiring less overall propulsive power to achieve lift-off speed.
Mega-scale ground-effect planes traveling at 100-feet elevation and 40% the speed as the same size of plane flying at 10,000-feet elevation, would incur fuel savings due lower speed travel. Peak fuel efficiency occurs when the vehicle travels at an elevation of 5% of wingspan, or 10-feet for a vehicle of 200-feet wingspan. Boeing once proposed to build a ground effect vehicle with a wingspan of 500-feet or 153-metres. The market for ground effect planes involves carrying massive volumes of medium priority freight at competitive prices and competitive travel duration, compared to ship and jet air freight.
Conclusions
Combining technical breakthroughs from different and competing groups offers the possibility of improving the competitiveness of several maritime transportation technologies that can sail along inland waterways or raise the hull above water. The convergence of the technologies would apply to future large-scale hydrofoil vessels, future mega-scale seaplanes and future mega-scale wing-in-ground effect planes.
The opinions expressed herein are the author's and not necessarily those of The Maritime Executive.